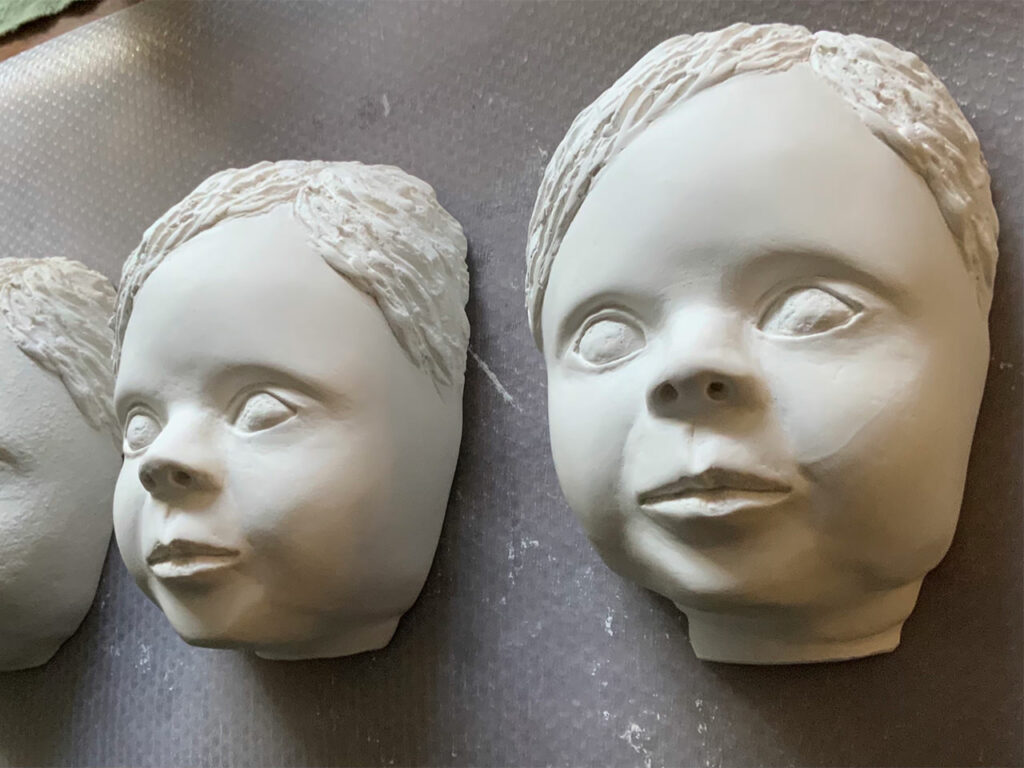
Um von Tonmodellen, in meinem Fall den Tonköpfen meiner Enkel, Abgüsse aus Gips zu fertigen, braucht man eine Negativform des Originals. Gießt man in diese flüssigen Gips, so entsteht eine Positivform, also eine Kopie des Originals.
Und warum dies überhaupt? Eine banalere Begründung wäre das Gewinnen einer Replik, die man verschenken kann…eine ganz andere, erhabenere Sichtweise ist aber diese: durch einen reinweißen Gips entsteht aus einem erdfarbenen Tonkopf eine erhabene, fast überirdische, Zeit und Raum transzendierende Abbildung eines menschlichen Kopfes oder Körpers.
Und so wirken auch viele der in der Gipsformerei der staatlichen Museen zu Berlin hergestellten Repliken klassischer Skulpturen (www.museumsportal-berlin.de/de/museen/gipsformerei; www.gipsformerei-katalog.de) aus feinstem Alabaster-Gips, die dort seit 200 Jahren hergestellt werden und deren Sammlung mittlerweile 7000 Objekte umfaßt.
Diese Eindrücke, früher bei zahlreichen Museumsbesuchen gewonnen, waren letztendlich wohl irgendwie der Motor für mich, in die Technik der Gipsabformung einzusteigen – autodidaktisch und daher nicht ohne Rückschläge beim Praktizieren.
Zunächst mußte ich mich mit der Negativabformung befassen, wobei mir die Wahl schwer fiel: Latex und Alginat als Abformmaterialien erschienen ökologisch attraktiv, sind aber nicht so stabil durch Alterung/Schrumpfung. Trotz anfänglicher Ressentiments kam ich dann doch auf das Silikon! Nach intensiver Recherche mußte ich nämlich zum Schluß kommen, daß es tatsächlich doch besser ist als sein Ruf: für seine Herstellung werden keine fossilen Rohstoffe benötigt, es ist ungiftig, kommt ohne Weichmacher aus, ist reißfest, flexibel, aber lange haltbar und dazu noch erschwinglich.
Das Eintauchen in die Welt der Silikonverarbeitung überrumpelte mich schon, hatte ich doch keine Ahnung von der Vielfalt angebotener Produkte. Letztendlich aber wurde klar, daß sog. RTV-Silikone (Raum-Temperatur-Vulkanisation) das Mittel der Wahl sind für die künstlerische Abformung.
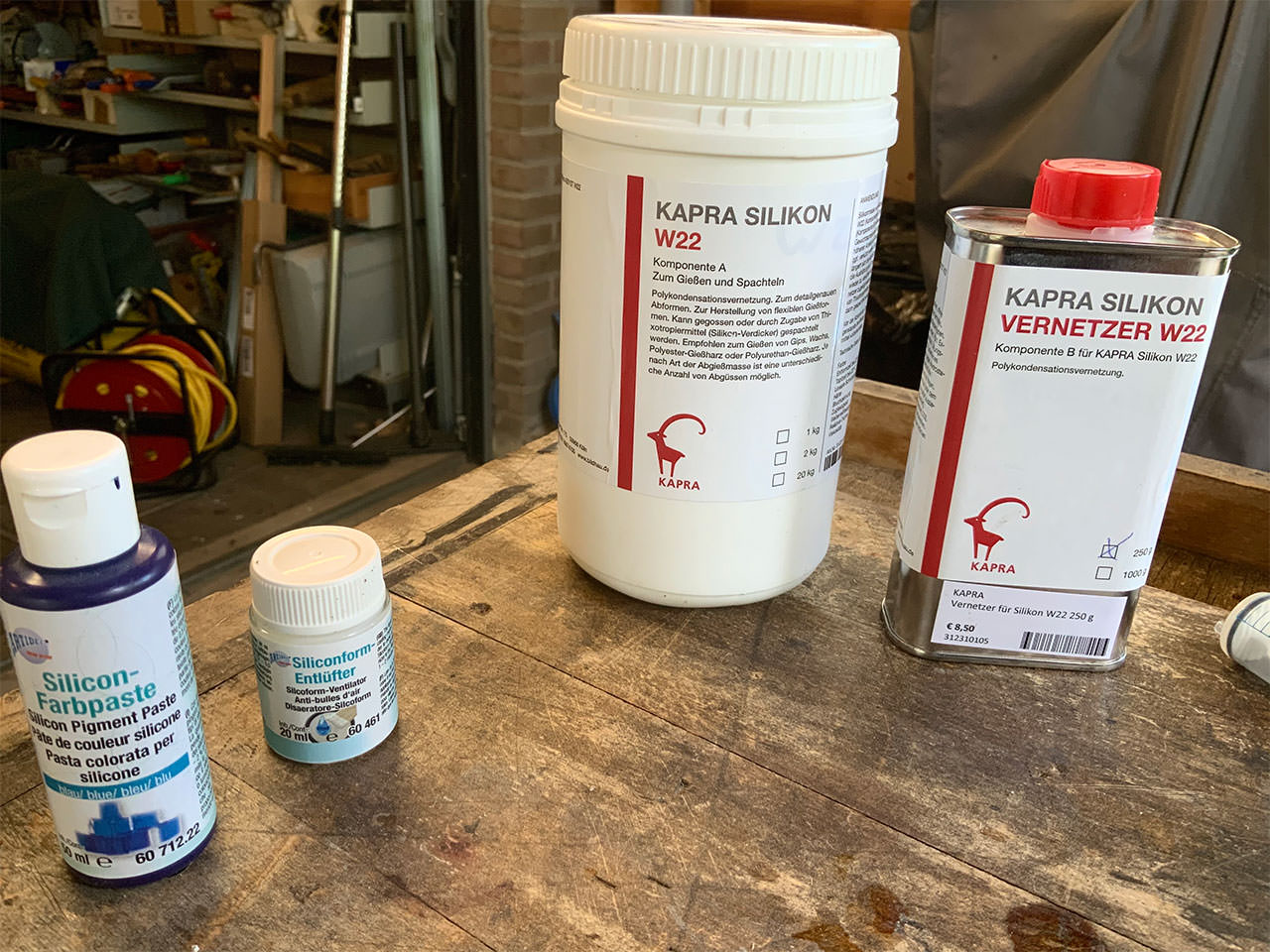
Genauer genommen sind es RTV 2-Silikonkautschuke, die im Gegensatz zu den im Baumarkt erhältlichen, zum Kleben und Abdichten benutzten Einkomponenten Silikone (RTV 1), als gieß- oder streichbare Massen durch Zugabe von sog. Vernetzern bei Raumtemperatur zu elastischen Formen vulkanisieren, daher auch Zweikomponenten-Silikone genannt.
Durch hohe Abformgenauigkeit werden kleinste Details abzuformender Oberflächen abgebildet – bei geringer Schrumpfung. Allerdings sind die Mischungsvorgaben und die empfohlene, ziemlich warme Zimmertemperatur von 23°C möglichst exakt einzuhalten, da es sonst zu erheblichen Abbindeverzögerungen kommt. Eine blasenfreie Aufbringung ist möglichst zu erreichen, also am besten die erste dünnflüssige Schicht mit einem Kurzhaarpinsel aufbringen, dann später zähere Schichten aufstreichen/aufspachteln, so daß insgesamt eine etwa 1cm dicke Silikonmantelschicht um das abzuformende Modell entsteht.
Vor jeglicher Abformung jedoch muß die poröse Oberfläche eines Modells aus gebranntem Ton oder Gips versiegelt werden mit Polyvinylalkohol (PVA) oder Schellack. Bei letzterem verbleibt jedoch ein glänzender Überzug auf dem Objekt – Geschmacksache. In beiden Fällen sollten dann aber noch Trennwachs (für besonders glatte Silikonoberflächen) oder Trennspray (PTFE) dünn aufgetragen werden, damit sich später die Silikonschicht leicht vom Modell trennen läßt.
ERSTE SCHRITTE
Meine anfänglichen Erfahrungen waren nicht ohne Rückschläge: es begann mit der ersten dünnen Schicht, die ich aufgegossen hatte, aber partout nicht trocknen wollte – trotz Fön (wegen der winterlichen Temperaturen in meiner Werkstatt).

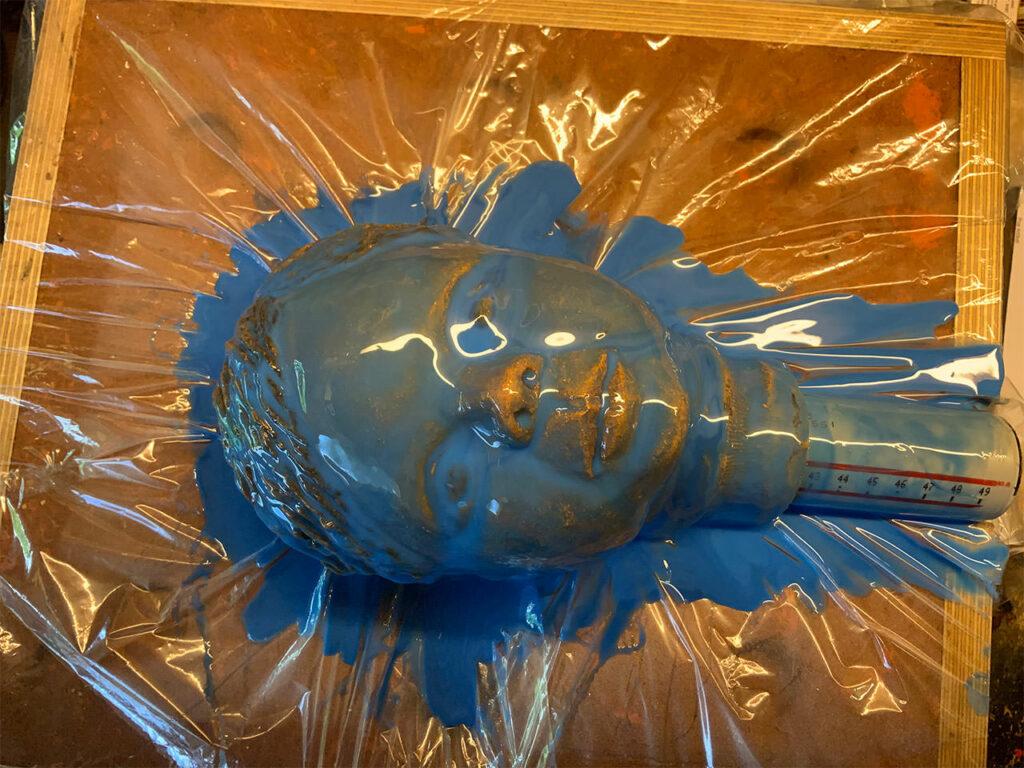
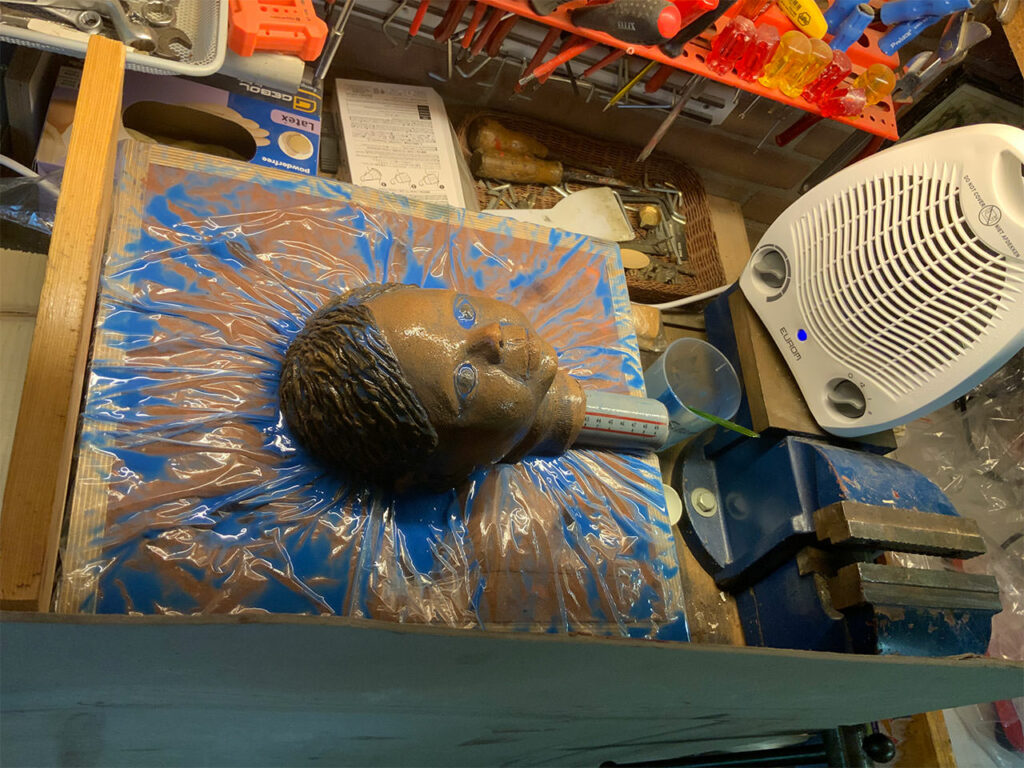
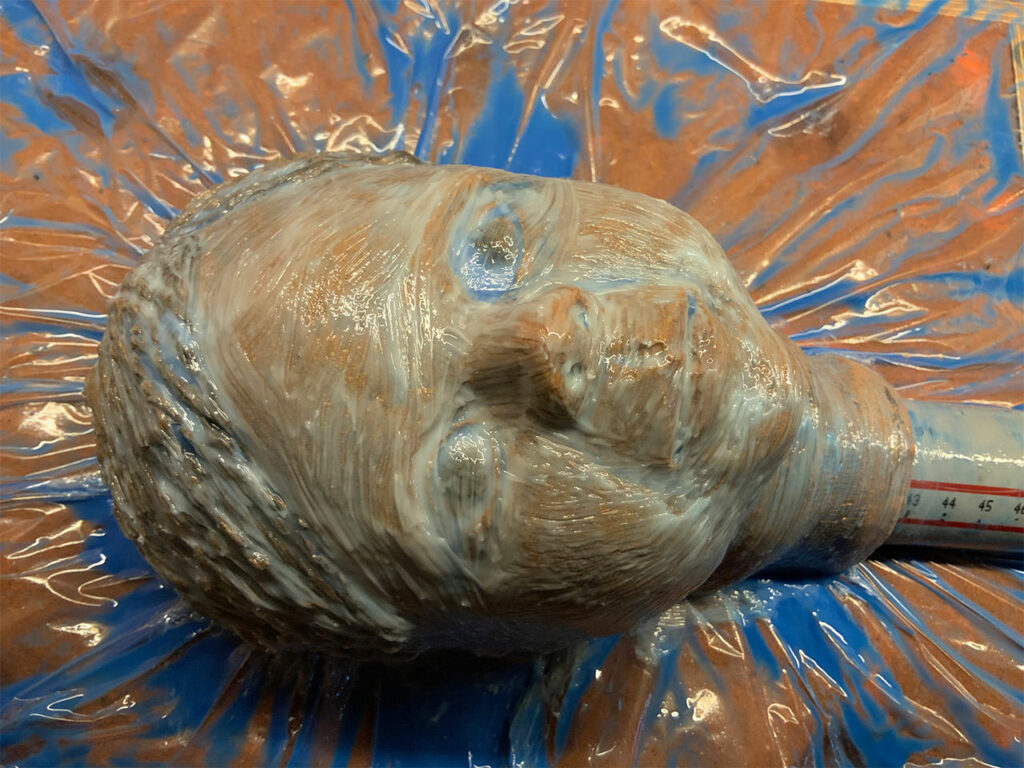
Nach 1 1/2 Wochen nicht-enden-wollenden Festwerdens gab ich dann gegen alle Regeln Vernetzer pur dazu und alles setzte sich binnen kurzer Zeit und ich konnte die zweite Schicht aufbringen, die etwas zähflüssiger gelang mittels Verdickungsmittel. Grund der ganzen Misere war letztendlich mein eigener Fehler: ich hatte das Mischungsverhältnis Silikonöl/Vernetzer nicht korrekt eingehalten, hätte doch exakt 100:5 sein sollen. Also: künftig immer mit der Waage arbeiten! Und: noch vor dem Silikonauftrag immer besser noch Trennspray auf das Tonmodell aufbringen. Schließlich addierte ich mehrere Schichten auf, die ich anfangs aus Sorge um zögerliche Vernetzung (= Festwerden) im Tagesabstand aufbrachte. Dies ist jedoch eigentlich nicht nötig, denn man kann folgende Schichten schon gemäß der „Fingerprobe“ aufbringen: beim Fingerabdruck sollte das Hautmuster stehenbleiben; das Silikon muß aber nicht komplett durchgehärtet sein. Die Silikonschichten verbinden sich nämlich später vollständig miteinander, werden zu einer mantelartigen Hülle, die dann abgezogen werden kann.
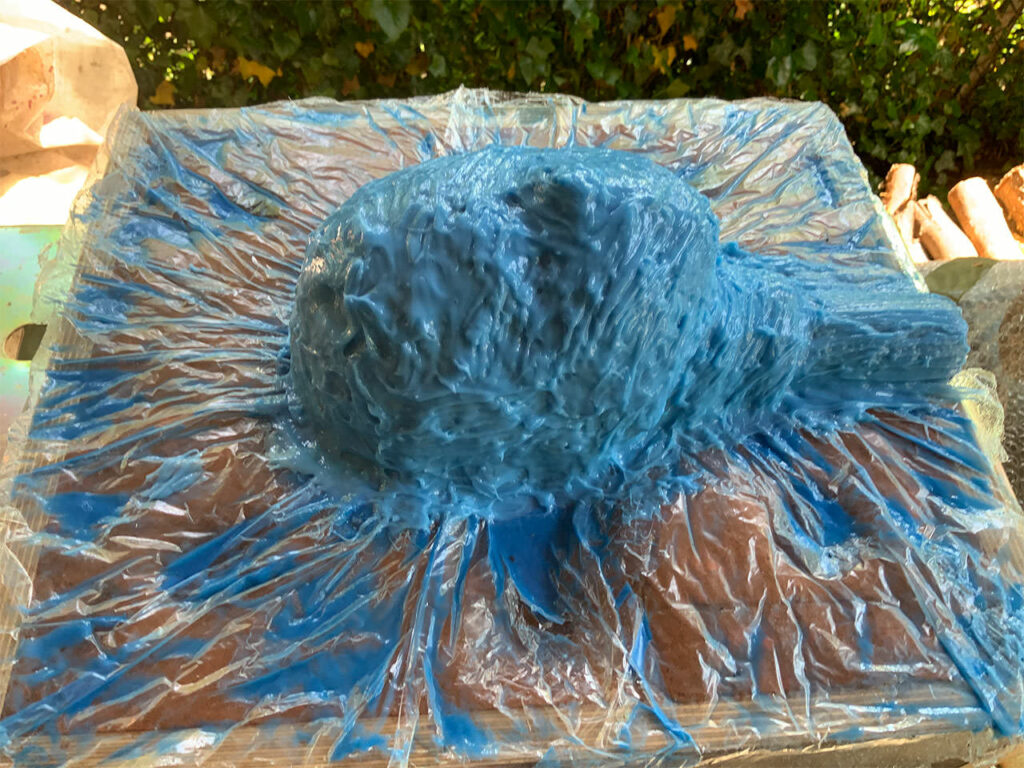
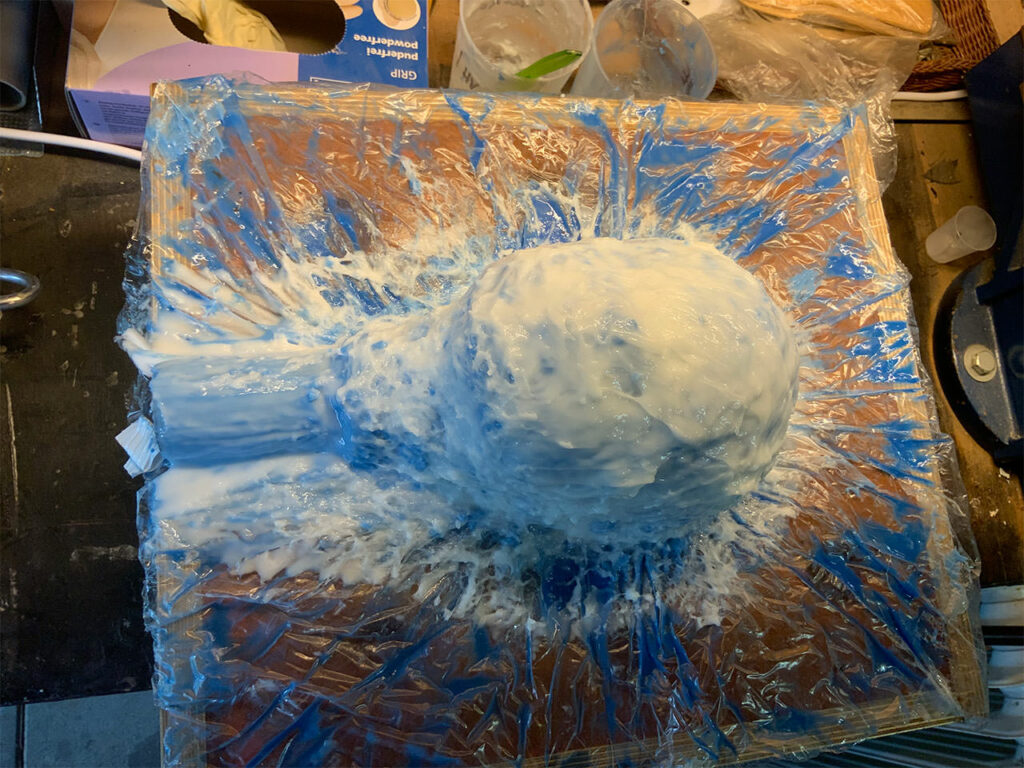
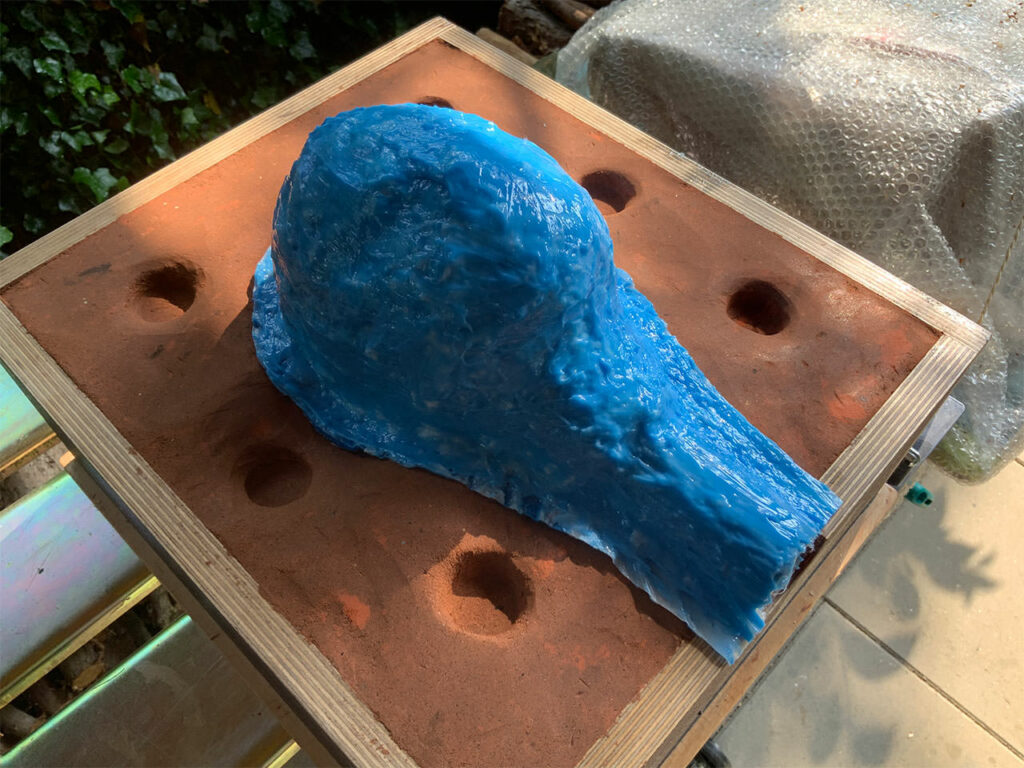
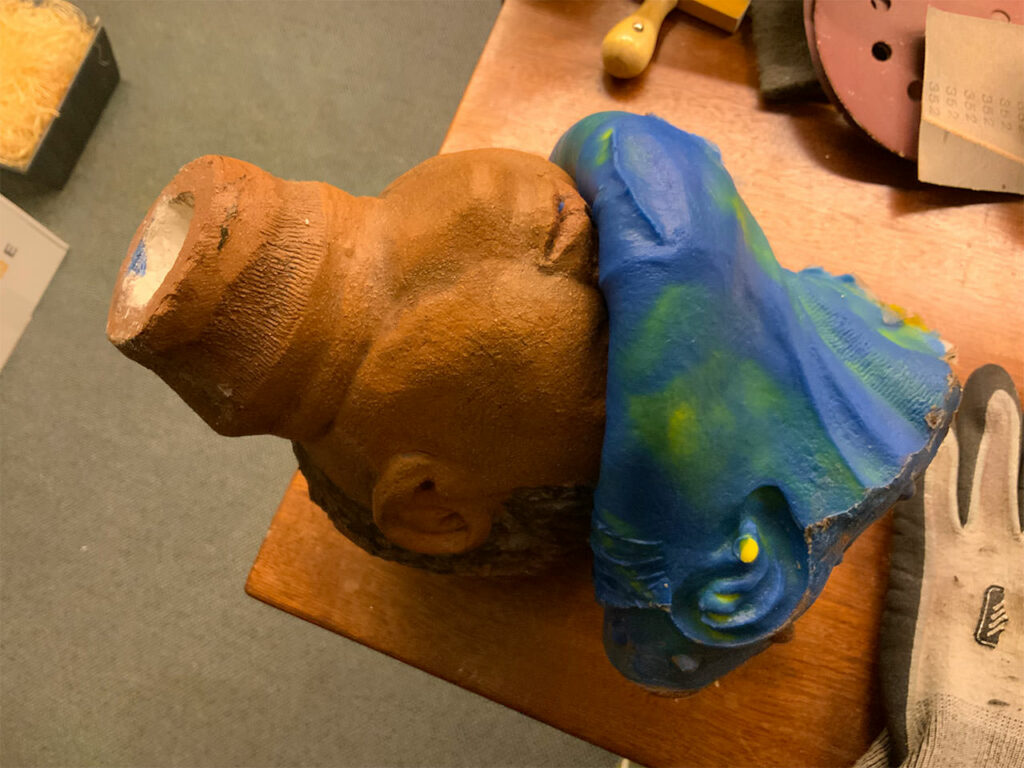
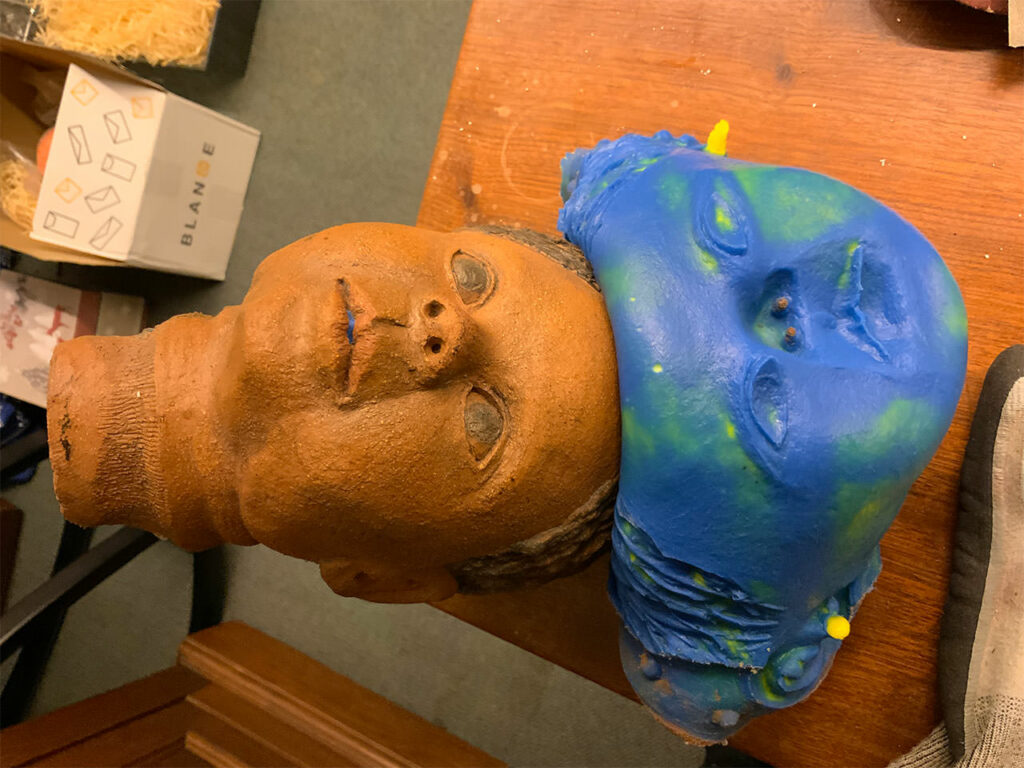

DAS PROBLEM DER FORM
Anfangs entschied ich mich für eine zweiteilige Form, bei der ein Adapterrand mit Passmarken im Silikon angelegt werden muß – siehe die halbkugeligen Erhebungen bzw. Mulden auf der Gegenseite. Dazu baute ich einen zweistöckigen Formkasten, wobei ich den unteren Kasten mit Ölsand füllte und den Tonkopf darin einbettete: erst zur Abformung der Gesichtsseite, dann nach Umdrehen war die Haarseite dran.
Aber dies würde ich heute definitiv einfacher gestalten, da es bei einer einfachen Form wie dem gezeigten Tonkopf auch mit einem kompletten Silikonüberzug gelingt, das Modell herauszulösen – oder mit nur einem kleinen Hilfsschnitt an der Rückseite.
Damals aber hatte ich zuerst den Ölsand mit Frischhaltefolie abdeckt, um die Vorderseite des Kopfes mit Silikon abzuformen…und um späteres mühseliges Säubern des Haarschopfes zu vermeiden. Weit gefehlt jedoch, denn die weit üblere Folge war, daß das zu allererst aufgebrachte dünnflüssige Silikon auf der Folie sogar noch auf die Rückseite des Tonkopfes lief und somit gestaltete sich die spätere Reinigung noch weitaus aufwändiger.
Und da zwischen der ersten und den folgenden Silikonschichten aufgrund der viel zu spät gelungenen Abhärtung so viel Zeit vergangen war, blieben von der ersten dünnen Schicht Rückstände auf dem Tonmodell kleben – auch hier war wieder mühselige Reinigungsarbeit angesagt. Dies Malheur passiert jedoch nicht beim zeitnahen Aufbringen der einzelnen Silikonlagen – die miteinander quasi verschmolzenen Schichten lassen sich en-bloc ablösen.
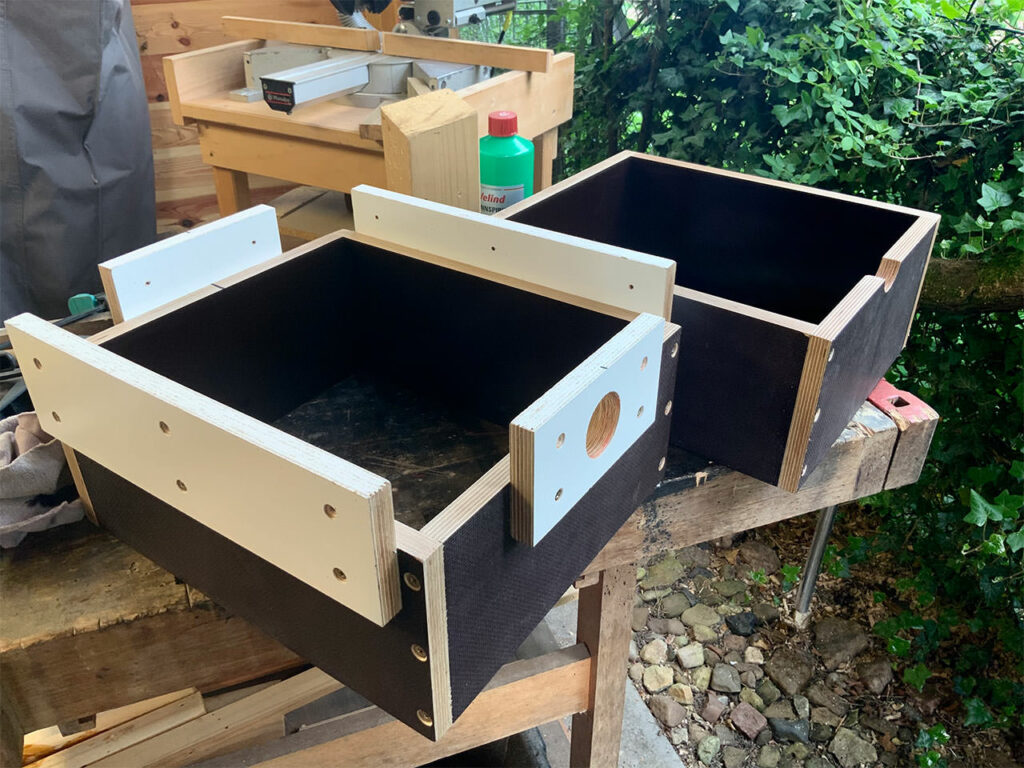
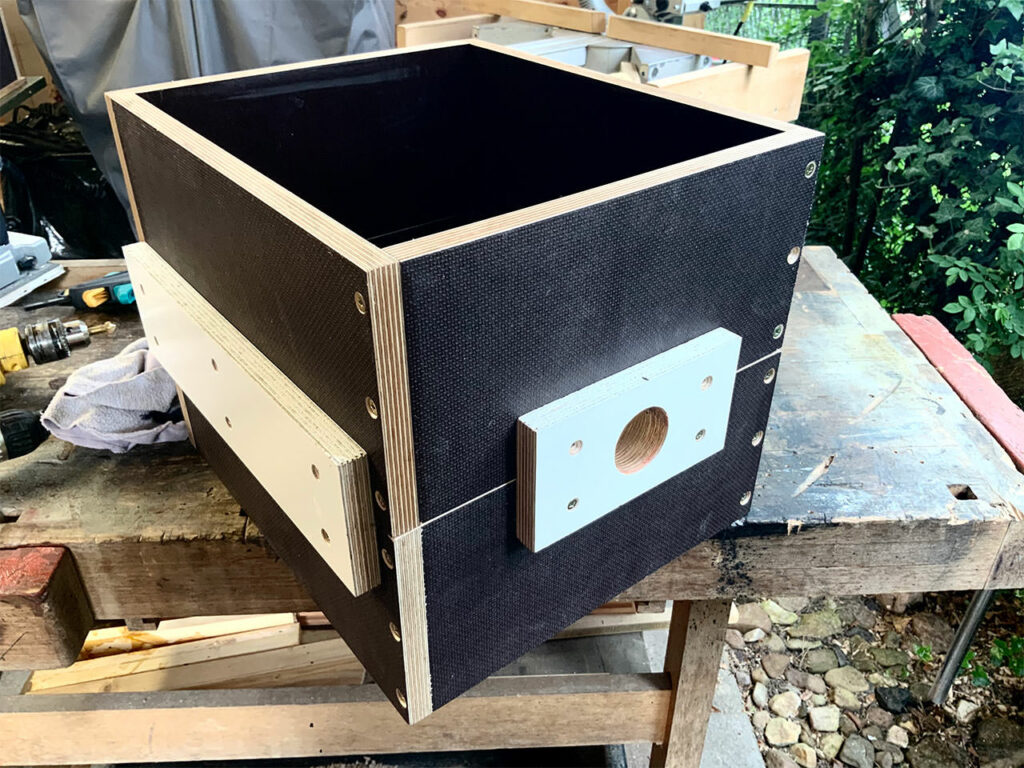
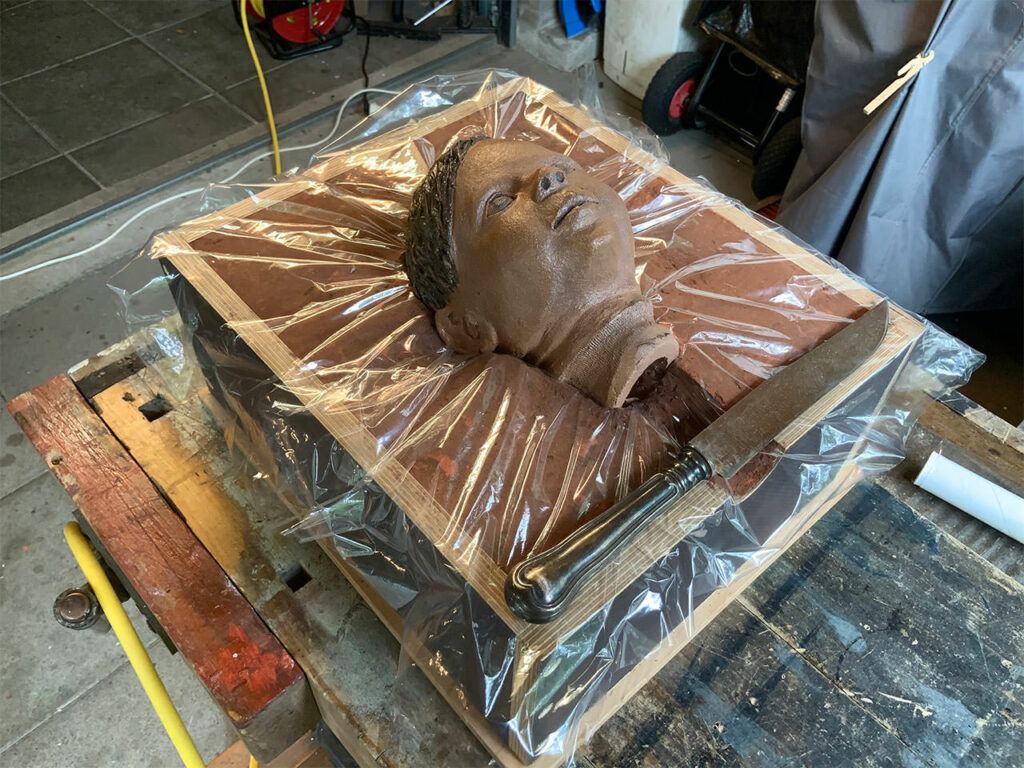
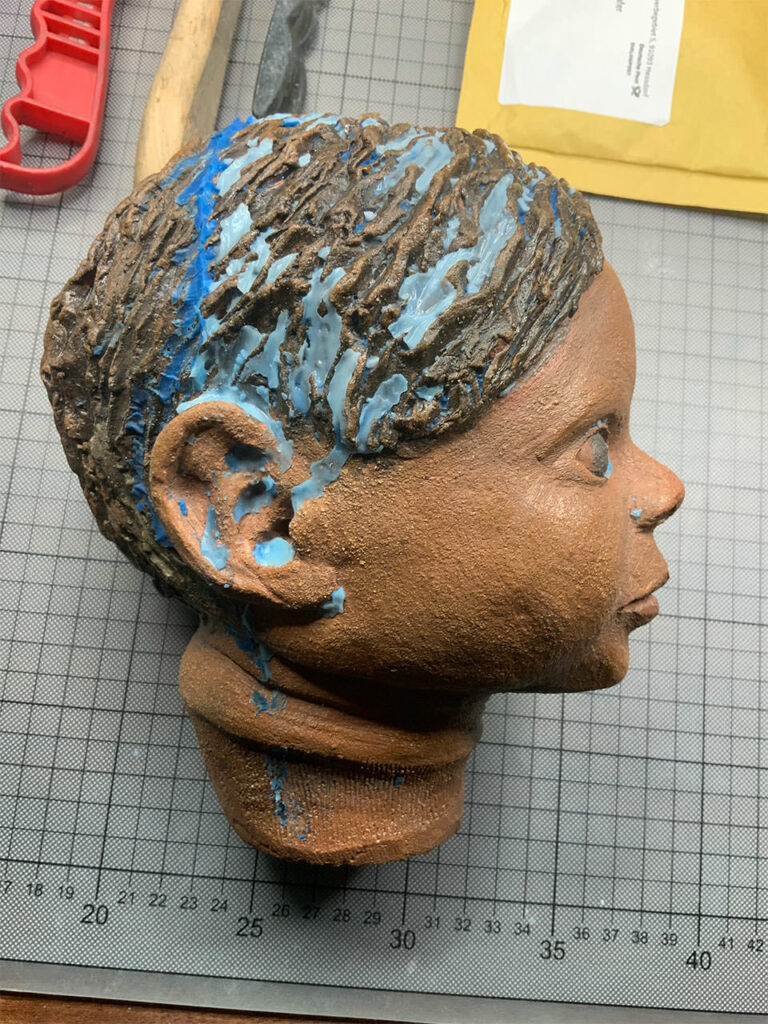
Als nächsten Schritt galt es, das Hinterlaufen von Flüssigsilikon zu vermeiden und hier nutzte ich die beim Bronzeguß übliche Methode: die Anlage eines Walles aus Plastilin (Knete), und zwar entlang einer Linie optimaler Trennbarkeit der zwei zu schaffenden Silikonmantelhälften. Obendrein lassen sich so halbkugelige Paßmarken im Plastilinkranz einbringen, die später das Feder-in-Nut-Passen beider Silikonteile ermöglichen.

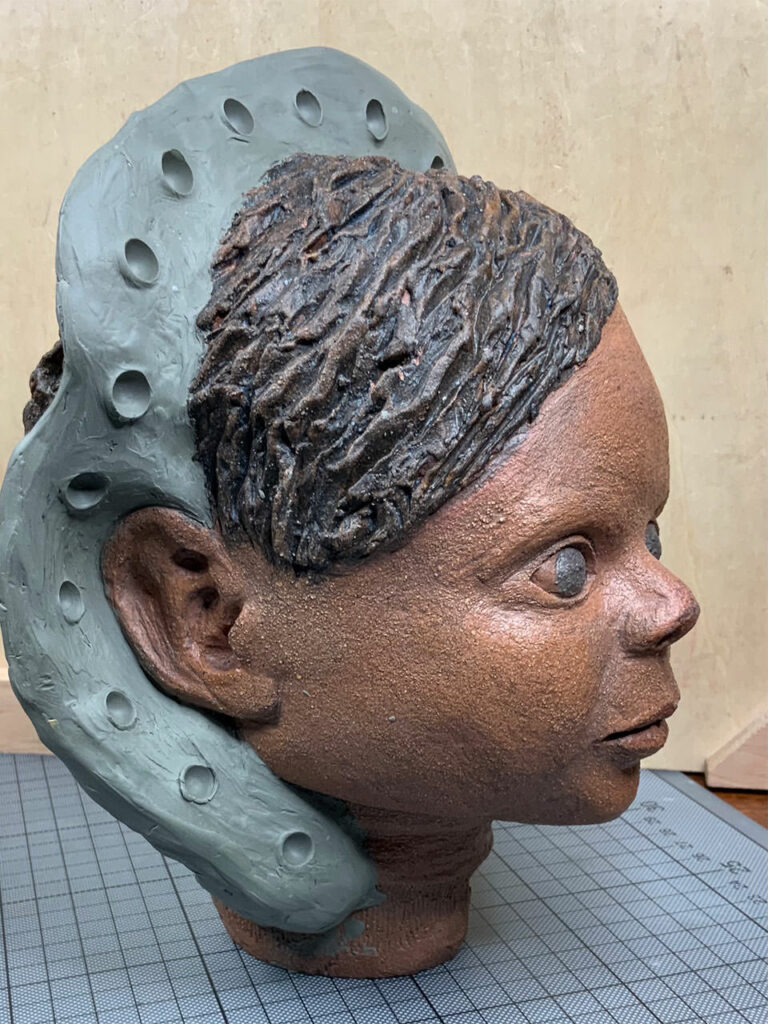
Der Silikonmantel – gleich ob zwei- oder einteilig – erlaubt zwar eine präzise Abformung, aber es bedarf eines äußeren festen Stützmantels, um später den Fließgips einzufüllen und die reale Form auch beizubehalten.
So war der Formkasten auch gedacht, nämlich preiswerten, einfachen Elektrikergips in den zweiten aufgesetzten Kasten zu gießen und so zunächst eine einseitige äußere Halteform zu schaffen, in die die Silikonabformung fest eingebettet war.
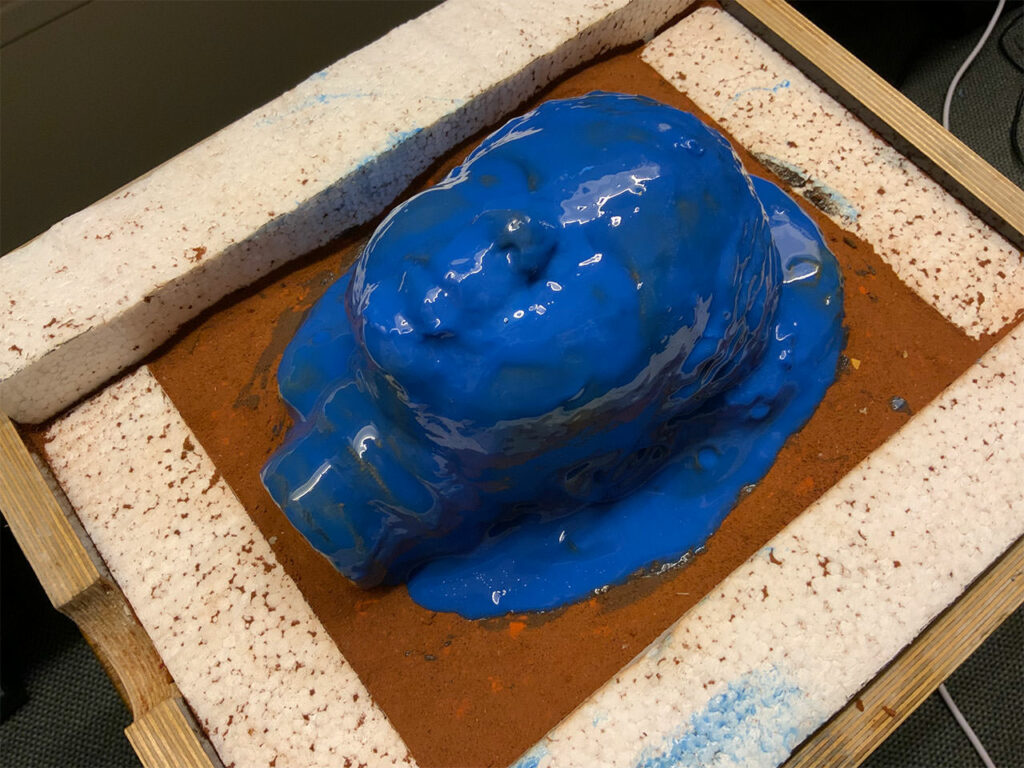
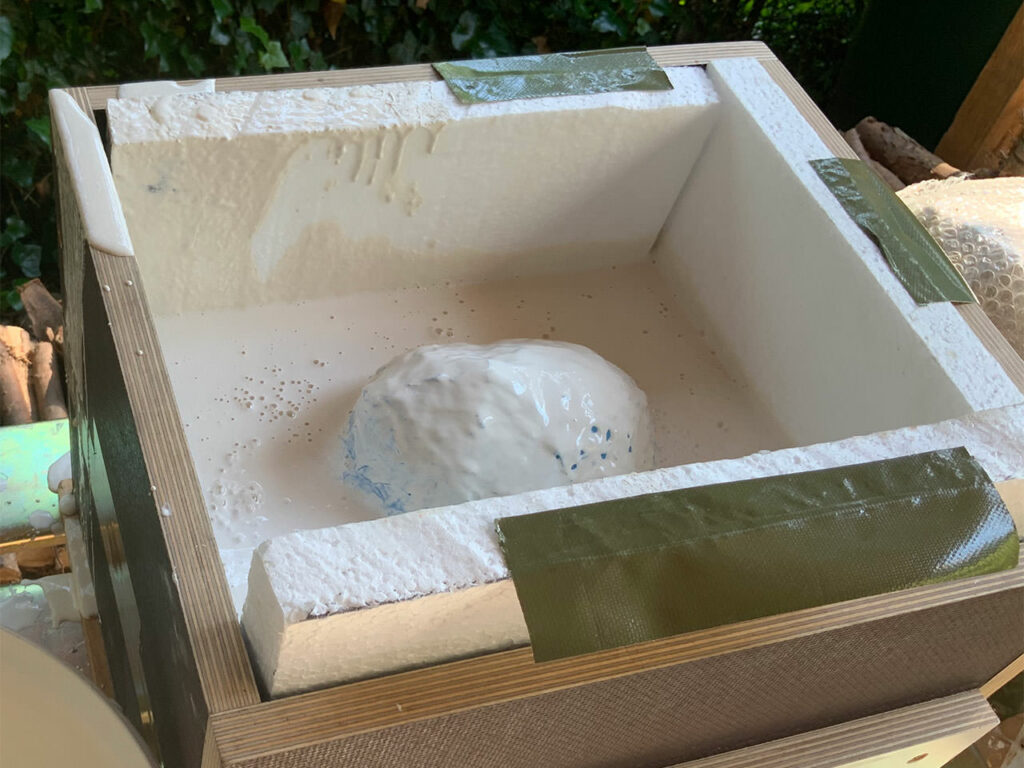
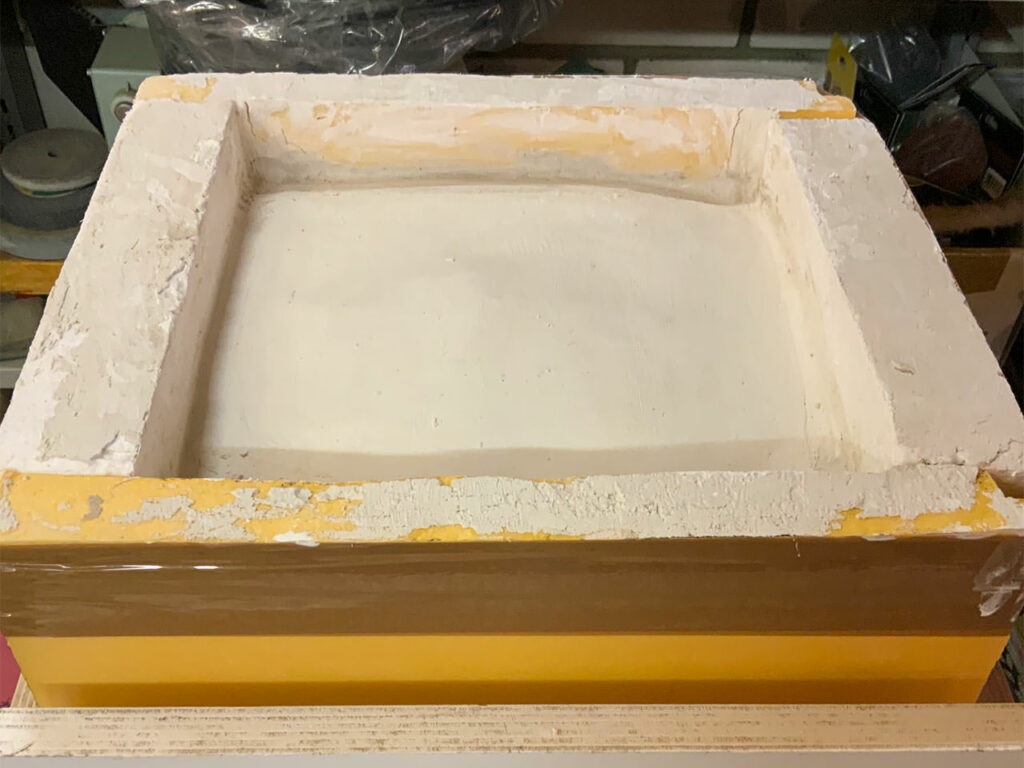
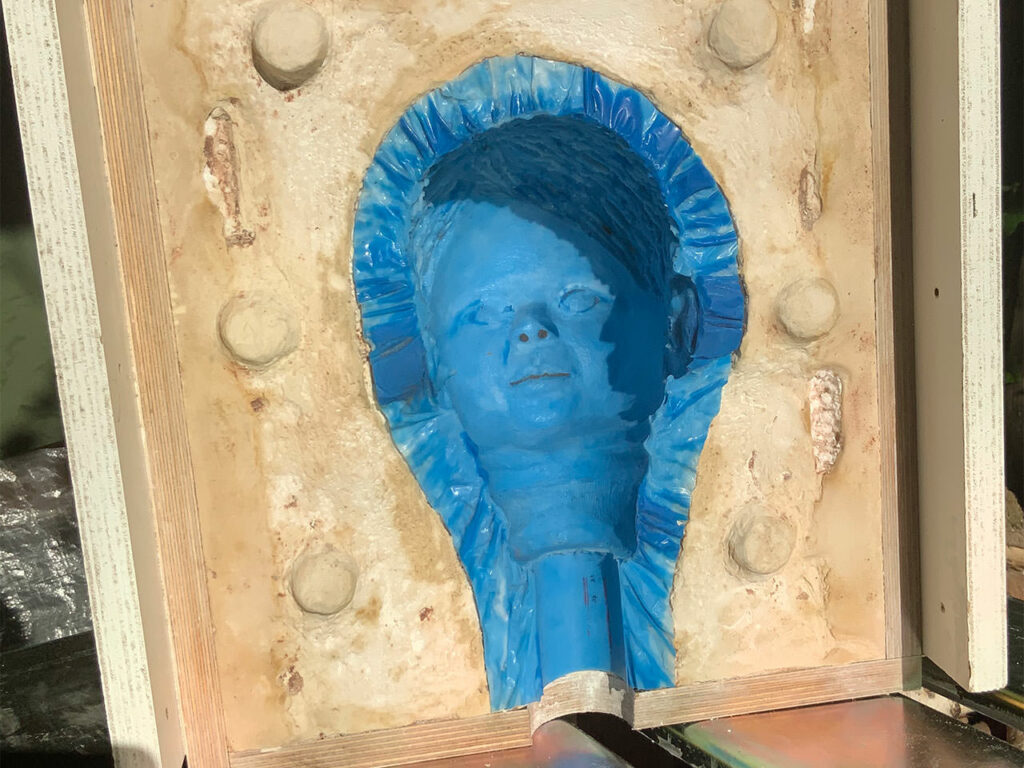
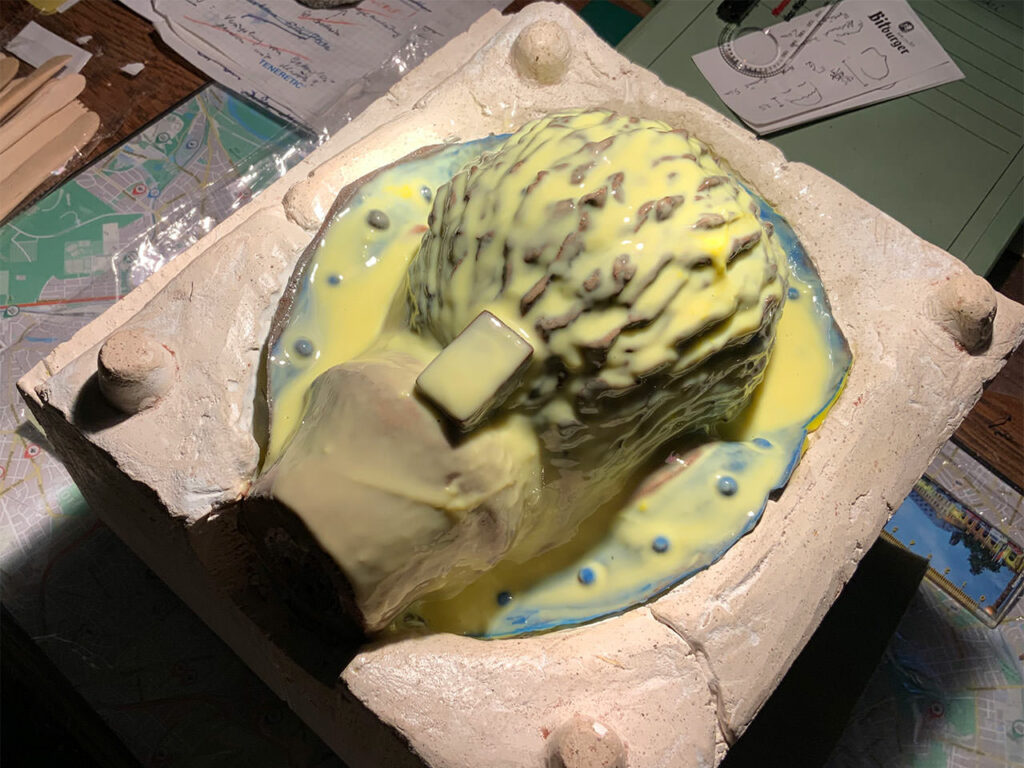

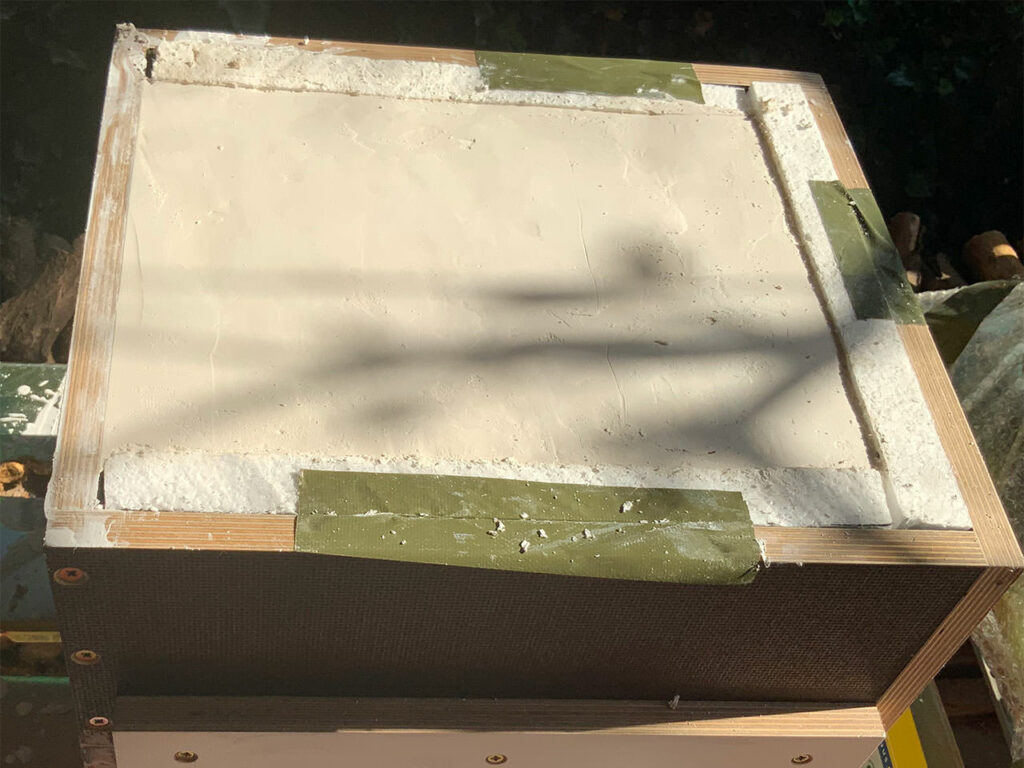
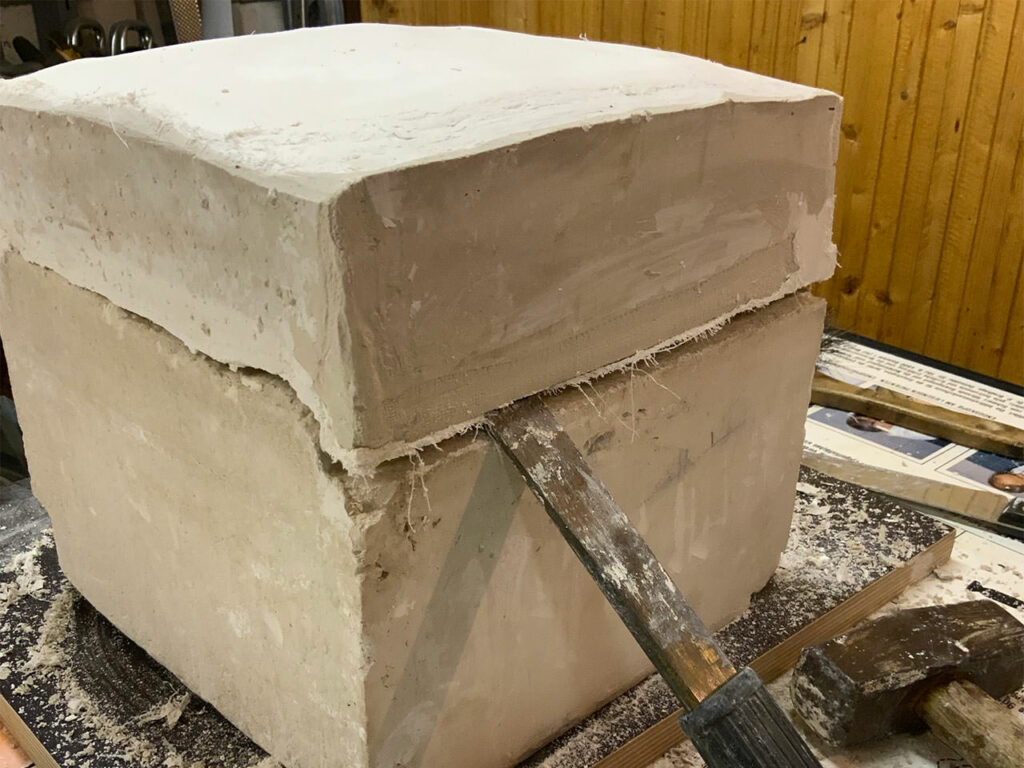
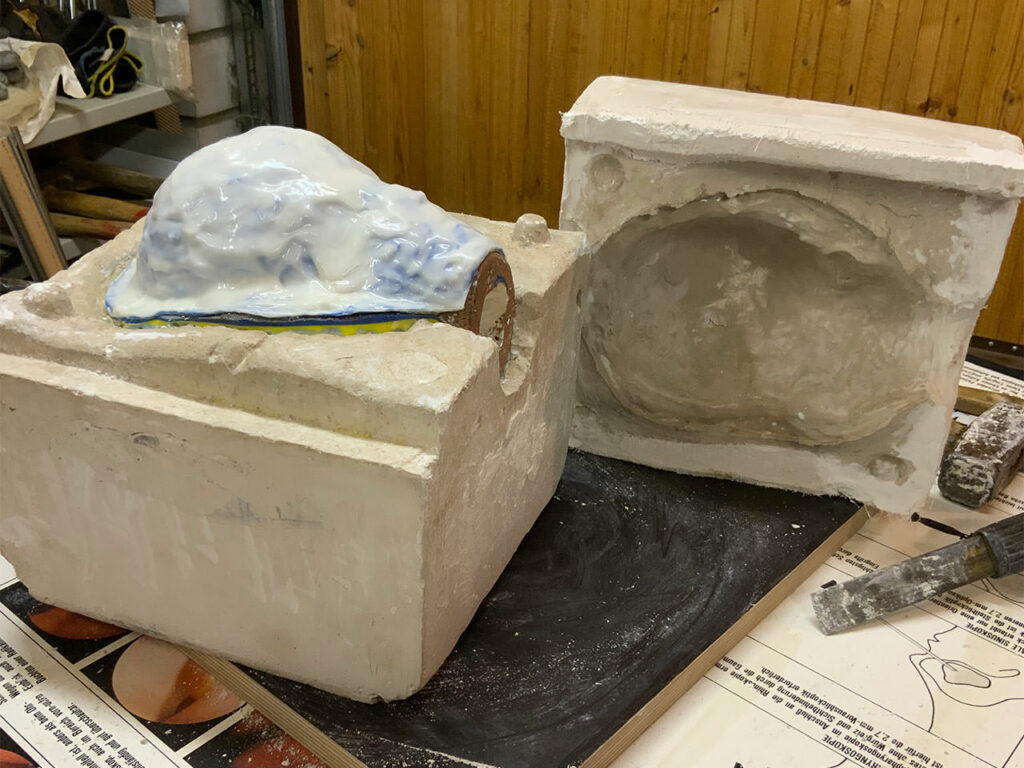
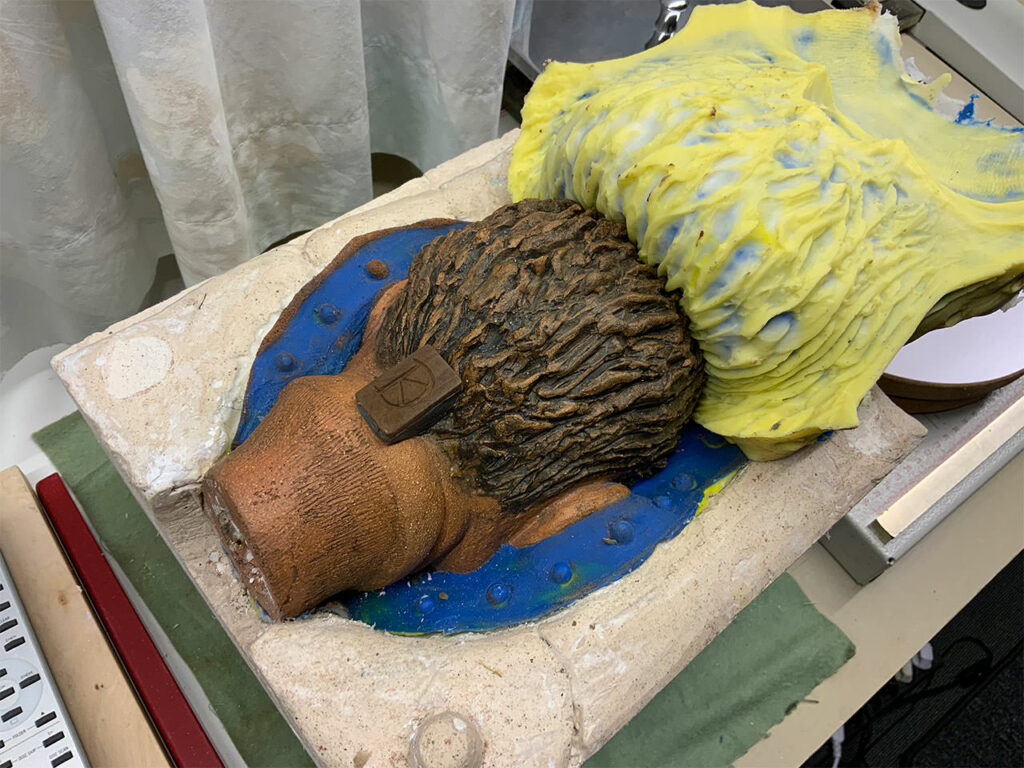
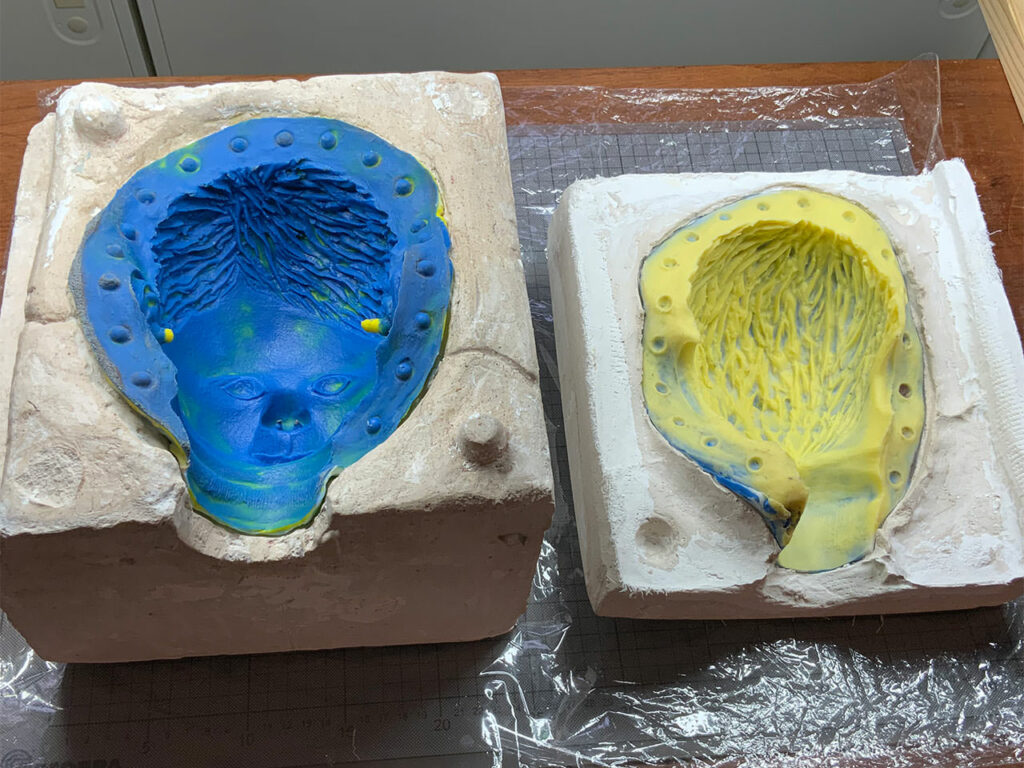
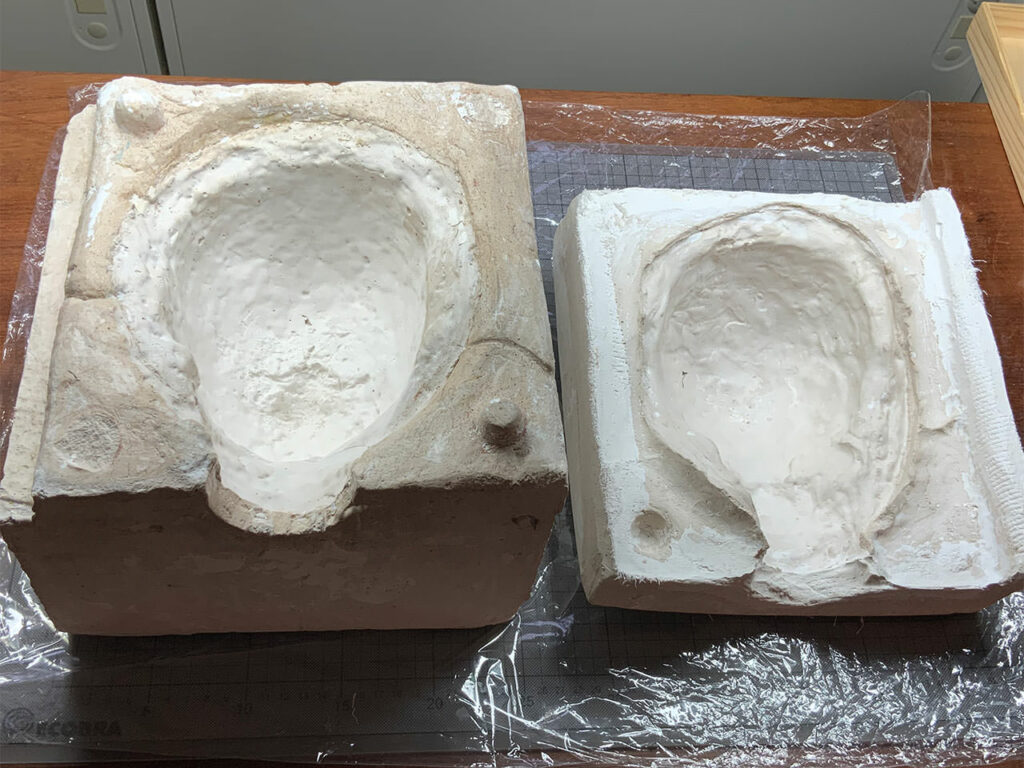
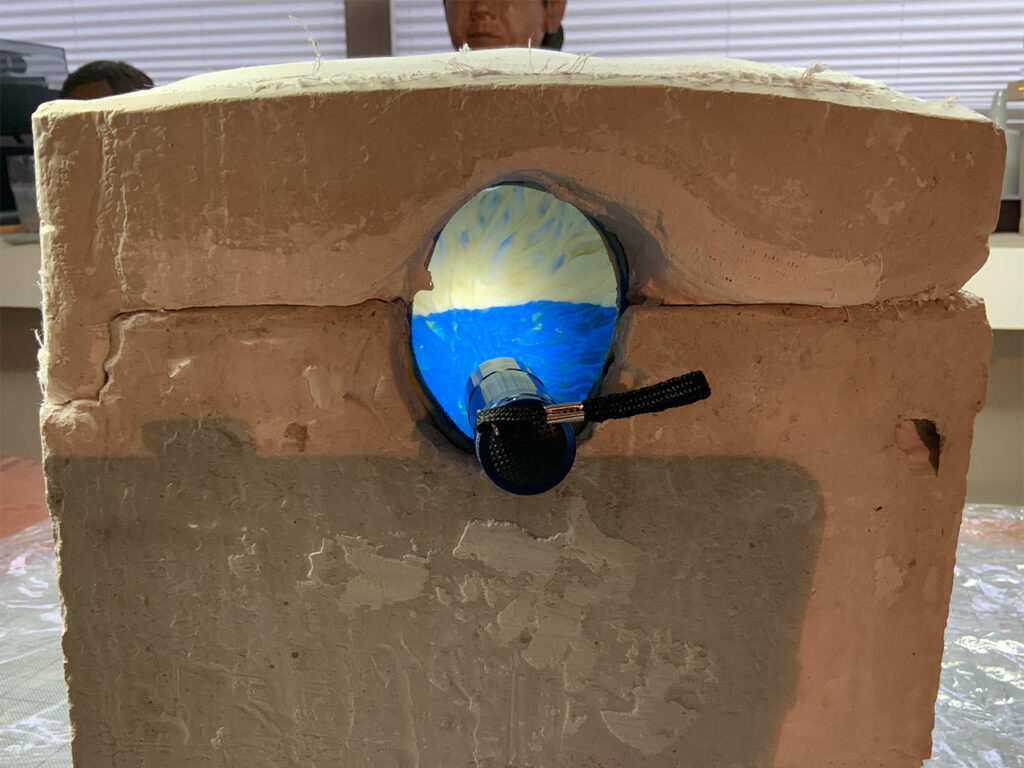
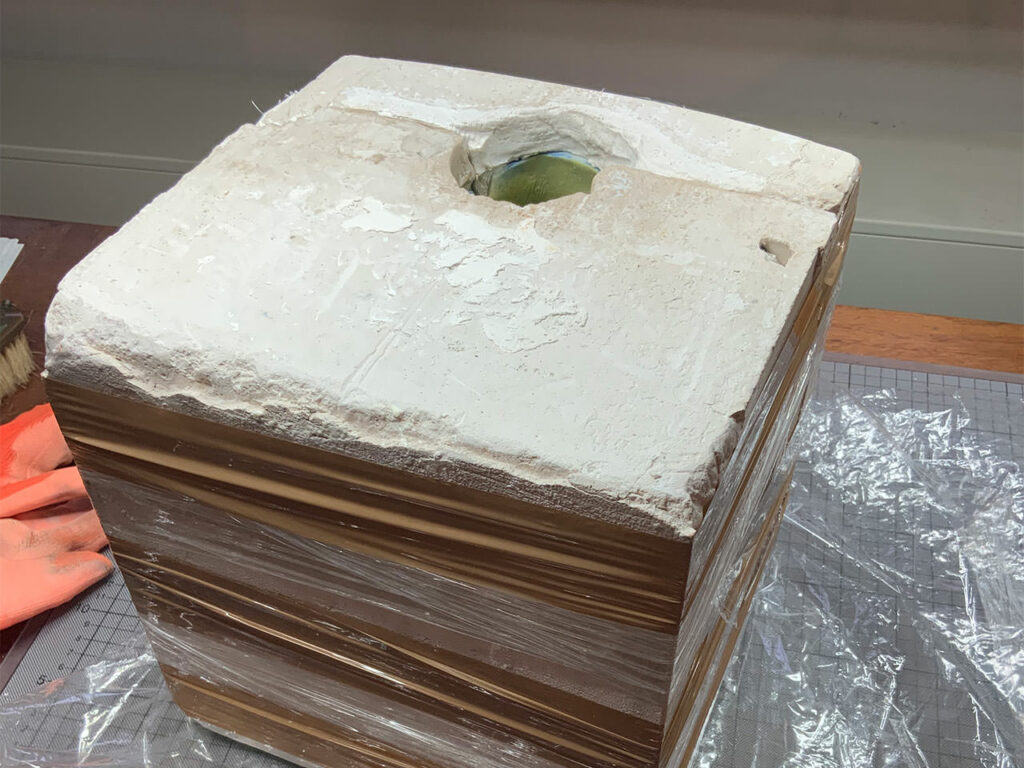
Durch die so erhaltenen zwei Silikonmäntel und die aufgegossenen Gipshüllen erhielt ich schließlich die komplette Gießform – fertig zum Einfüllen eines hochwertigen Fließgipses.
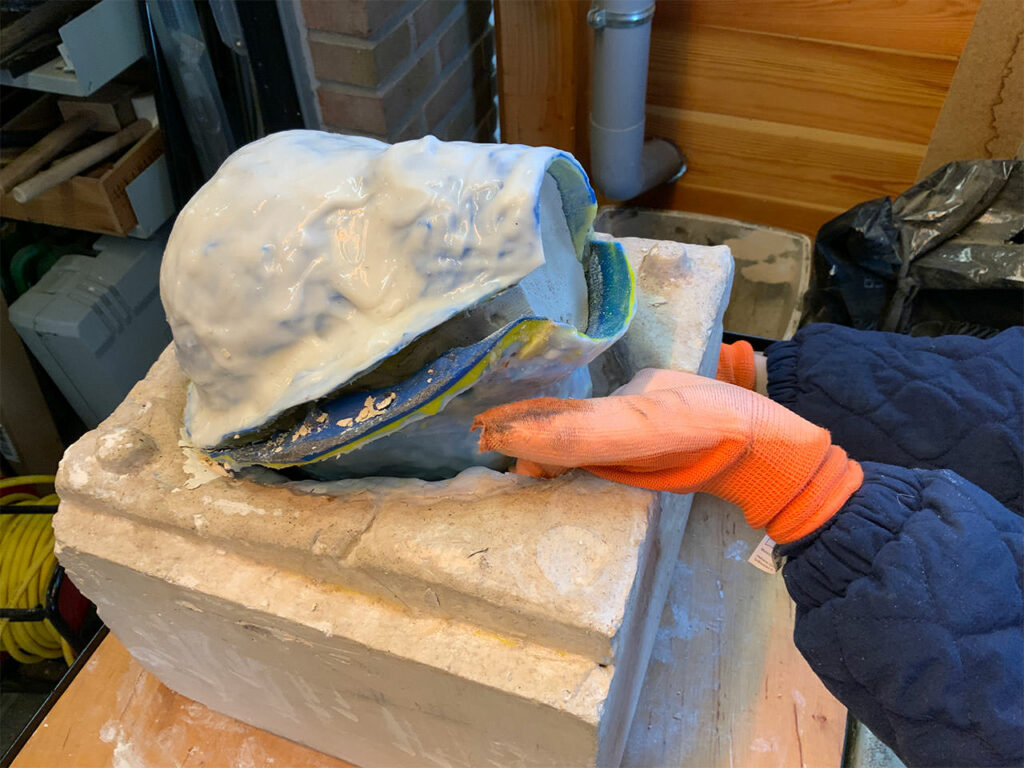
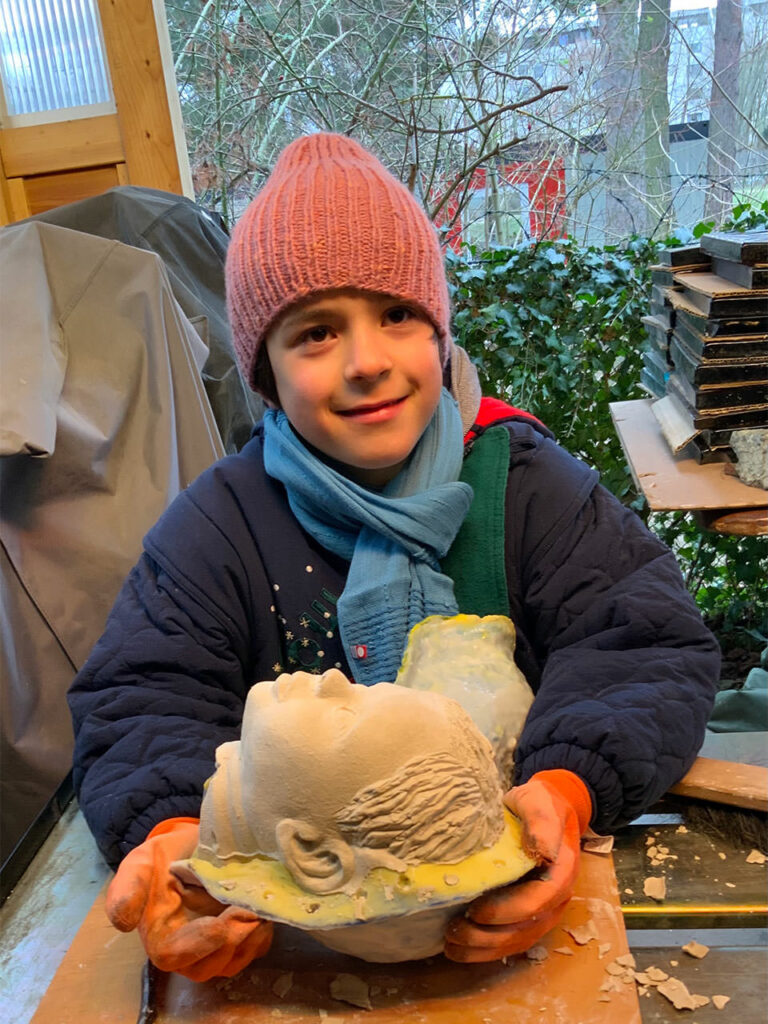
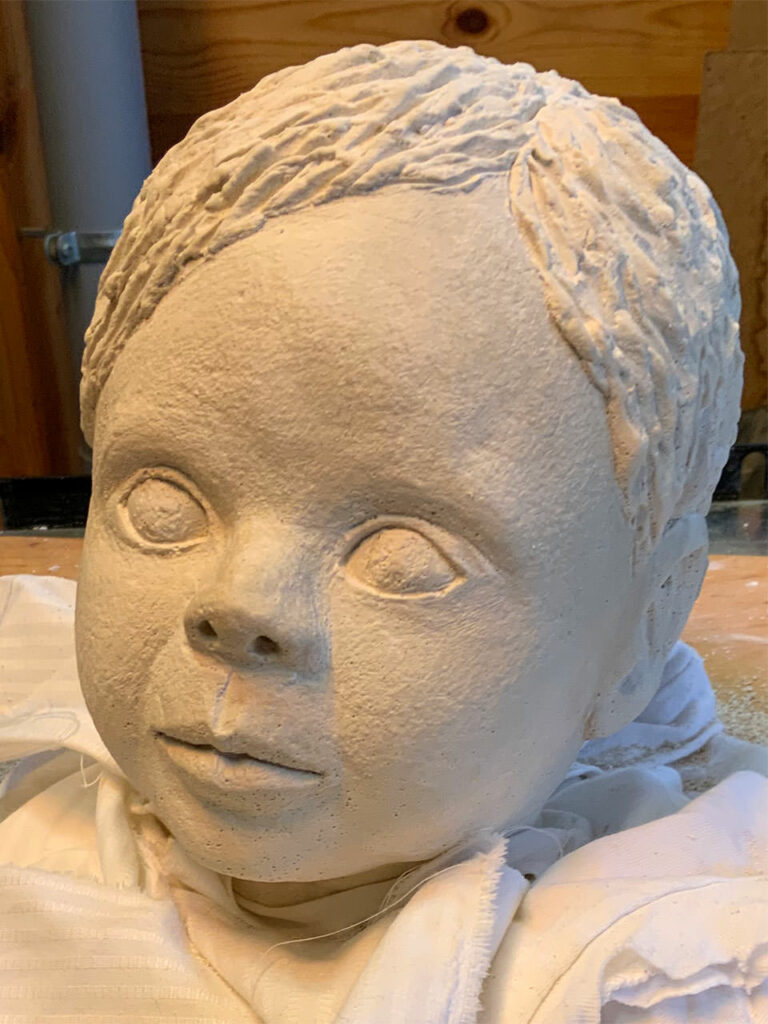
Mit der äußeren Gipsform experimentierte ich aber dennoch, da die erste Blockform so massiv war, schlecht und nur langsam austrocknete. Und so versuchte ich es zunächst mit einer dünneren Gips-„Kappe“ und schließlich auch mit einer komplett dünnen Gipshülle mittels Gipsbinden. Beide Strategien mußte ich jedoch verwerfen, da das Gewicht des eingegossenen Gipses zu einer Leckage an den Rändern der zweiteiligen Silikonform führte: Fließgips trat also aus trotz der äußeren Gipsschale.
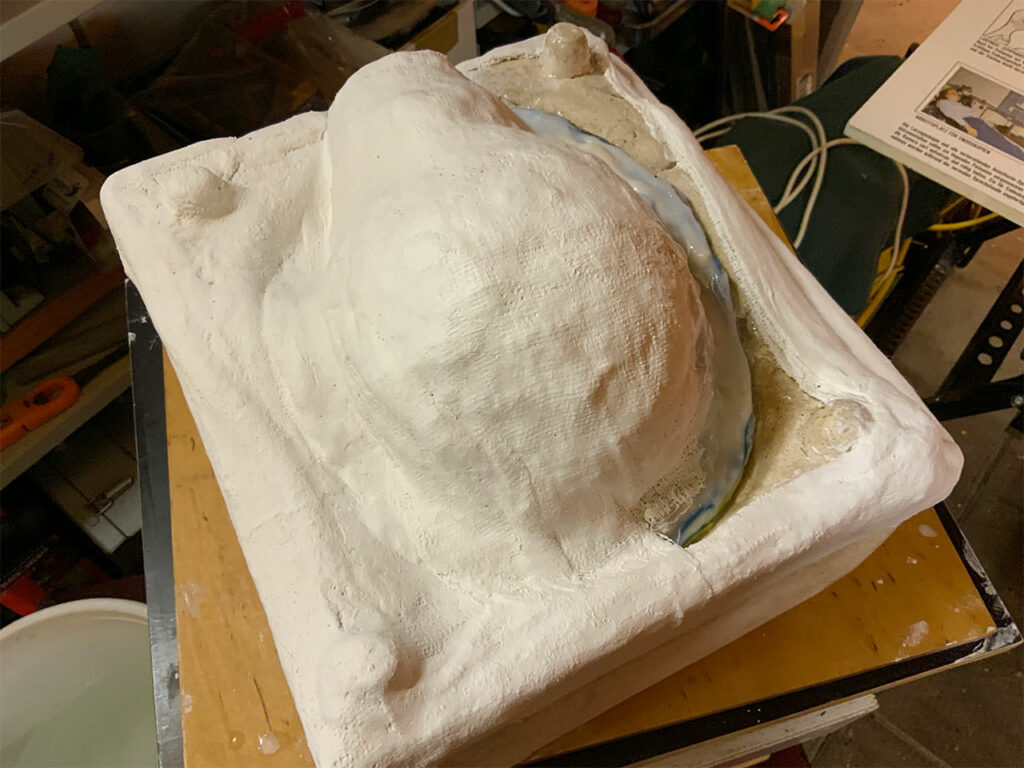
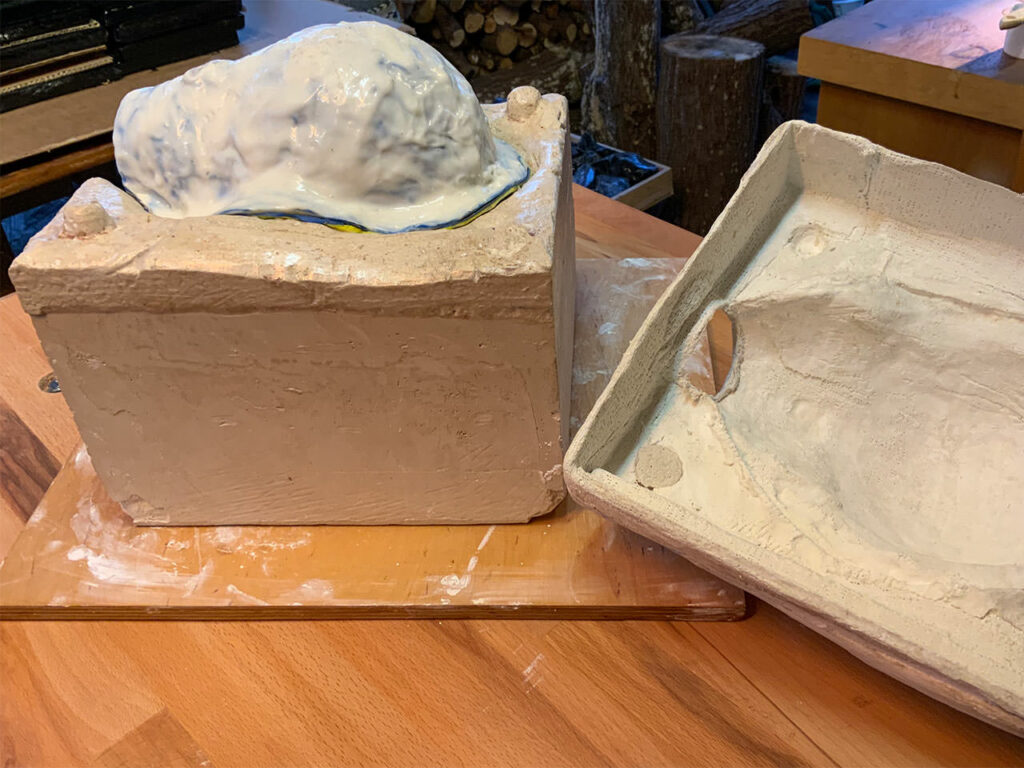
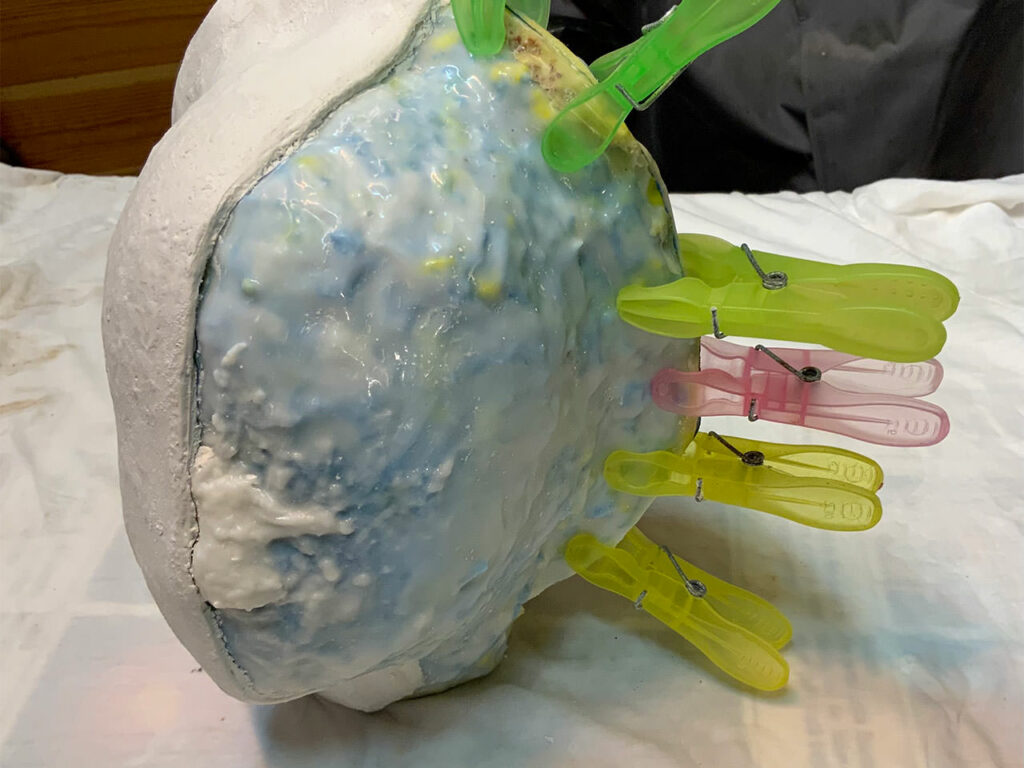
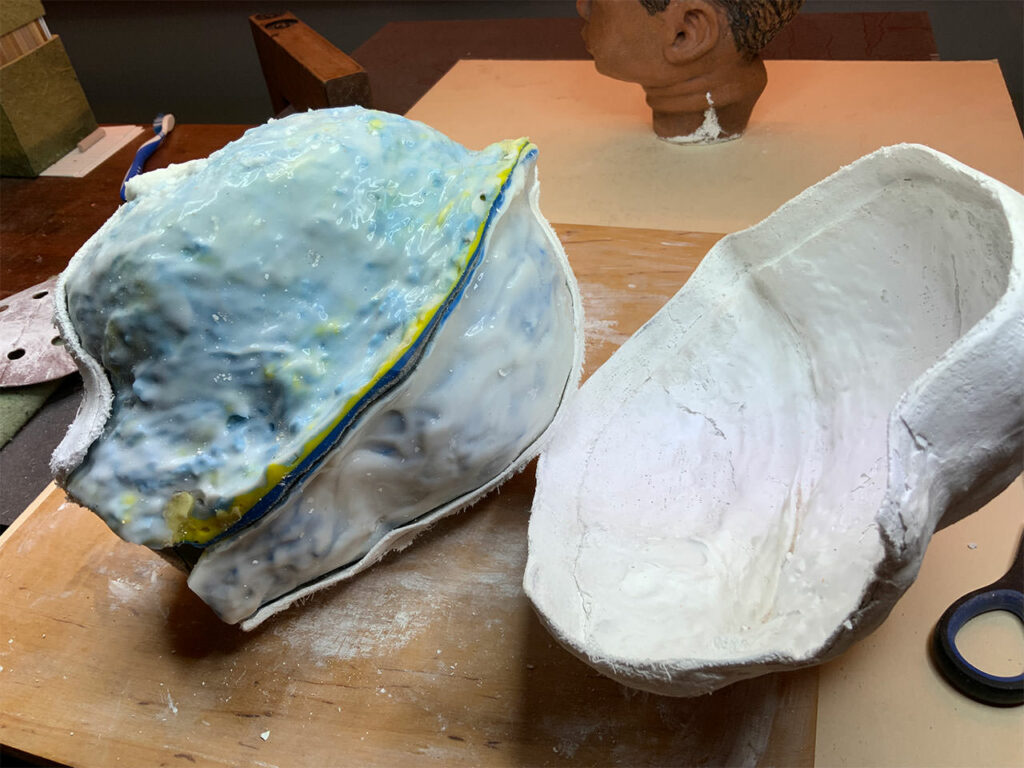
Die Gründe lagen auf der Hand, nämlich einerseits die Zweiteiligkeit der Silikonabformung und andererseits die ungenügende Haltefunktion der Gipshülle, obwohl diese stramm um die Silikonform angepaßt worden war. Die Gipsaustritte führten nicht nur zu einer breiteren Gratbildung auf dem Gussmodell, sondern auch zu Austritten in die Gipshülle – beides ist mit erheblich höherem Reinigungsaufwand verbunden. Natürlich ist IMMER das Gussmodell nachzubearbeiten, also kleine Defekte mit Gips ausfüllen (Achtung: immer dest. Wasser nehmen!) oder die unvermeidlichen Grate abtragen. Aber die Unterschiede im Nachbearbeitungsaufwand zwischen den Gußergebnissen mit den drei unterschiedlichen Gipsmänteln waren deutlich und so blieb ich zunächst bei der möglichst schweren Variante, nämlich der Blockform mit dem schweren Gipsblockdeckel: hier trat am wenigsten Fließgips aus und umso weniger Nachbearbeitung fiel an.
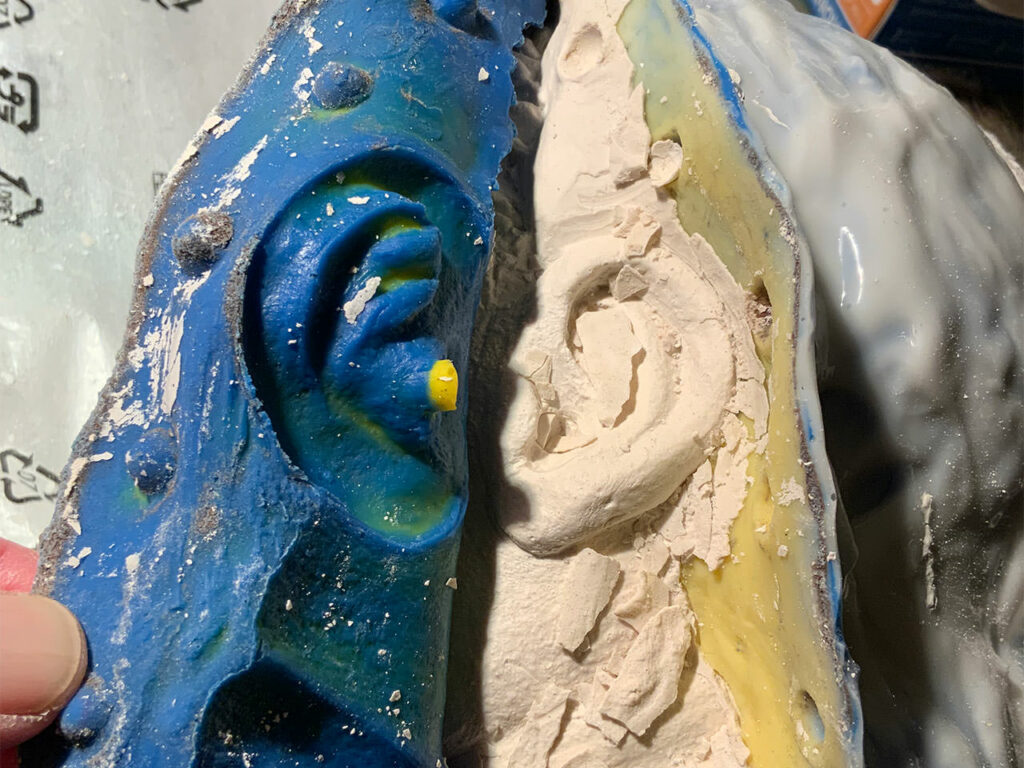
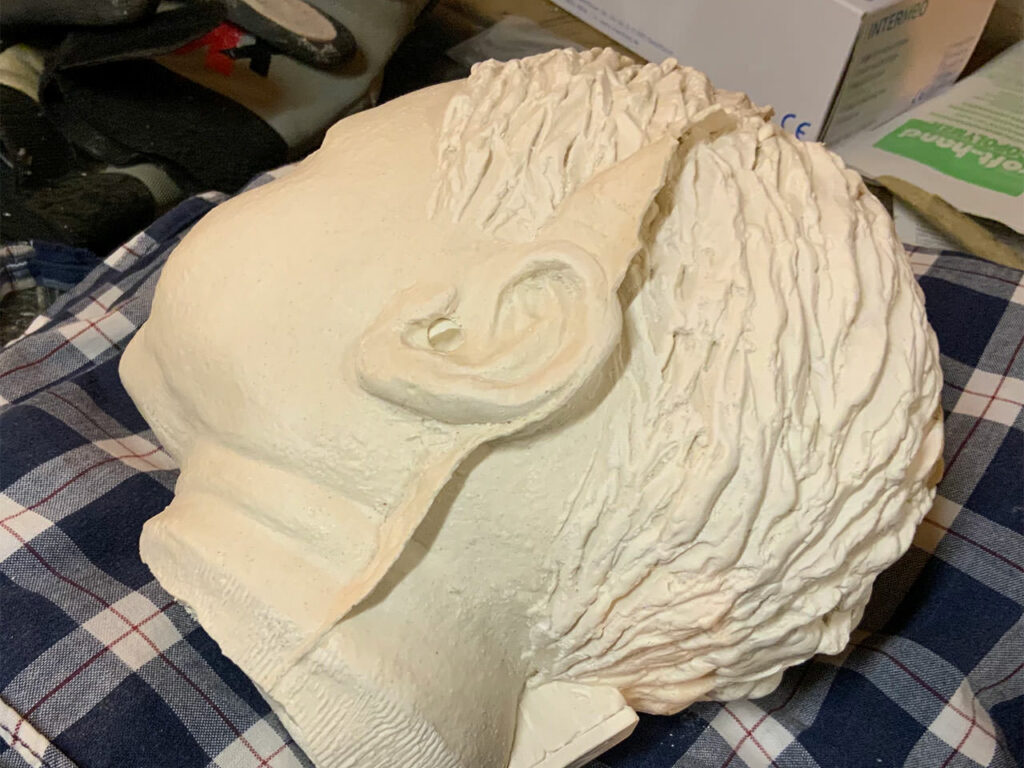
EINFACHE FORMEN SIND UNKOMPLIZIERT
Die zuvor dargestellte Silikonabformung und die äußere stützende Gipsschalung läßt sich definitiv vereinfachen. Es braucht keine überstehenden „Silikonlippen“, wie es zuvor gezeigt wurde. Eine einfache Kopfform wird nach Verschluß der Tonporen des Tonoriginals (mittels PVA) und Trennspray (PTFE trocken) mit mehreren Lagen Silikon überzogen – die dünnflüssigste zuerst, dann immer zähflüssigere.
Danach erfolgt die Anfertigung der Gipsschalen: auf das mit Silikon umhüllte Tonmodell wird eine Frischtonbegrenzung gesetzt und so eine Gipsschalung hergestellt, meist in zwei oder drei Unterteilungen. Dabei muß darauf geachtet werden, daß eine spätere Ablösung gut möglich ist, also Ausbuchtungen umgangen werden – siehe dazu den folgenden Abschnitt KOMPLIZIERTE FORMEN. Die Gipsschalen stabilisieren die flexible Silikonform beim Einguß des Fließgipses – sie sind unbedingt nötig!
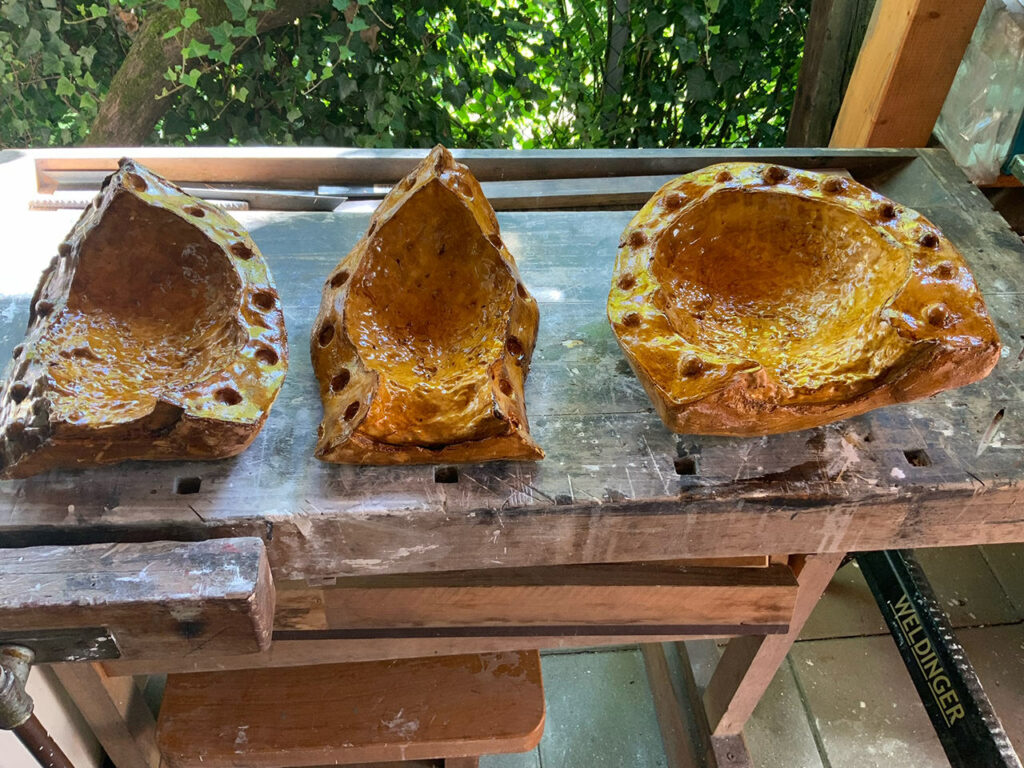
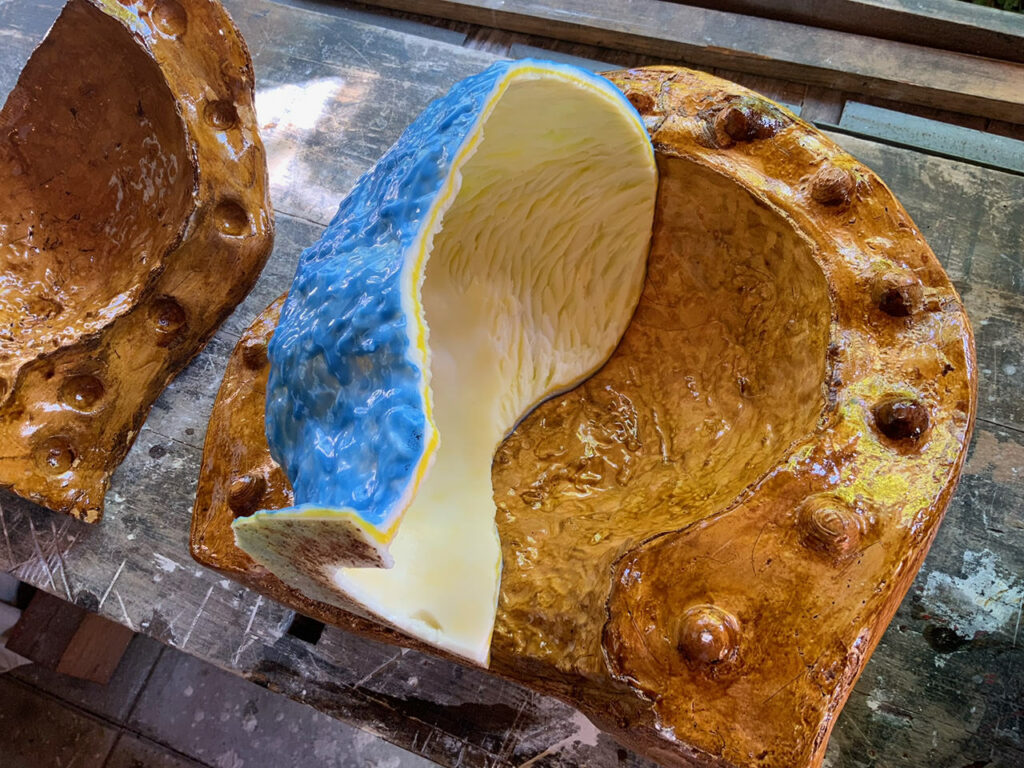
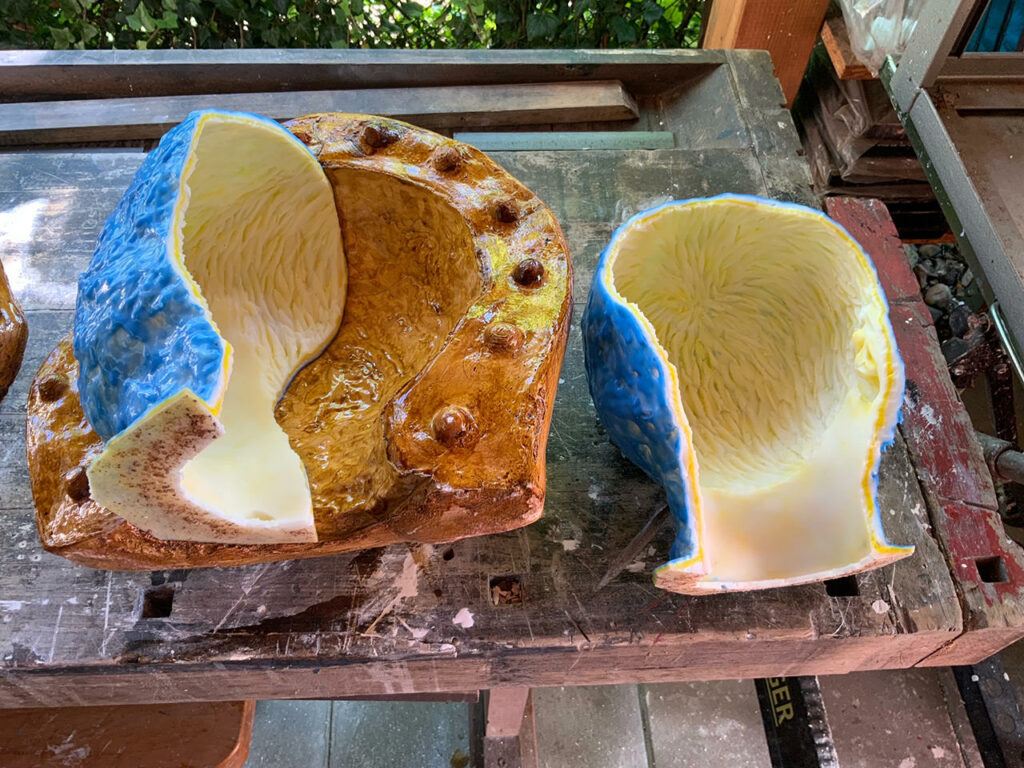
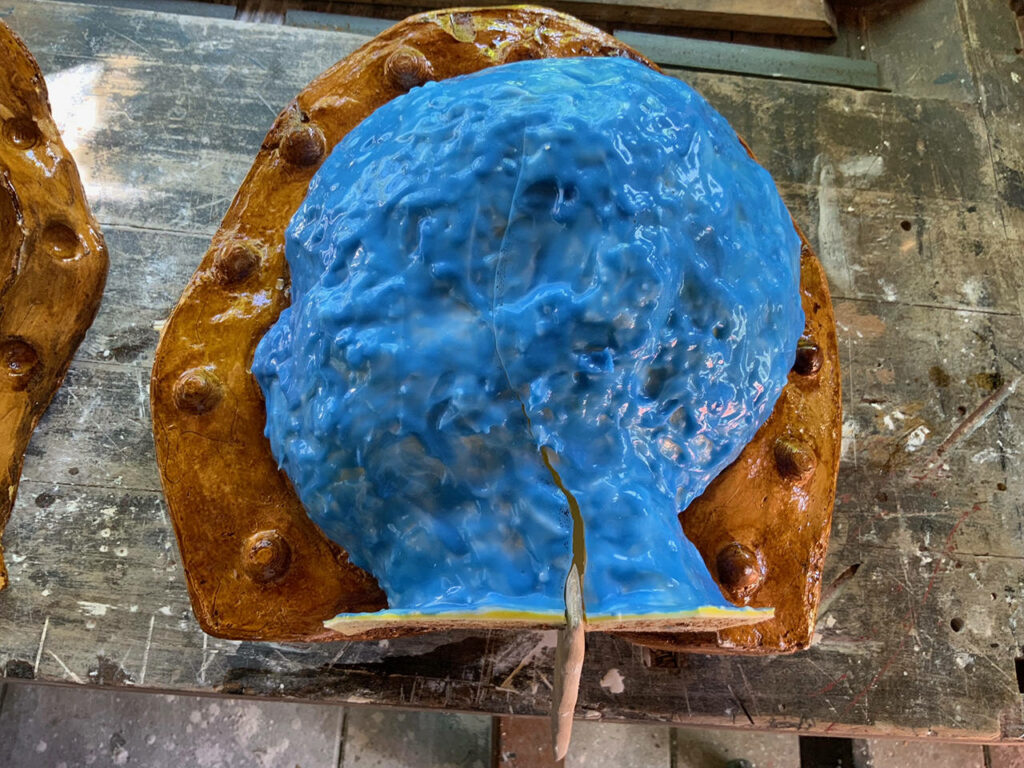
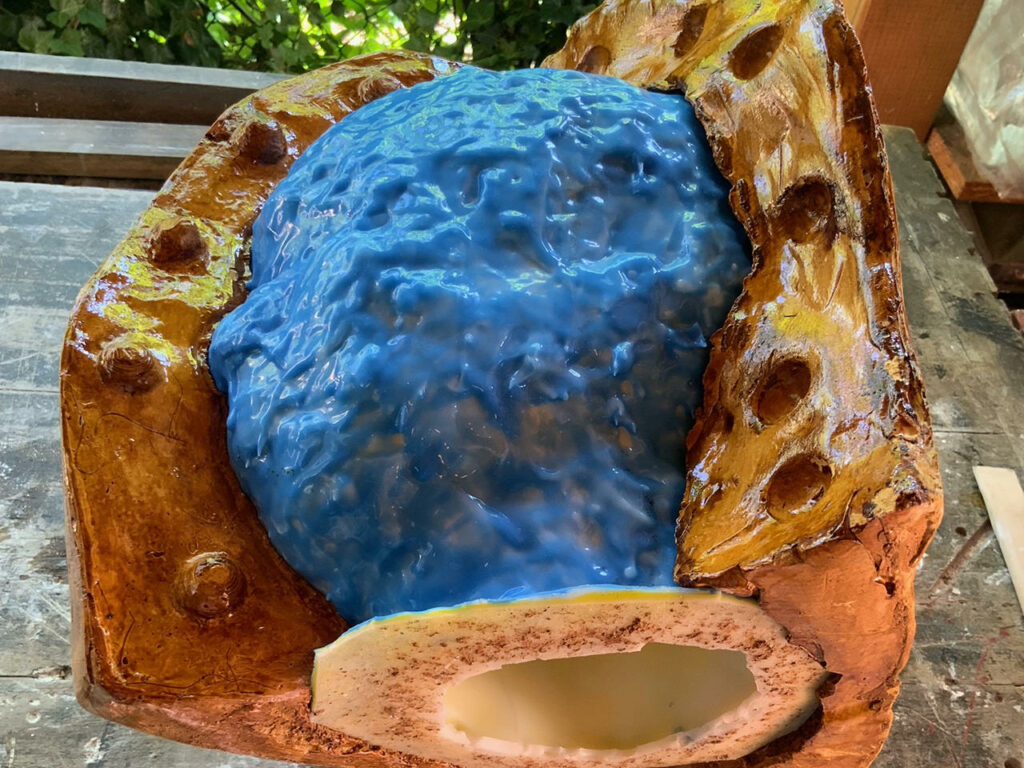
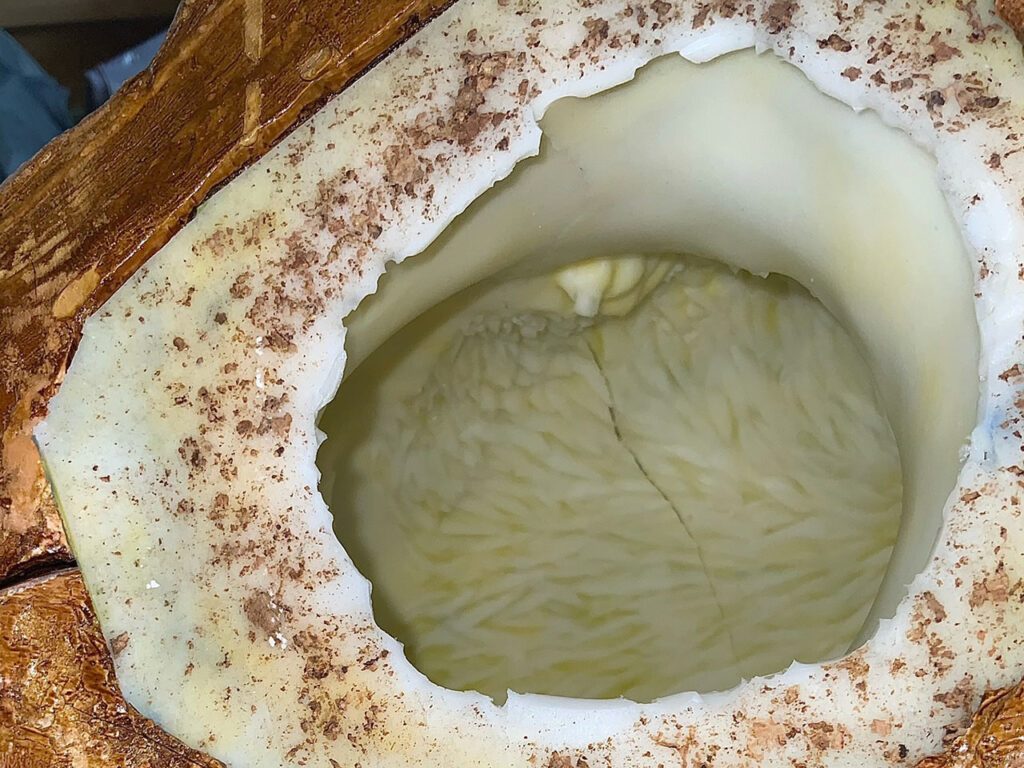
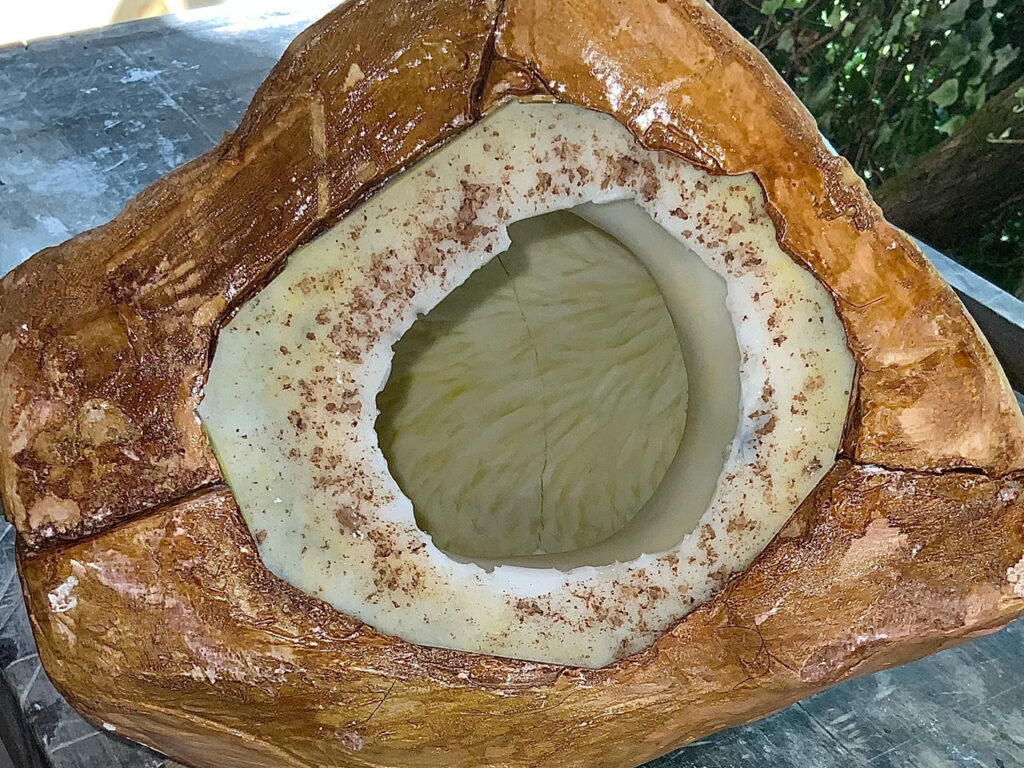
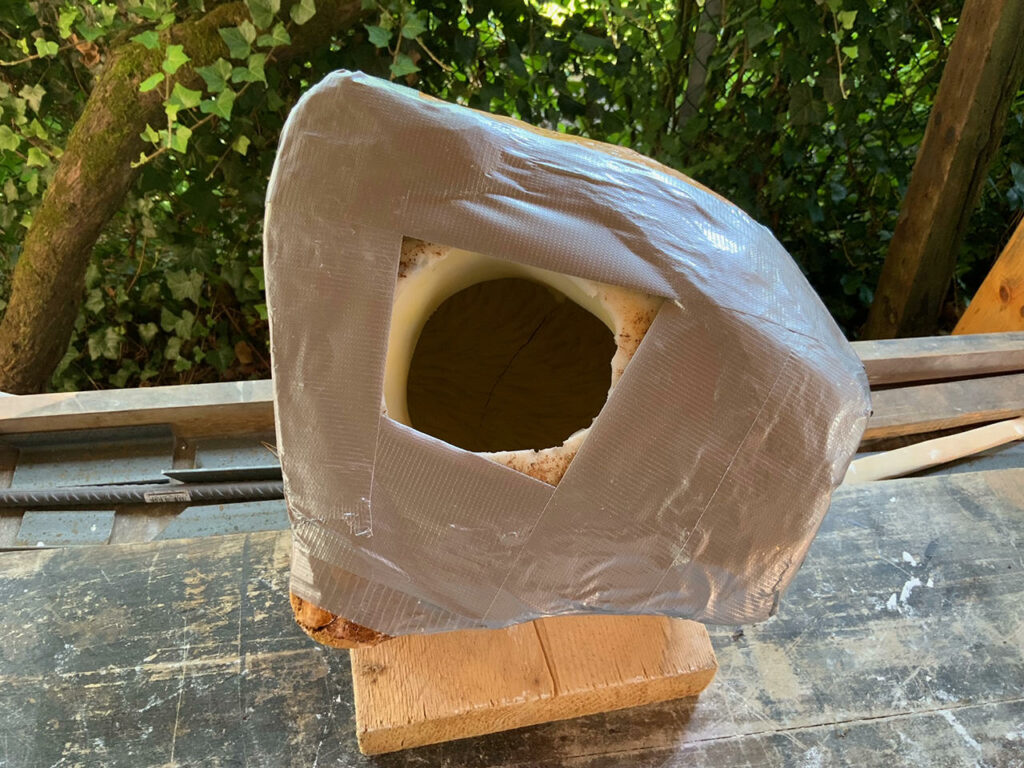
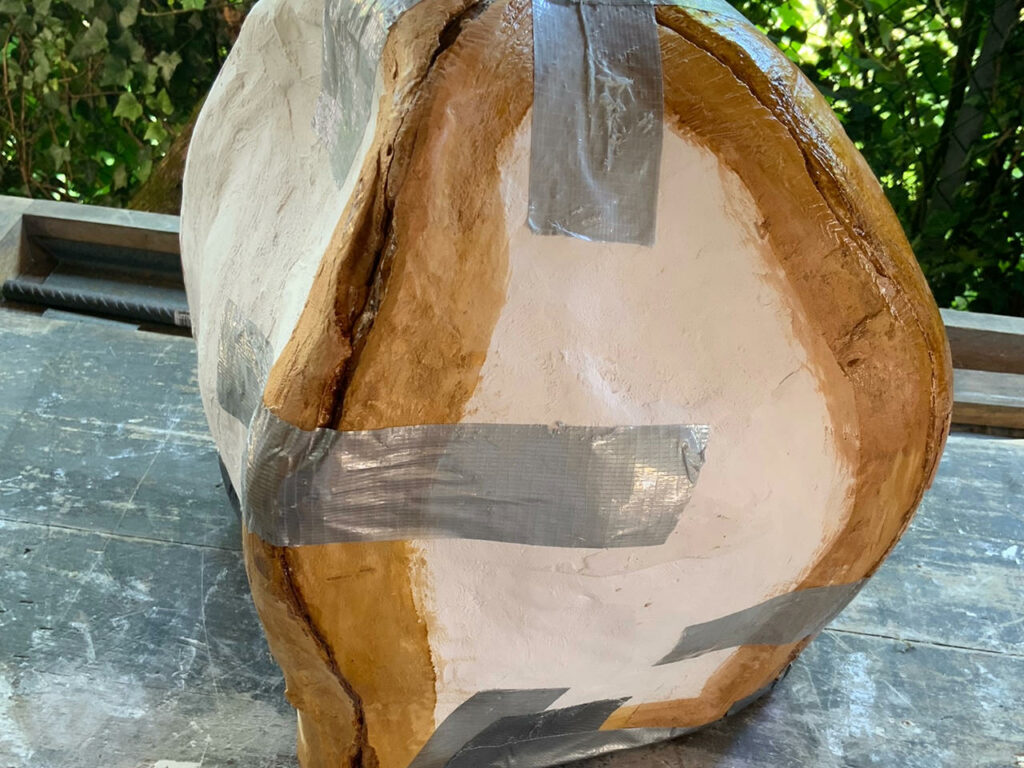
KOMPLIZIERTE FORMEN
Für die mühevoll nachbearbeitete Büste Gretas wählte ich folgenden Formenbau: eine zweiteilige Silikonform kombiniert mit einer dreigeteilten Gipskappe. Die Silikonform an sich war mit erheblichen Problemen behaftet, da die Zöpfe Gretas zu sogenannten „Hinterschneidungen“ führten und eine Art „Druckknopftechnik“ sollte die nur zweiteilige Form ermöglichen.
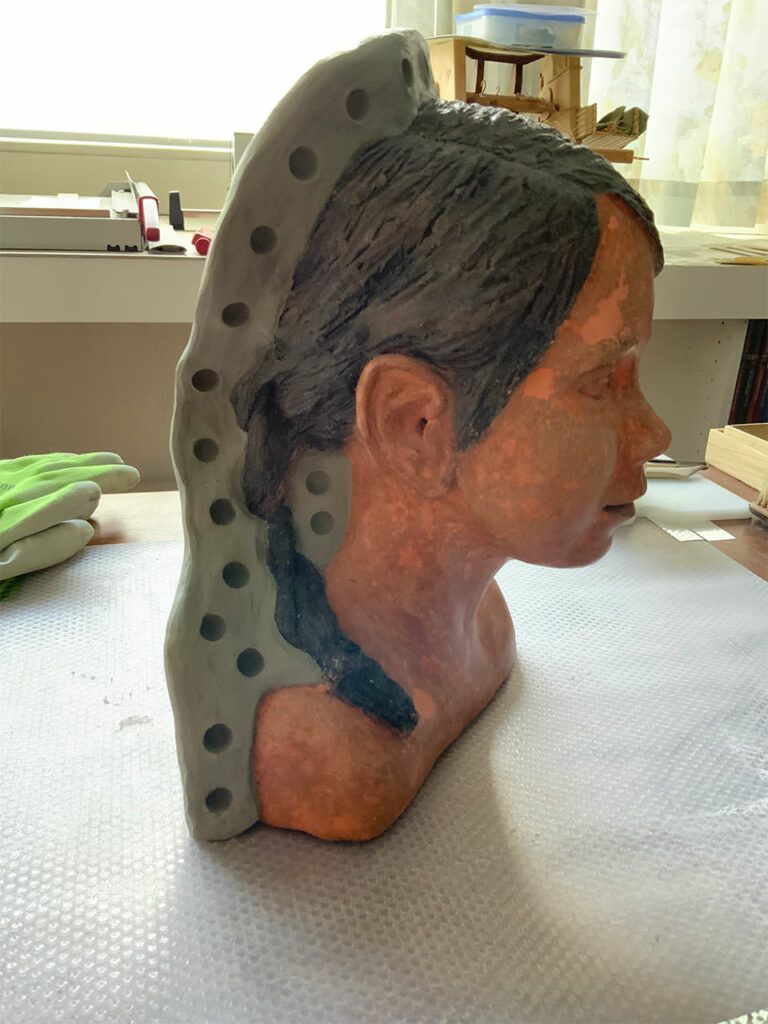
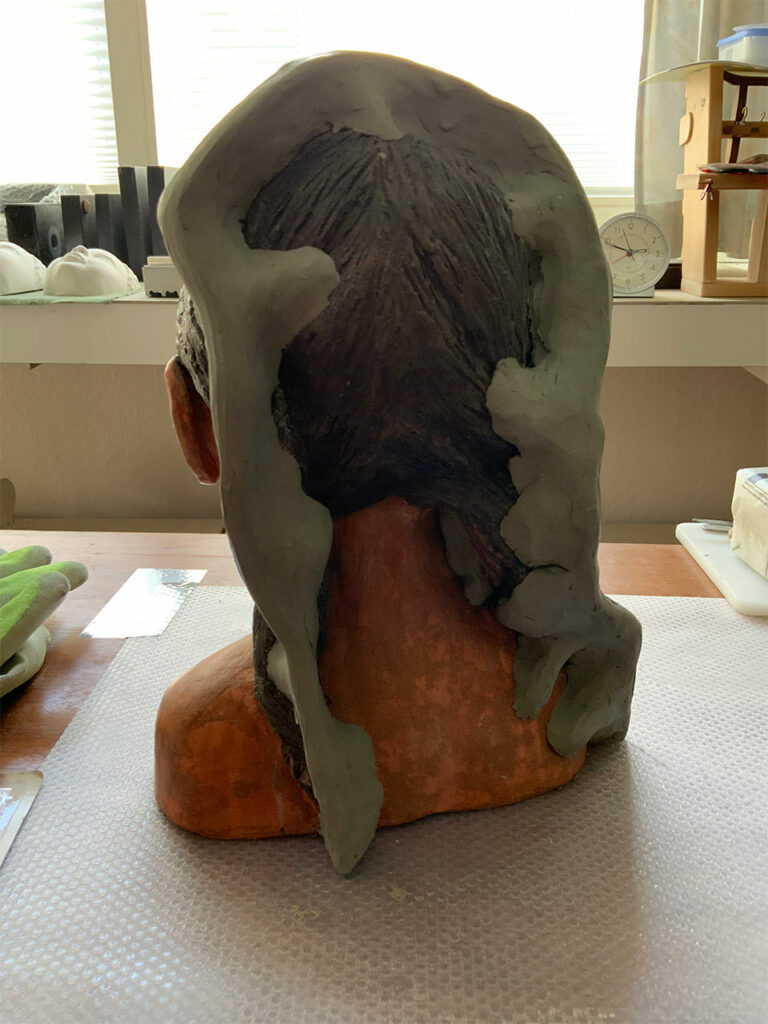
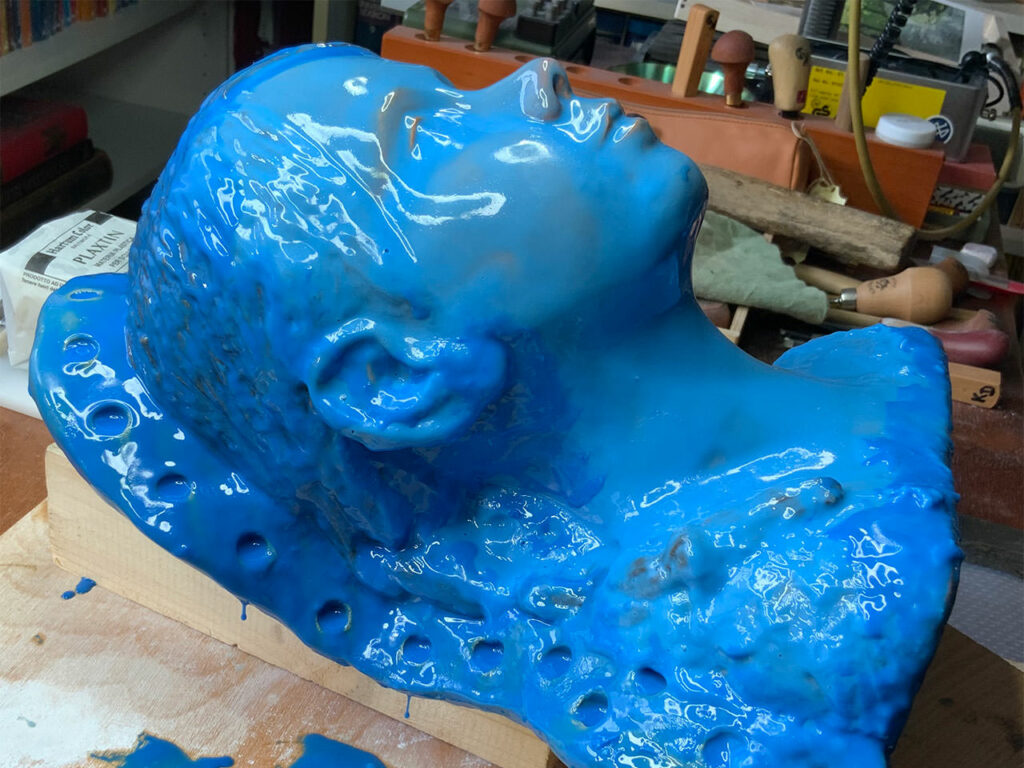
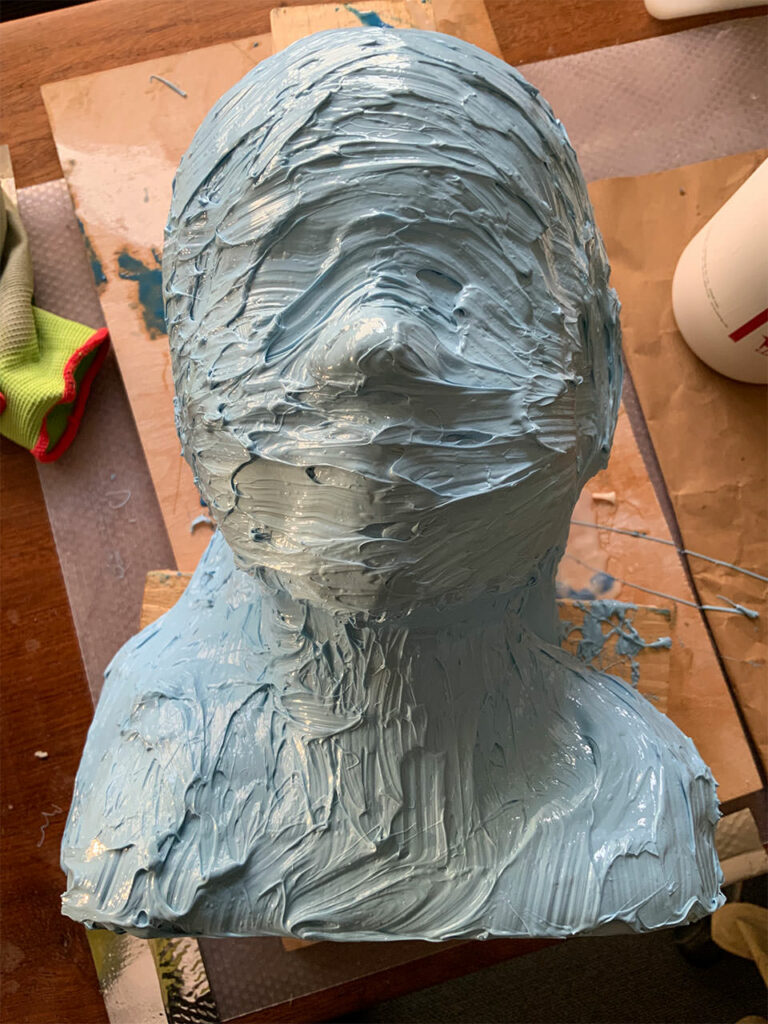
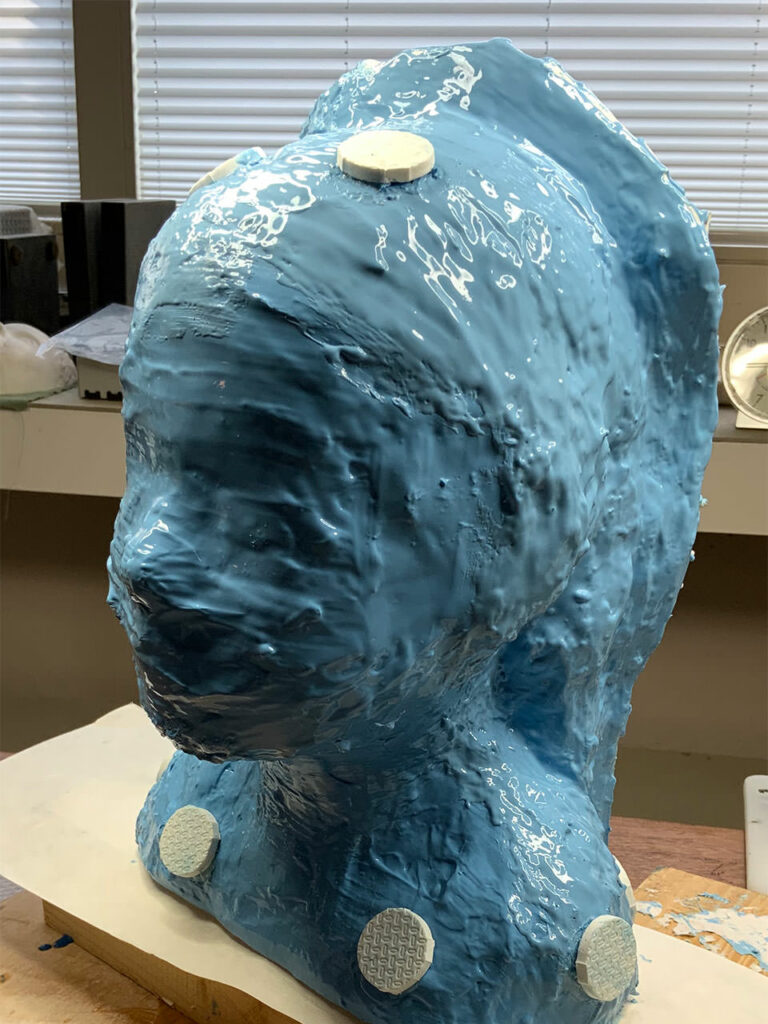

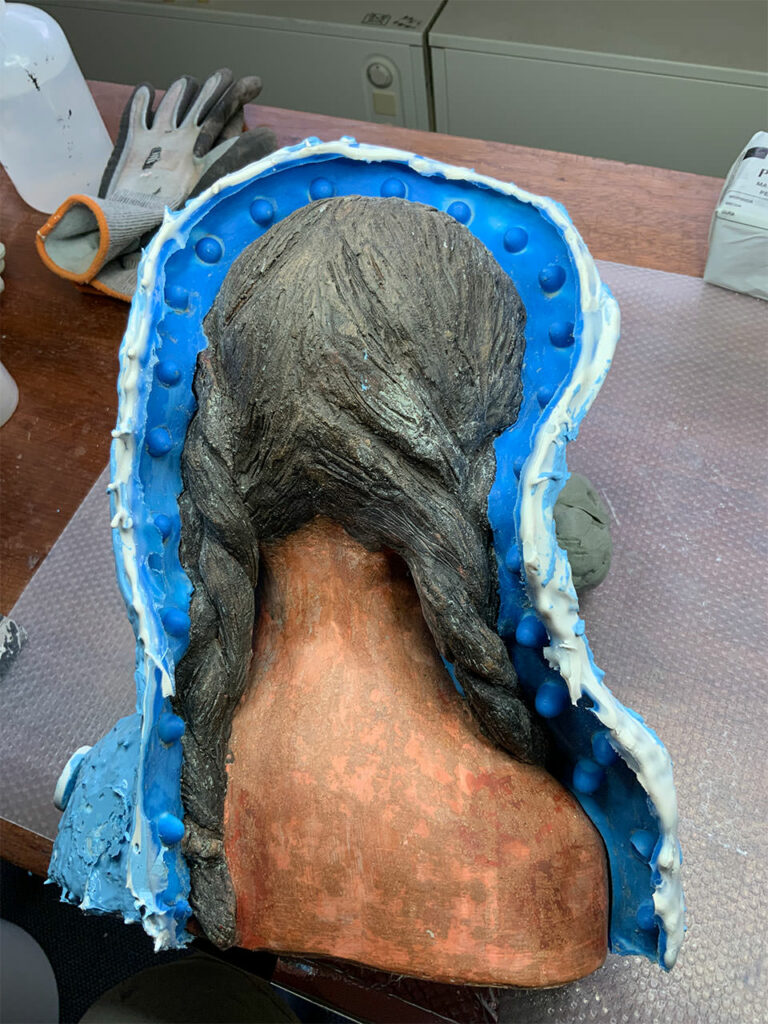
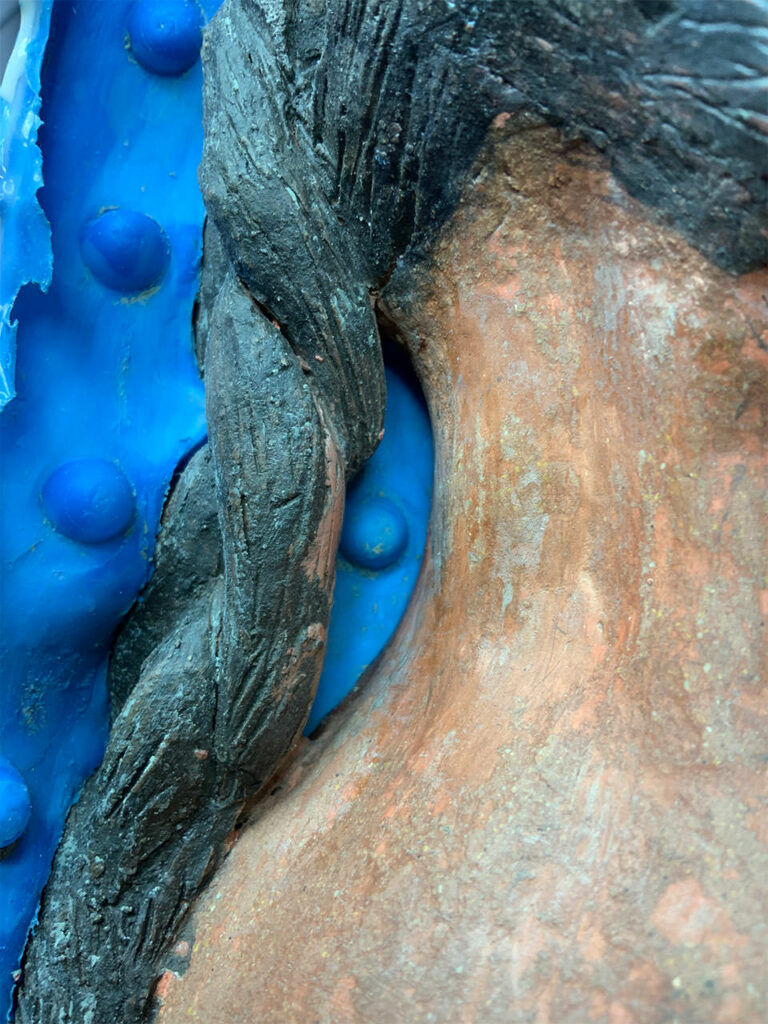
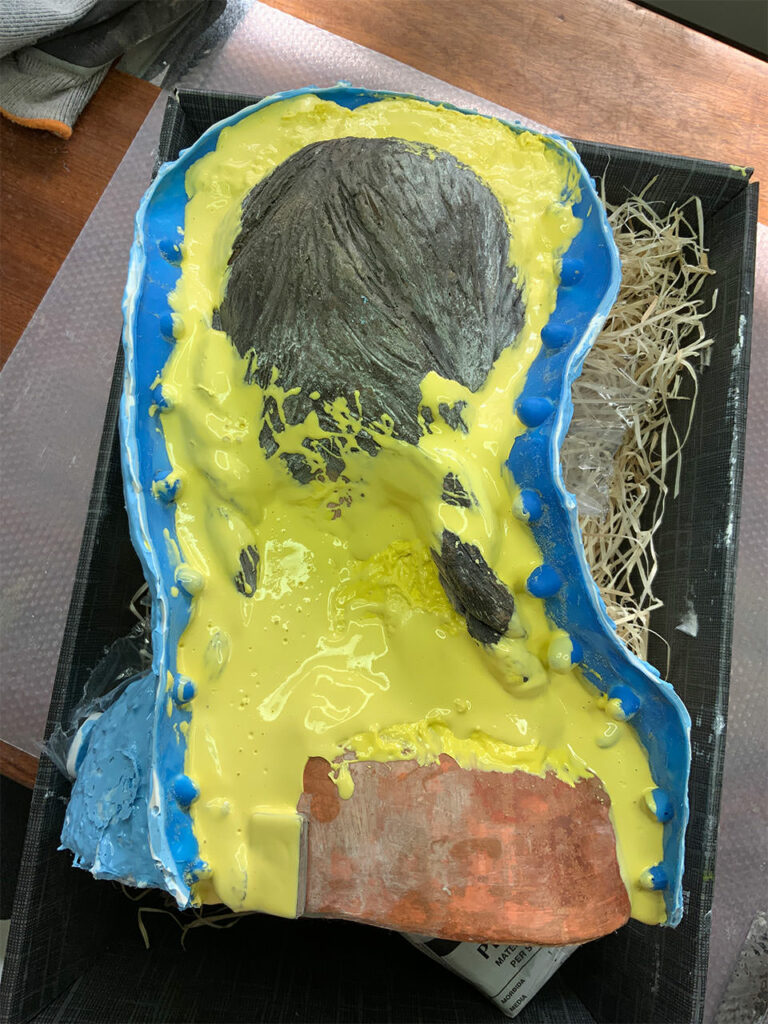
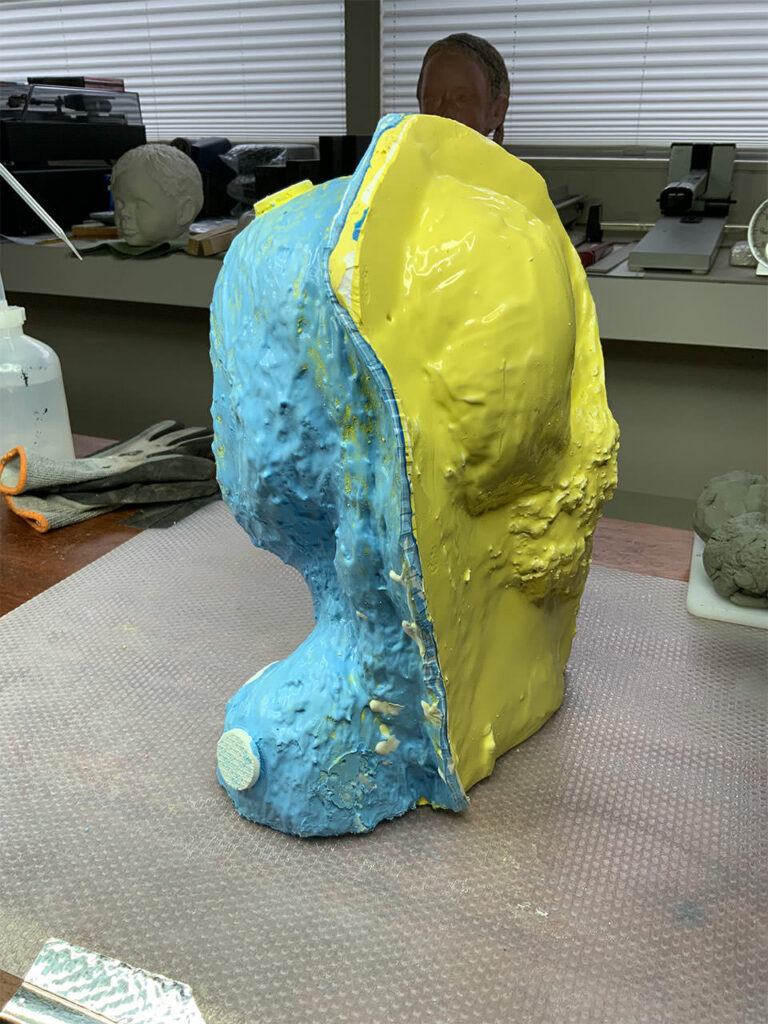
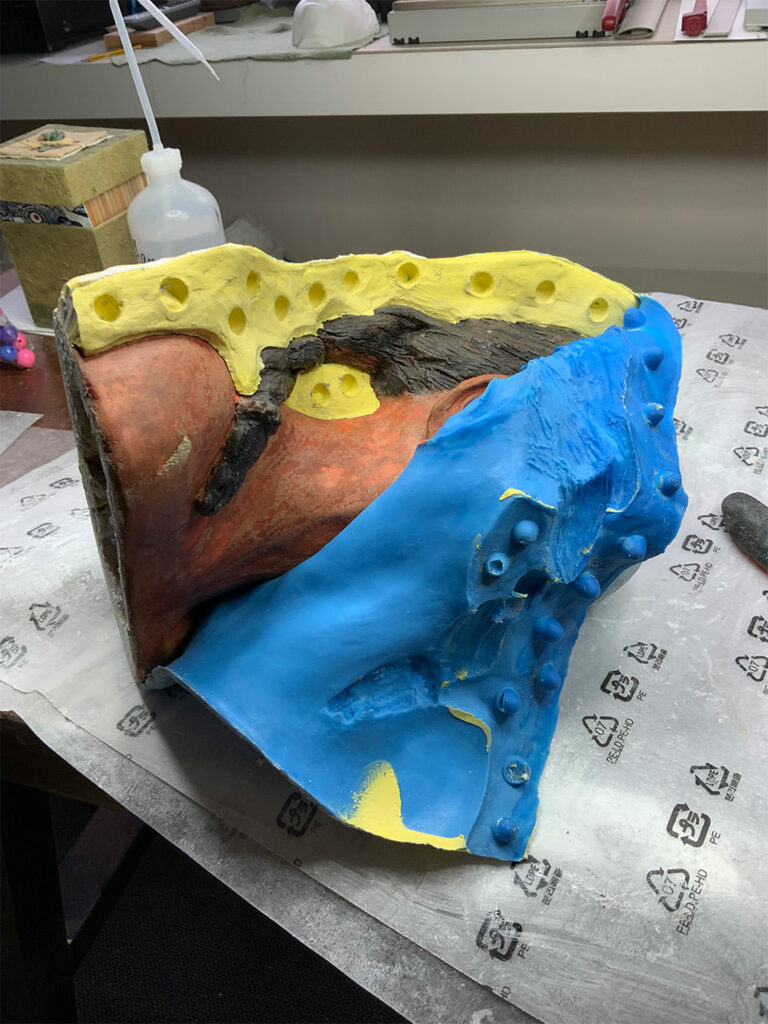
Die noppenartigen Erhebungen (blau) sind meine „Passmarken“ und erlauben das exakte Einpassen des Gegenstückes (gelb).
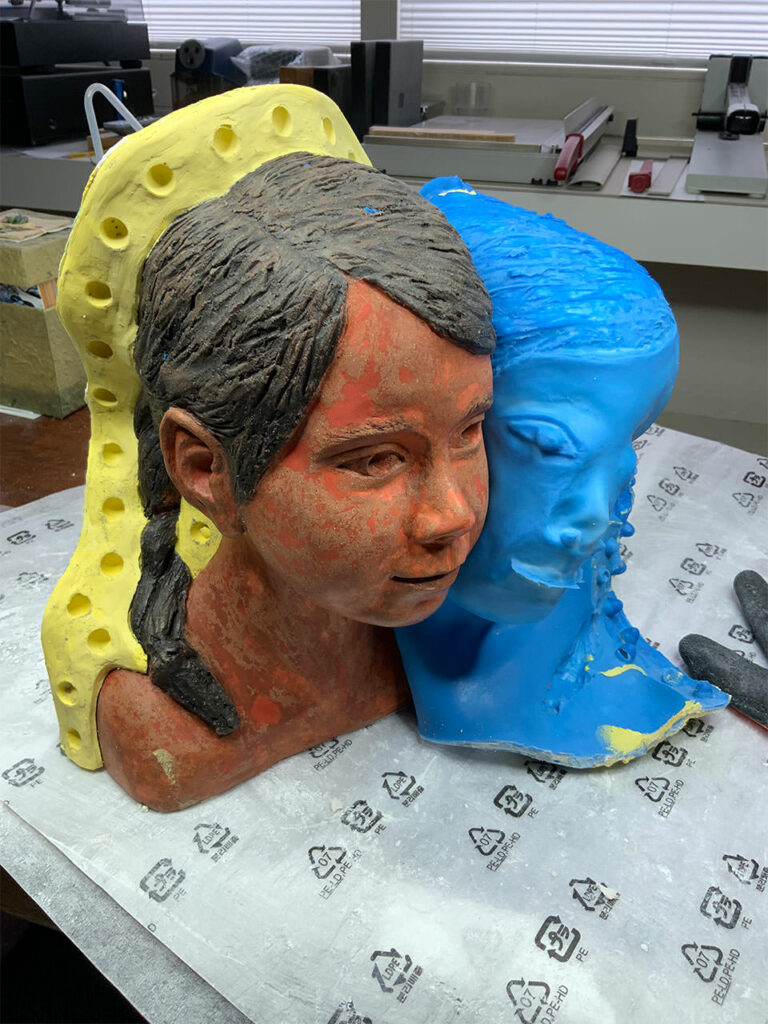
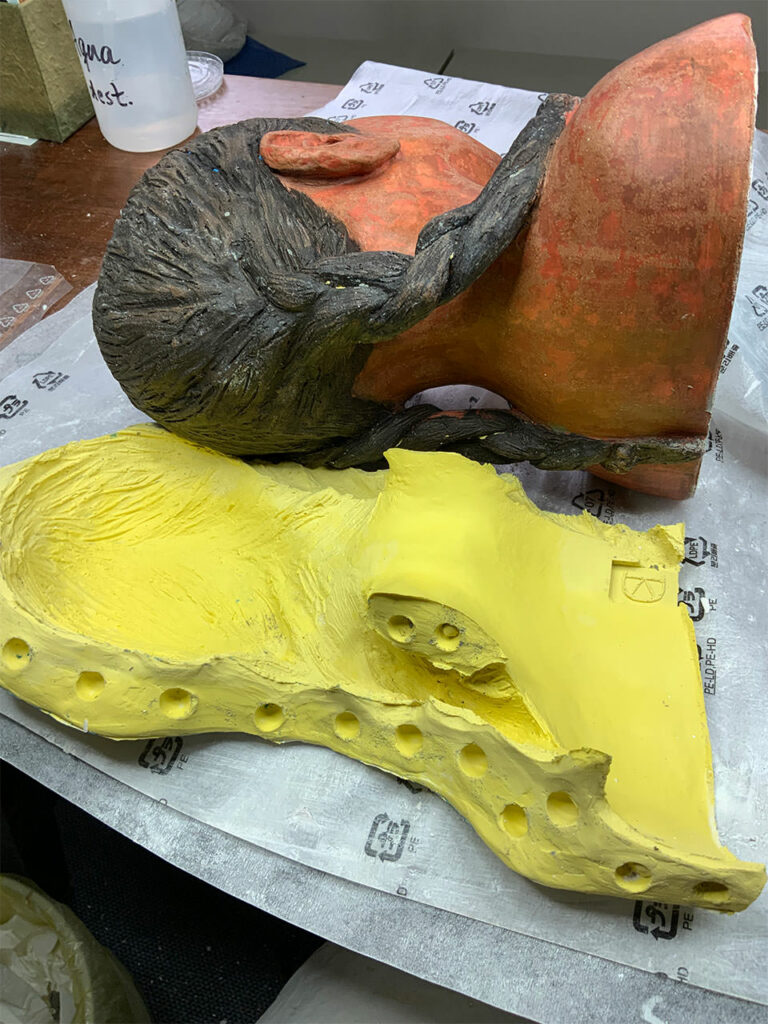
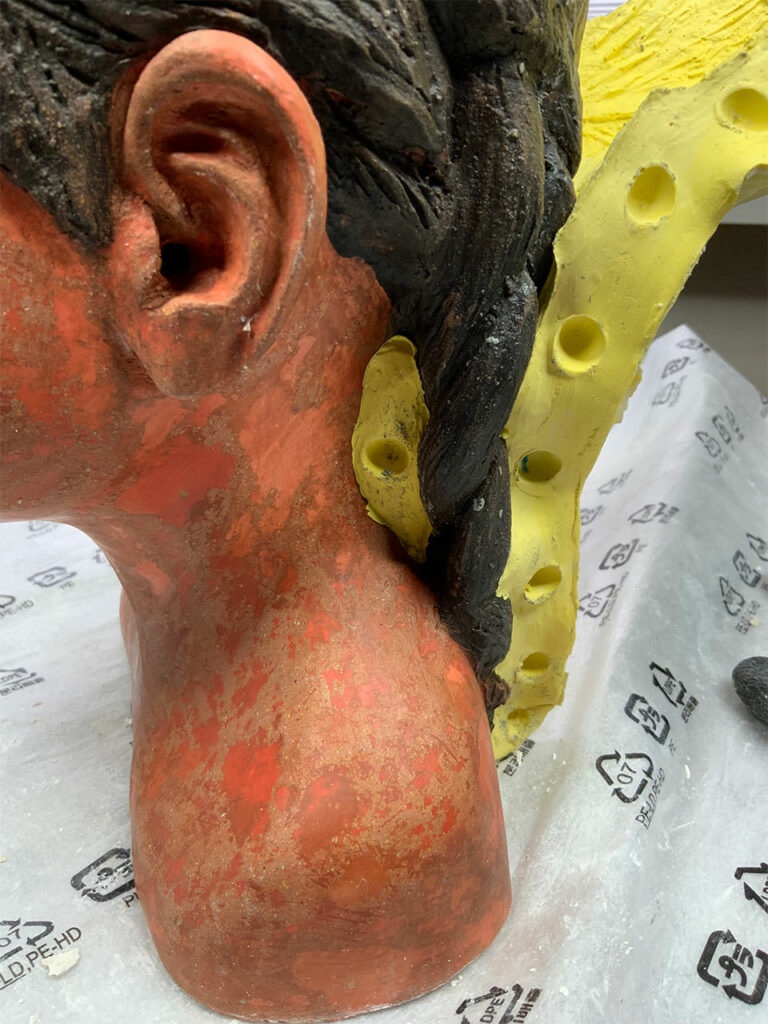
Als nächste Schwierigkeit zeigte sich die äußere Gipshülle, die wegen der Oberflächen dreigeteilt sein mußte – sonst hätten sich nicht die Teile von der Silikonform ablösen lassen. Auf die rutschige Silikonhülle legte ich dann Gipsbinden auf, die im Gegensatz zu dem als Trennwand gedachten Plastilin sogar gut anhafteten und einen Randwall ermöglichen. Das Plastilin rutschte nämlich haltlos ab.
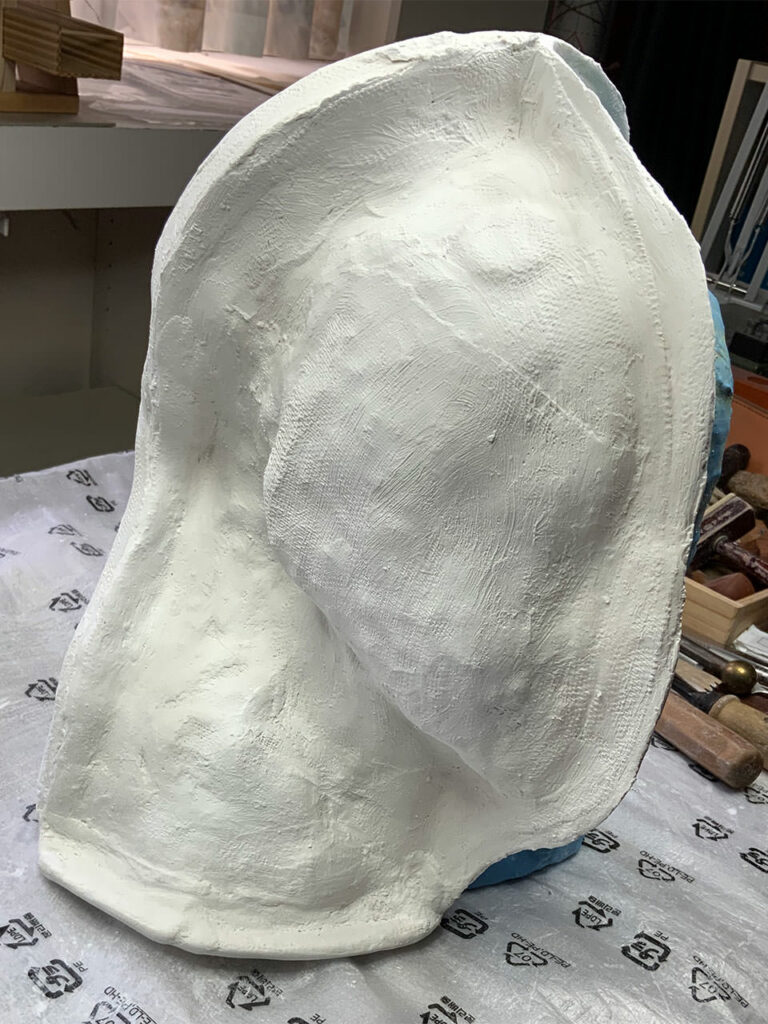
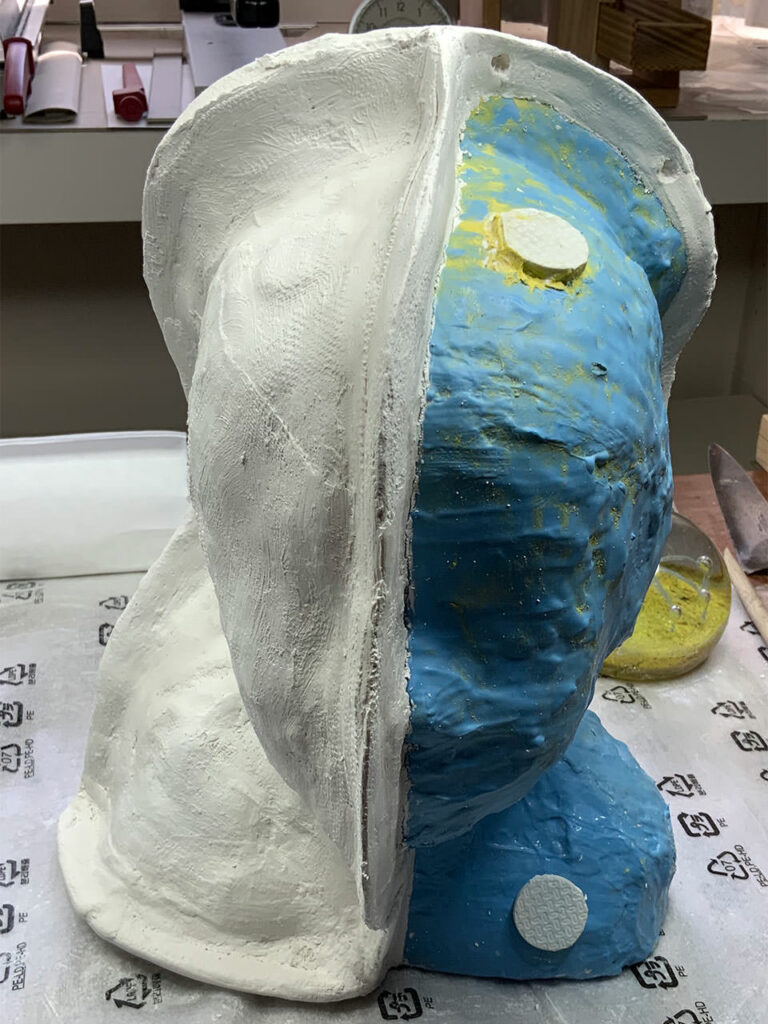
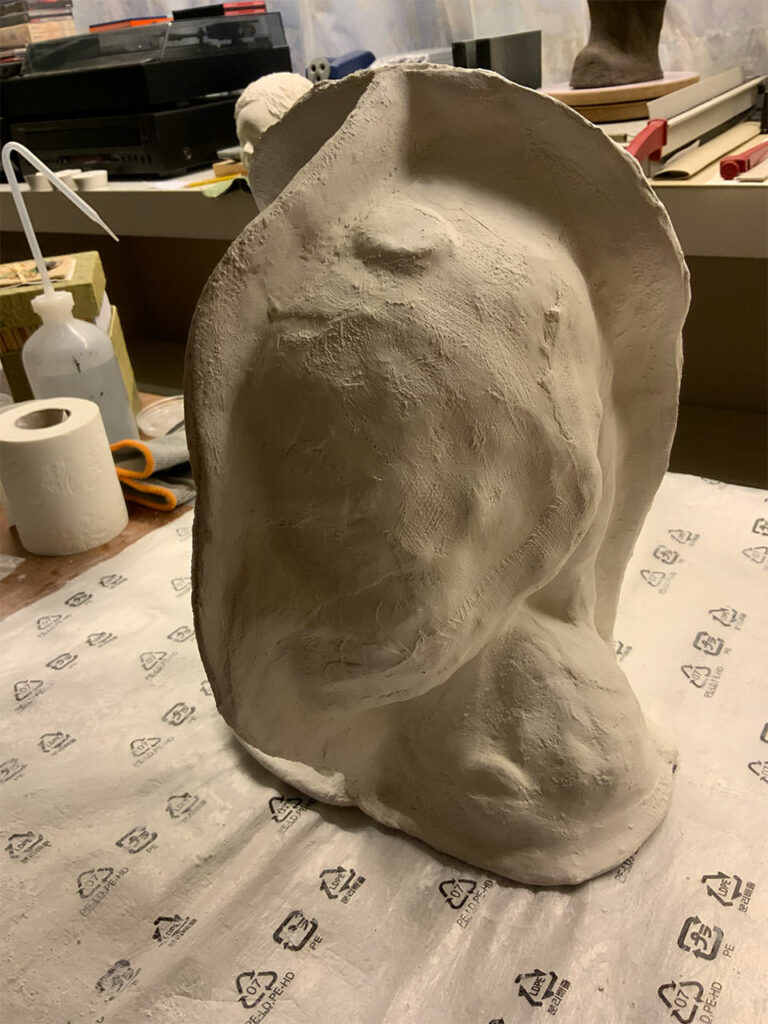
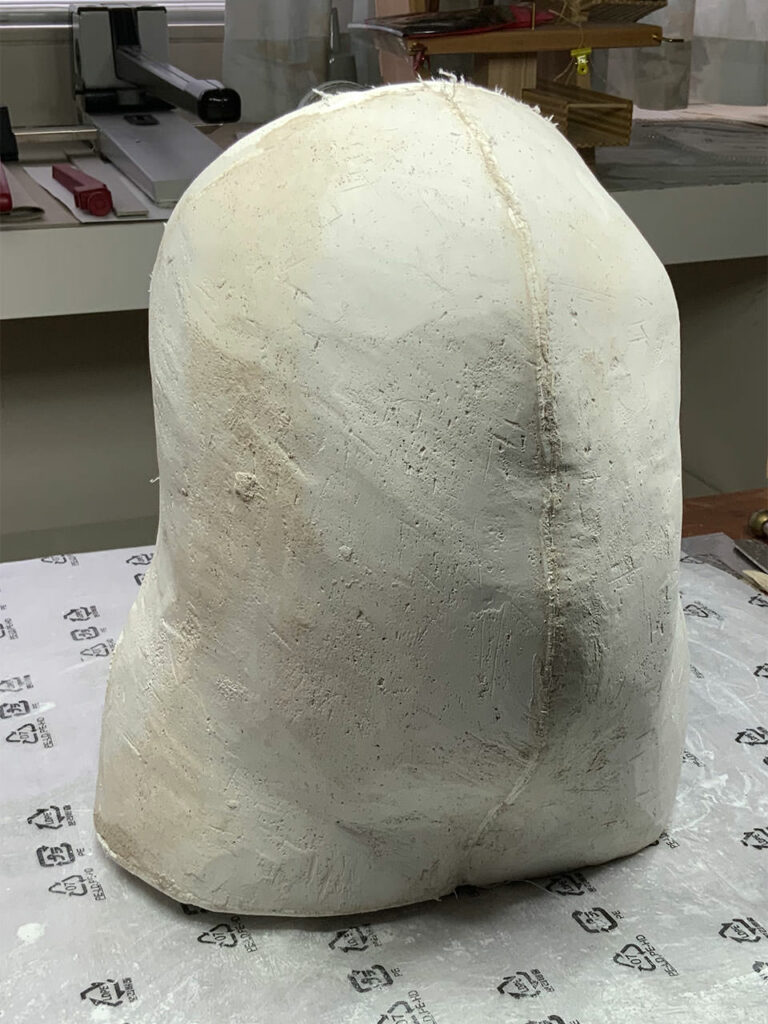
Die separiert geformten Gipskappen, begrenzt durch die wallartig aufgebauten Gipsbinden, wurden als drei große Mulden mit einfachem, schnellhärtendem und preiswertem Elektrikergips aufgebaut und so entstand der zusammenhängende Block, der sich auf einem Heizkörper in nur wenigen Tagen trocknen ließ.
DER GIPSGUSS
Dieser steht erst an, nachdem sowohl die innere Silikonform als auch die äußeren Ummantelung mit einfachem Gips gefertigt sind. Vor dem Einbetten der Silikonform in die Gipshülle erwies sich als hilfreich, sie mit Vaseline Spray zu besprühen: so löst sie sich später recht leicht aus der paßgenauen äußeren Gipsummantelung.
Anfangs verwandte ich noch PTFE-Trennspray, um die leichte Auslösung des Gusses aus der Silikonform zu bewirken, jedoch bekam ich später erst den Profi-Tipp, die Silikonform INNEN gründlich mit Seifenlauge (Spüli) von allen Fettresten zu befreien, damit sich die Oberflächenspannung reduziert und der Gipsleicht überall hin fließen kann – und dies reduziert enorm die Blasenbildung.
Fast peinlich zu erwähnen, aber wahr, gestaltete sich mein erstes Vorgehen: so goß ich doch insgesamt 8 L Fließgips (CALCAST 200 / Fa. bildhau, Köln) in den (vermeintlich) dichten Formkasten.
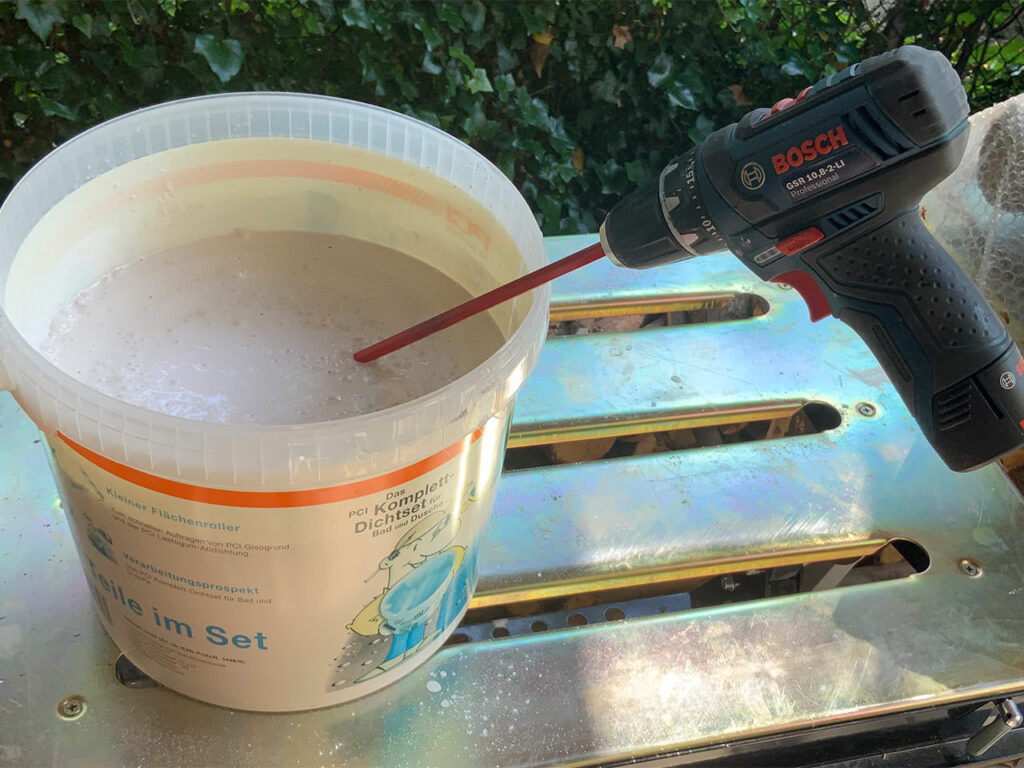
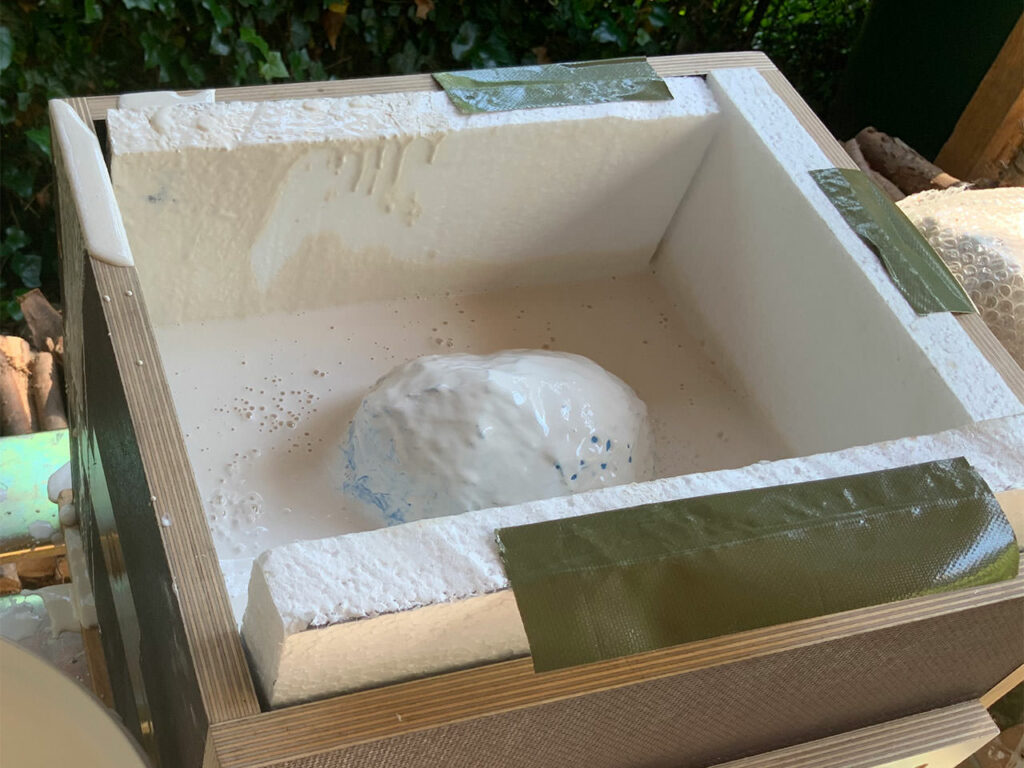

Resultat: eine Riesensauerei! Konsequenz: immer schon vorher die „Ritzen“ des Formkastens mit ein wenig Gipsmasse abdichten und die „aufschwimmenden“ Styropor-Platzhalter gleich fest fixieren, dann erst ist es eine Freude.
GIPS IST NICHT GLEICH GIPS — DIE GIPS-DIVEN
Und dies gilt sowohl für seine Zusammensetzung als auch für seine „Aufbereitung“. Erfreulich aber: Naturgipse sind ungiftig, nicht ätzend und ökologisch unbedenklich.
Hat aber der Gips schon trotz trockener Lagerung kleine Verklumpungen, so muß man diese durch ein Feinmaschensieb auflösen. Ebenfalls ein typischer Anfängerfehler war das elektrisch-motorische Anrühren: es bleiben viel zu viele kleine Blasen – und das, obwohl ich mir extra dazu eine Rüttelplatte gebastelt hatte, um jene Störenfriede zu vertreiben .
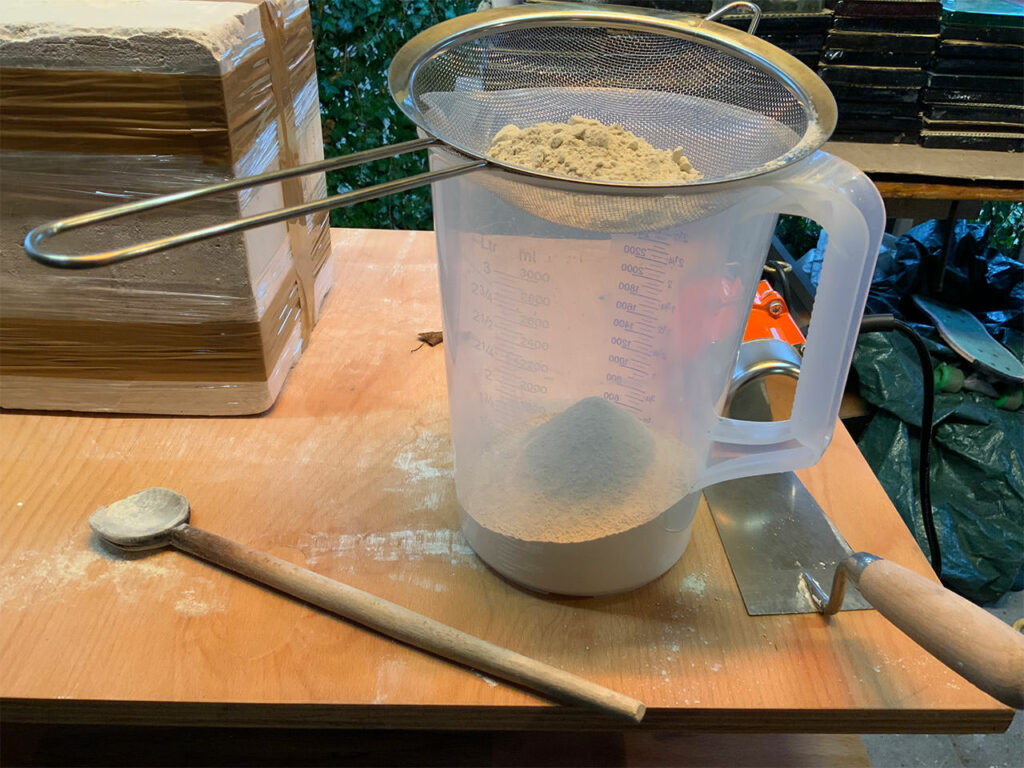
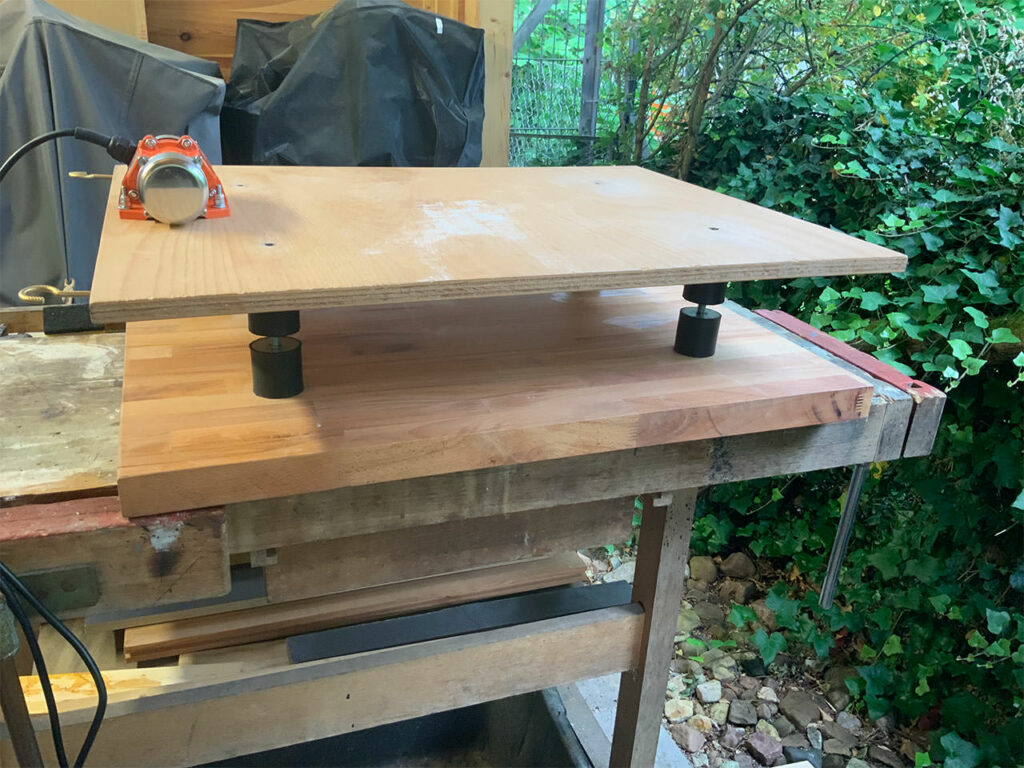
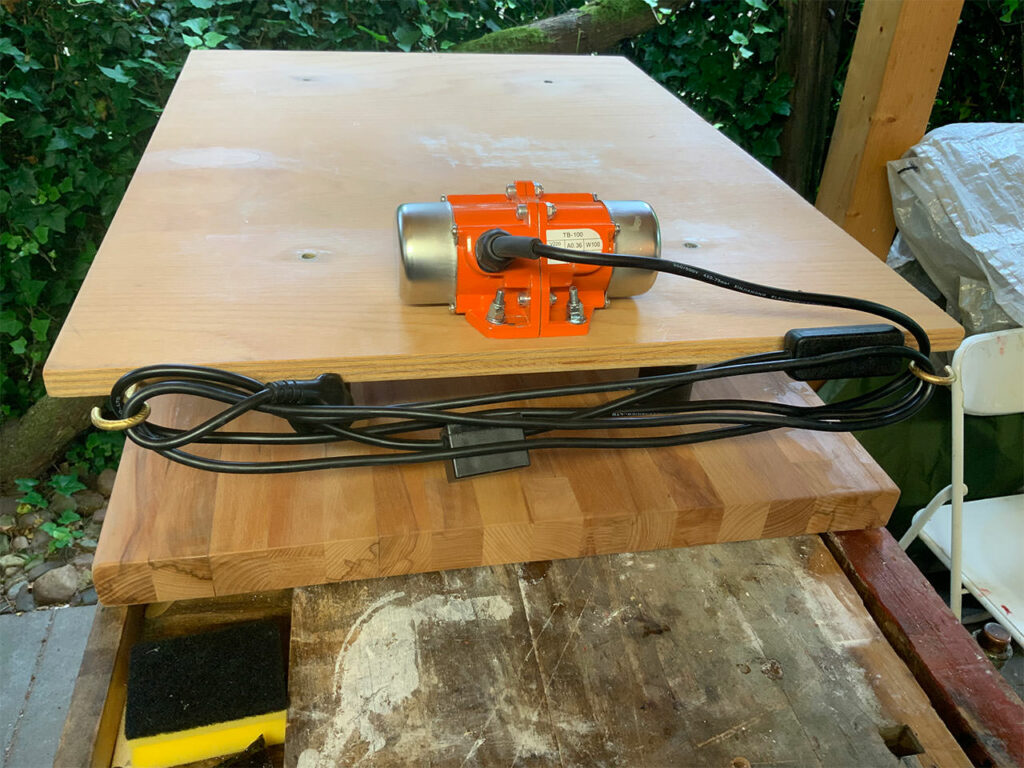
Den Bau dieser Rütteleinrichtung hätte ich mir sparen können, denn die erhoffte Reduktion der Blasenbildung war nicht überzeugend. Mittlerweile rühre ich den Gips auch garnicht mehr in das Wasser ein, sondern streue ihn portionsweise und langsam in die bereitgestellte Wassermenge (muß kein Aqua dest. sein), bis beim Einstreuen sich feste „Inseln“ bilden, dann lasse ich für einige Minuten alles in Ruhe „einsumpfen“– eine Empfehlung der Profis an der Staatlichen Gipsmanufaktur zu Berlin. Erst kurz vor dem eigentlichen Eingießen darf man nämlich umrühren, denn dann läuft die Uhr bis zum Zähwerden – und kann so einen ausfüllenden Guß vereiteln.
Tipp 1: Keine maschinelle Rührung, da nur so weniger Blasen entstehen und man die Klümpchenbildung auch recht gut wegdrücken kann.
Tipp 2: Wer besonders genau und vorsichtig vorgehen will, der folge den Empfehlungen der Dentalgipsprofis (Fa. Hinrichs, Goslar) und wählt nur destilliertes Wasser zum Ansetzen des Gipses (bei Hornbach 5 L = 1,85 €). Der Salzgehalt/Kalkgehalt im Leitungswasser verändert Farbe und Abbindeverhalten enorm – im Nachhinein eine Erklärung für die störenden Farbvariationen noch innerhalb des Gusses der anfangs genommenen CALCAST-Gipse (Fa. bildhau, Köln).
Tipp 3: Wenn man in die Anmischgefäße, z.B. Messbecher, ganz dünne Plastik-Mülltüten (1, 5, 10 L / Fa. Rossmann) einlegt, so hat man kaum noch Arbeit mit festgewordenem Gips.
Tipp 4: Hilfreich kann auch ein Gipsabbindeverzögerer sein (Fa. Hinrichs, Goslar), der in kleiner Menge (2 %) in das Anmischwasser vorab gegeben wird: so muß man sich nicht so arg beeilen. Die gewonnene Zeit bis zum Sämigerwerden kann man gut nutzen, um alle Klümpchen herauszumassieren.
Schließlich aber muß der angerührte Gips wirklich noch recht flüssig sein, damit man die immer auftretenden feinen Bläschen wegklopfen oder wegrütteln kann – eine Rüttelplatte braucht man nicht, aber einfach und zugleich genial ist das Aufsetzen, Drehen und Aufstoßen der kompletten Gipsform auf einem kleinen, aber dicken Kissen. So gelingt es tatsächlich, durch die rüttelnde Bewegung die kleinen Bläschen zu vermeiden, die man sonst später in mühevoller Kleinarbeit durch Gipsauffüllung korrigieren müßte.
Wenn man zu lang mit dem Ausgießen wartet, wenn der Gips also schon anzieht und zäher wird, dann hilft auch das Rütteln nicht mehr: die Blasen können sich nicht sich lösen und in der Silikonform aufsteigen. So wird der Abguss fehlerhaft, da an den Bläschenorten die Form nicht komplett ausgegossen werden kann und man entweder den kompletten Guss verwerfen muß oder mindestens wieder mehr Nachbearbeitungsarbeit hat.
Eigentlich kam ich viel zu spät erst auf die Idee, bei den Superprofis in Berlin direkt nachzufragen (Gipsformerei der staatlichen Museen zu Berlin) und bekam den genialen Tipp, die benötigte Fließgipsmasse in 2–3 oder mehr Fraktionen aufzuteilen. Von dem gemischten Gesamtvolumen – noch nicht umgerührt – entnimmt man eine erste Portion. Dann wird diese KURZ umgerührt und in die Silikonform gegossen. Sie ist noch sehr flüssig, fließt leicht in die Silikonform, wird durch Drehen/Kippen in alle Richtungen in jeden Winkel der Form geführt. Dann läßt man den eingegossenen Gips LEICHT anziehen, danach wird eine zweite Portion entnommen, KURZ umgerührt und eingegossen – wiederum unter Drehen und Kippen der Form. Bei der zweiten Lage kann man dann schon entspannter vorgehen, denn schließlich ist durch den ersten sehr sorgfältigen Ausguss die Form entsprechend abgebildet. Schließlich wird der gesamte Rest des ungemischten Gipses eingegossen, zuvor aber noch umgerührt. Man hat aber die Wahl, ob man komplett die Form ausgießt oder eine Hohlform wählt. Dazu sollte die Gipsschichten aber mindestens 1 cm Wandstärke allseitig haben.
DIE QUAL DER WAHL
In der Staatlichen Gipsmanufaktur wird standardmäßig SUPRADURO eingesetzt, welchen ich bei der Goslarer Firma Hinrichs (mischt eigentlich in großem Stil Gipse für den zahnärztlichen Bereich) beziehen konnte. Dies ist kein Baumarktgips! Alternativ bietet diese Firma auch den ALMOD an, welcher gleichermaßen für Abgüsse/Skulpturen geeignet ist, aber von der Konsistenz her etwas weicher ist.
Erfreulicherweise auch recht preiswert (ca. 15–20 €/25kg): der SUPRADURO wird härter, dichter als der ALMOD, aber beide sind einfach schön weiß, edel und gut bearbeitbar – der ALMOD noch leichter als der SUPRADURO.
Die Fa. Bildhau in Köln bietet CALCAST 200/300 an – ersterer ist fast weiß, letzterer cremefarben.
ABLAUF DER GUSSVORBEREITUNG … UND DER GIPSGUSS
Somit ist die komplette Gießform hergestellt, bestehend aus der inneren Silikonabfomung in zwei Teilen und der äußeren Gipshülle in Form von drei Gipskappen.
Zur Festigung der Gipsoberfäche INNENSEITIG ist ein Überzug mit Schellack sinnvoll, da die Oberfläche gehärtet wird und auch weil sich dann aus der Silikonform austretender Fließgips später leichter entfernen läßt. Ferner ist darüber ein dünner Überzug mit Vaseline oder Trennspray (PTFE) hilfreich, damit sich die Gipskappen nach erfolgtem Guss leicht von der inneren Silikonform lösen lassen.
Für den eigentlichen Guss mit Fließgips müssen diese Gipskappen in immer der gleichen Reihenfolge auf- und abgebaut werden (I / II / III).
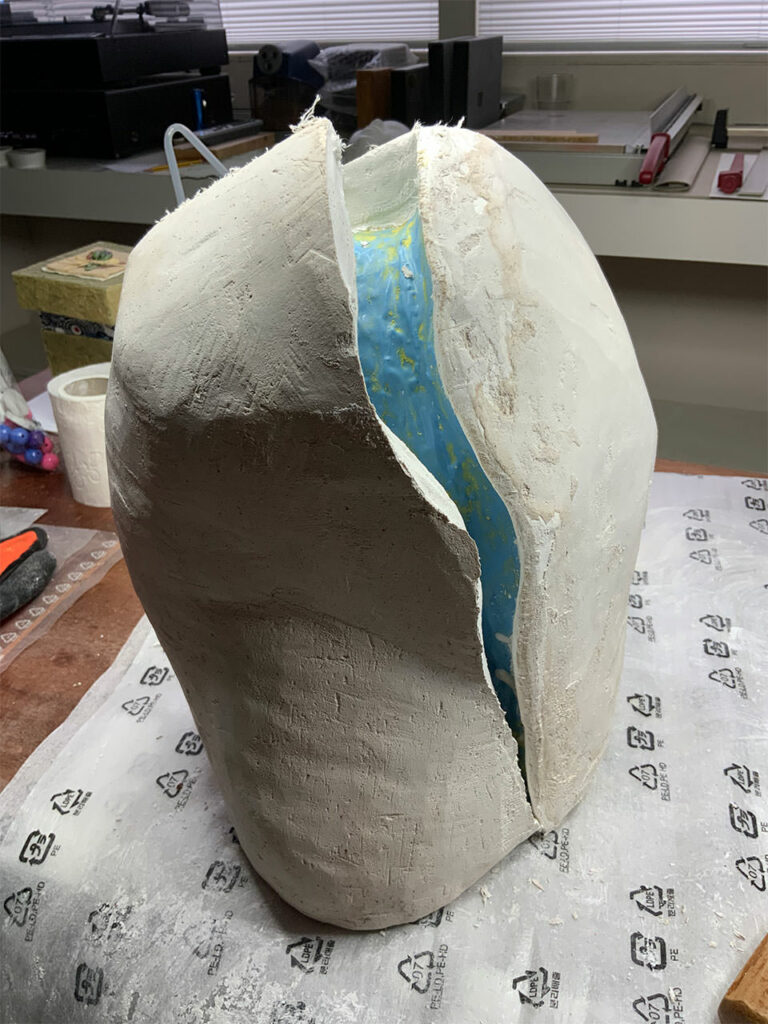
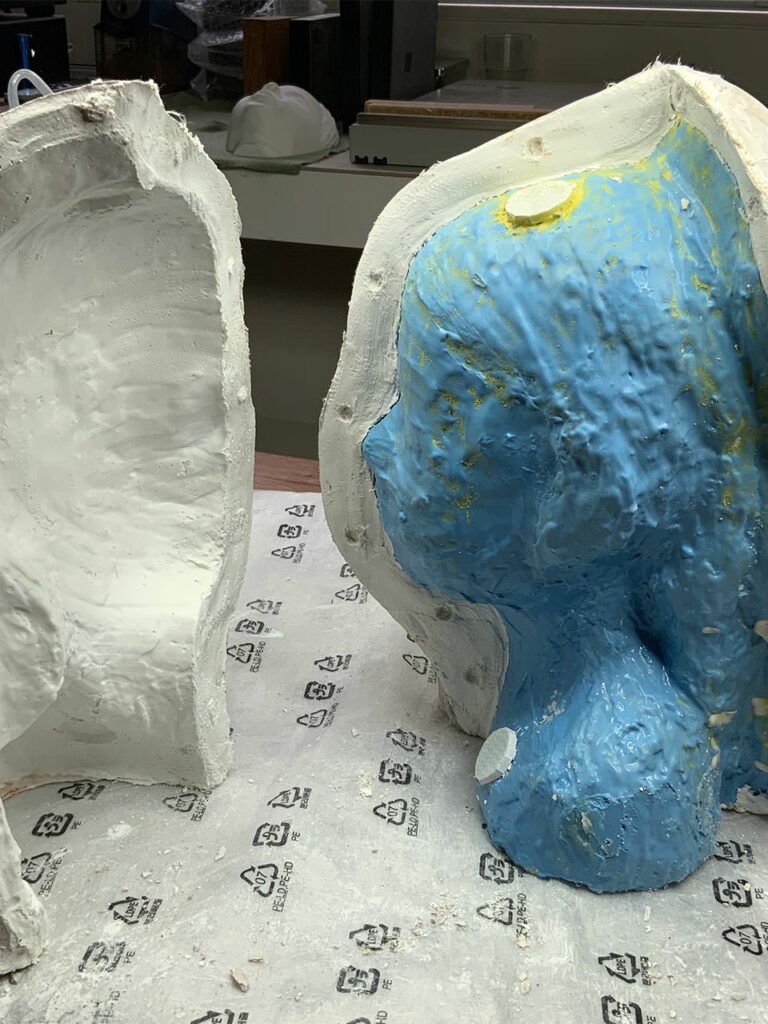
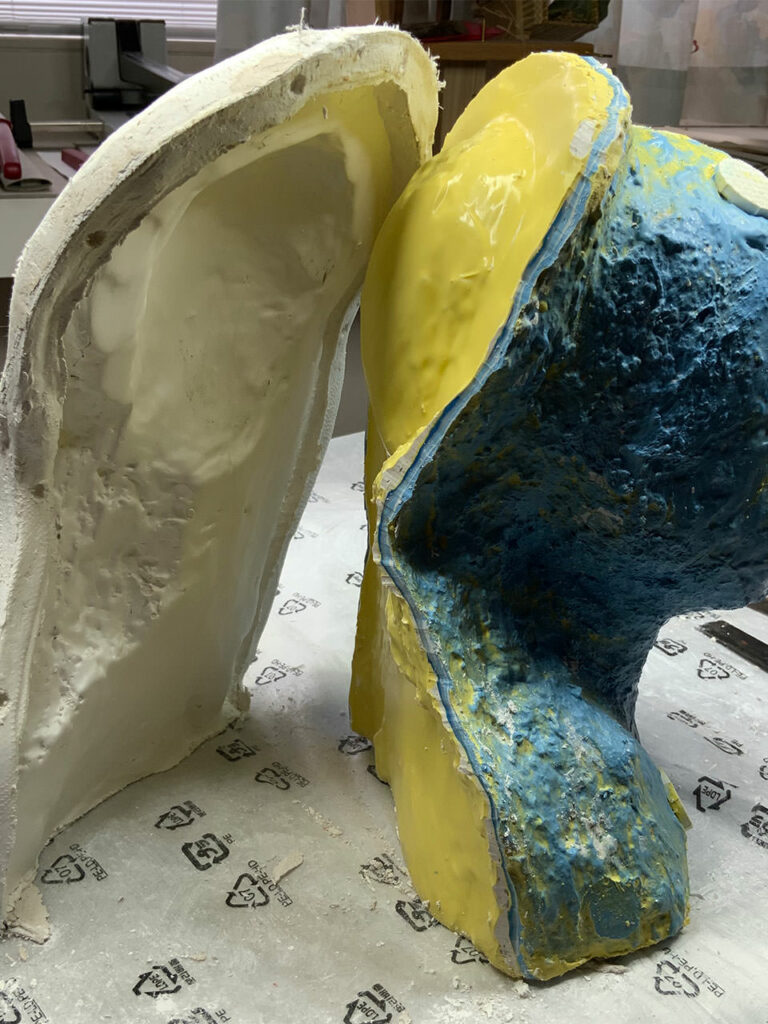
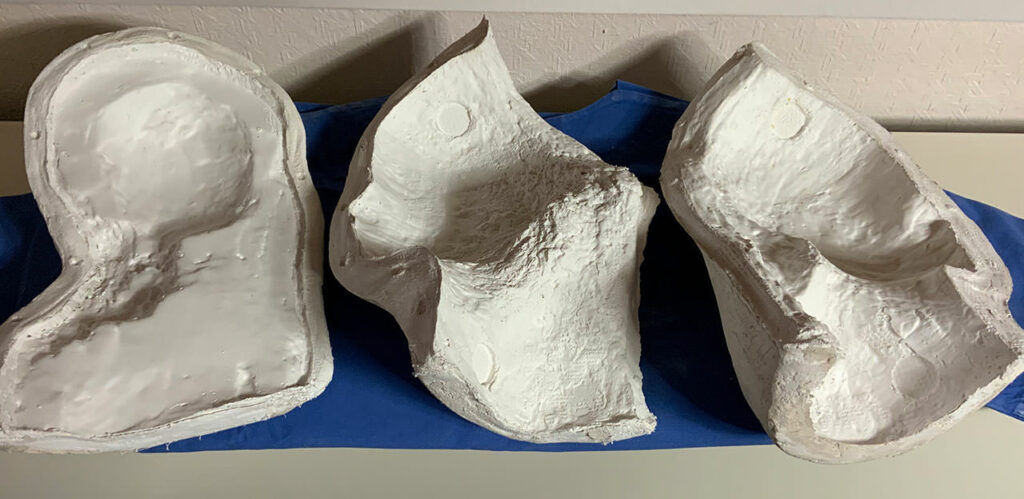
Die vorderen beiden Hälften werden zuerst mit der vorderen Silikonform befüllt. Die noppenartigen Erhebungen (blau) sind meine „Passmarken/kento“ und erlauben das exakte Einpassen des Silikon-Gegenstückes (gelb).
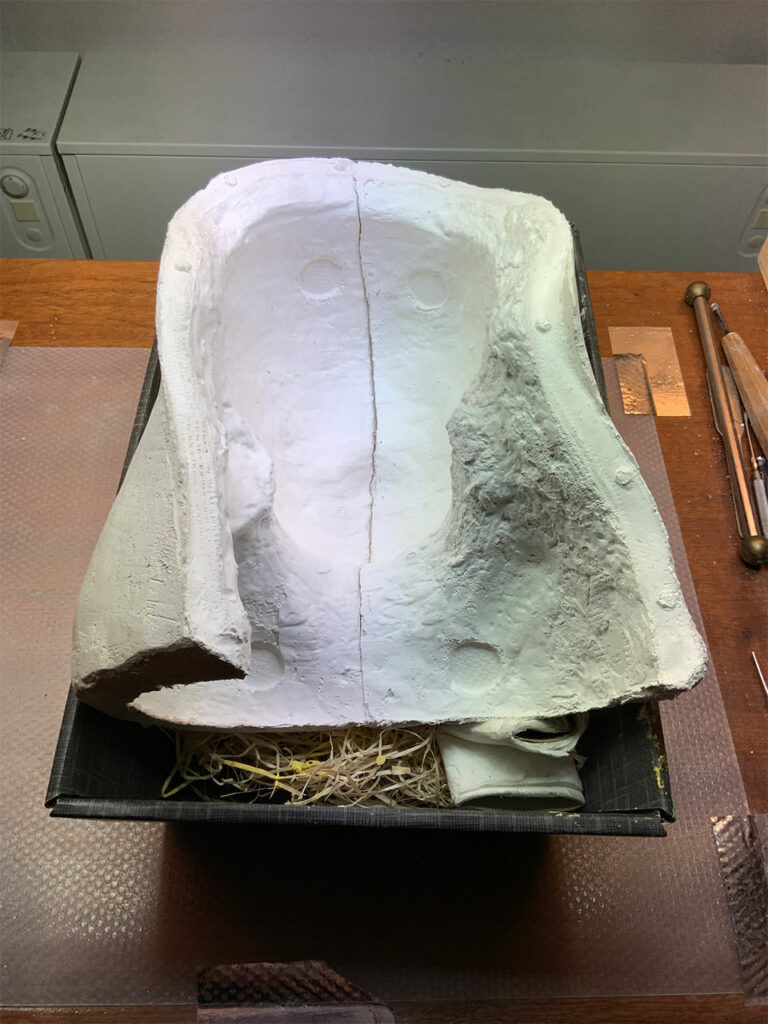
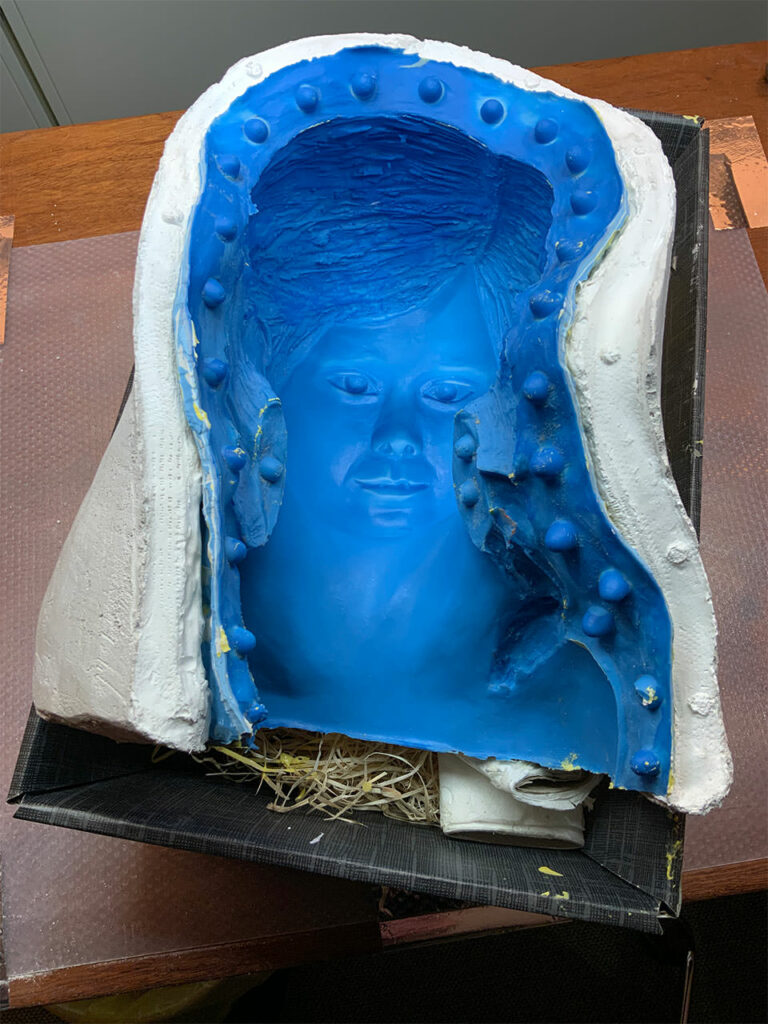
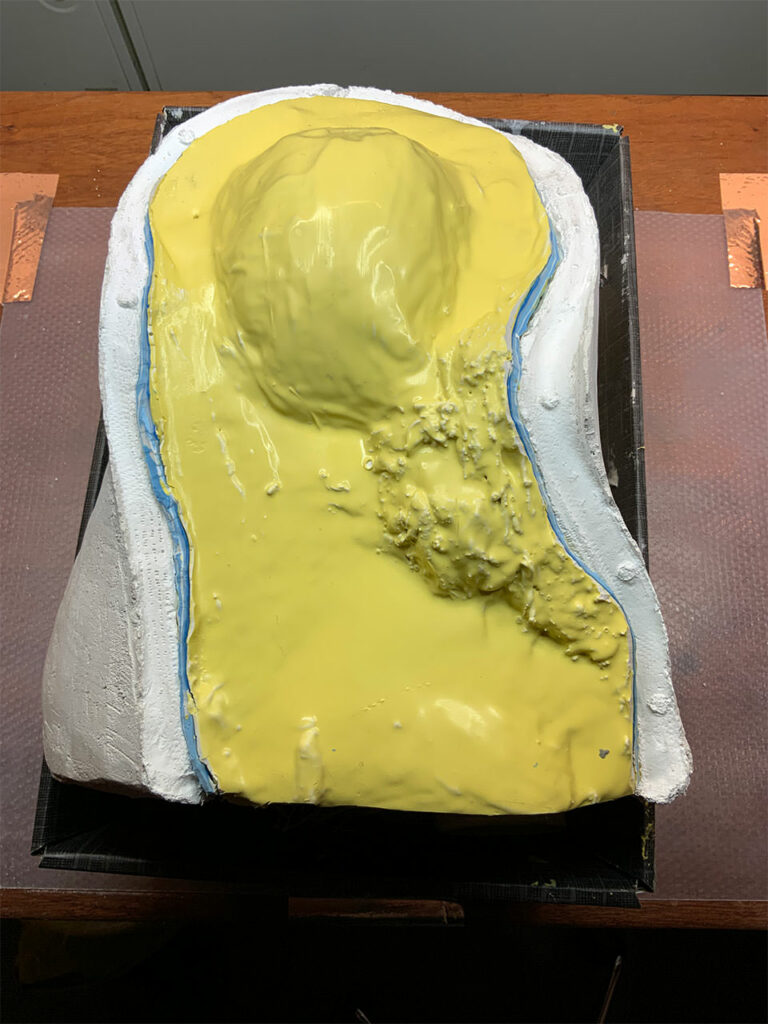
Zum Schluß Gipskappe III: Die Passmarken im Gips sind bei dieser Schichtdicke nicht so deutlich und effektiv wie die im Silikon, aber es gibt genügend Unregelmäßigkeiten zwischen den Gipshüllen, die eine saubere Adaption ermöglichen. Jetzt kommt das Verzurren unter Zug mit Spezialklebeband und dazu der Blick von unten zur Kontrolle der möglichst präzisen Anpassung der Silikonformhälften!
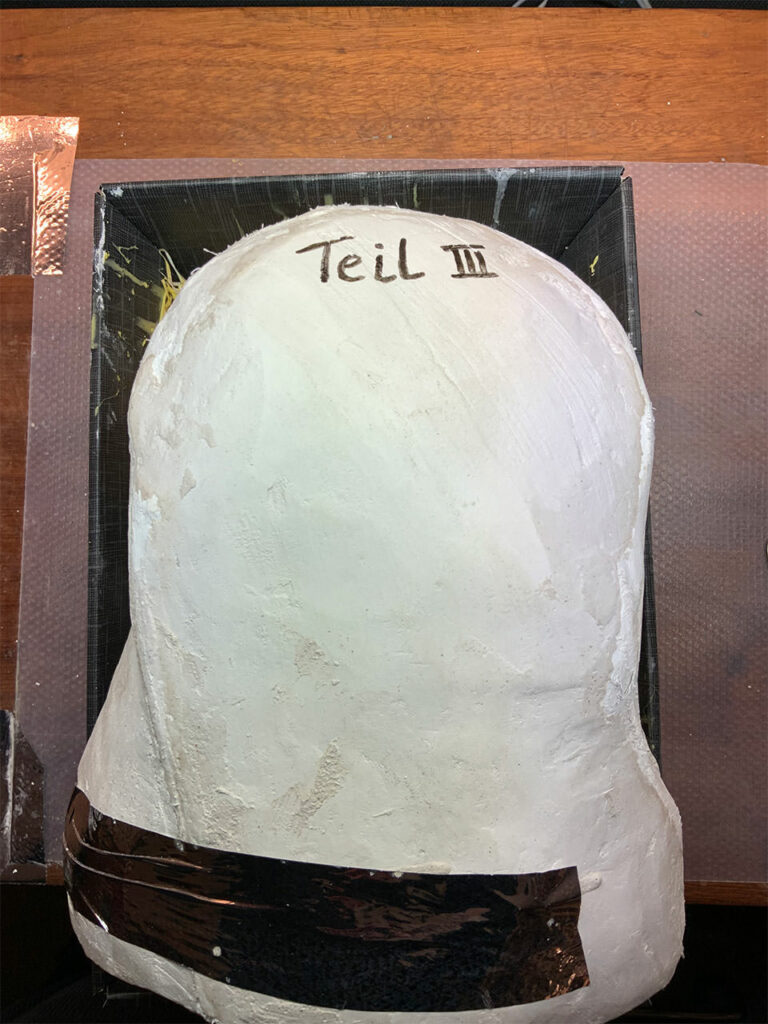
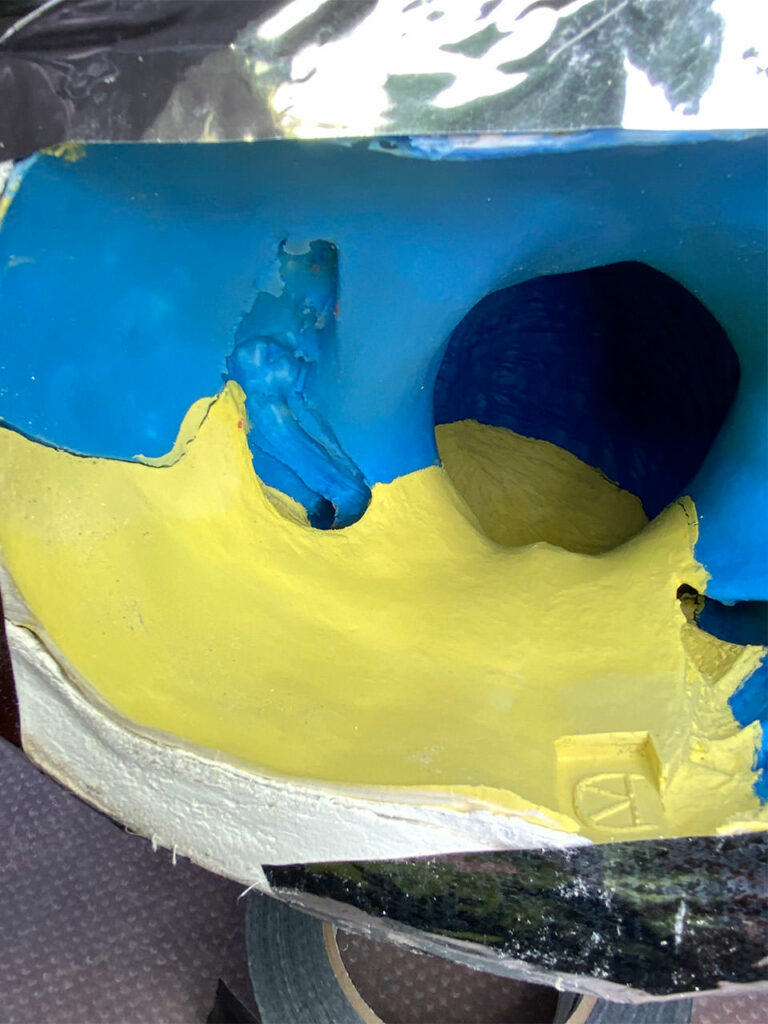
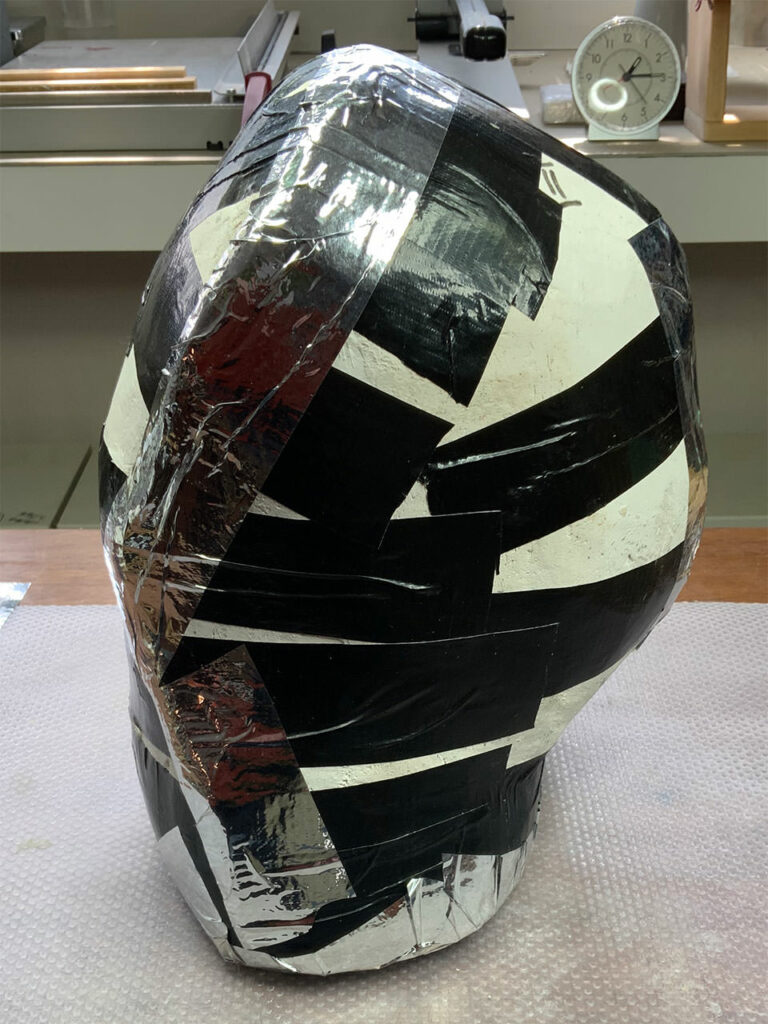
Auch den umlaufenden feinen Spalt zwischen den Gipskappen habe ich überklebt, so daß KEIN FLIESSGIPS AUSTRETEN sollte, aber einen Minispalt kann man einfach nicht ganz vermeiden. Statt der „Verpflasterung“ praktizierte ich kürzlich noch eine andere Variante, die Verschmierungen der Gipskappen äußerlich verhindert: umwickelt man die gut schließenden Kappen ganz fest mit Frischhaltefolie mehrfach, so entsteht ebenfalls eine sehr gute Fixation, so dass der Druck der einzugießenden Gipsmasse die Form nicht auseinanderdrängt und so auch nicht zu vermehrtem Fehlaustritt an den Kontaktstellen der Silikonform führt! Nun wird die Gießform dann aufgestellt – gesichert mit Holzwolle in einem Baueimer.
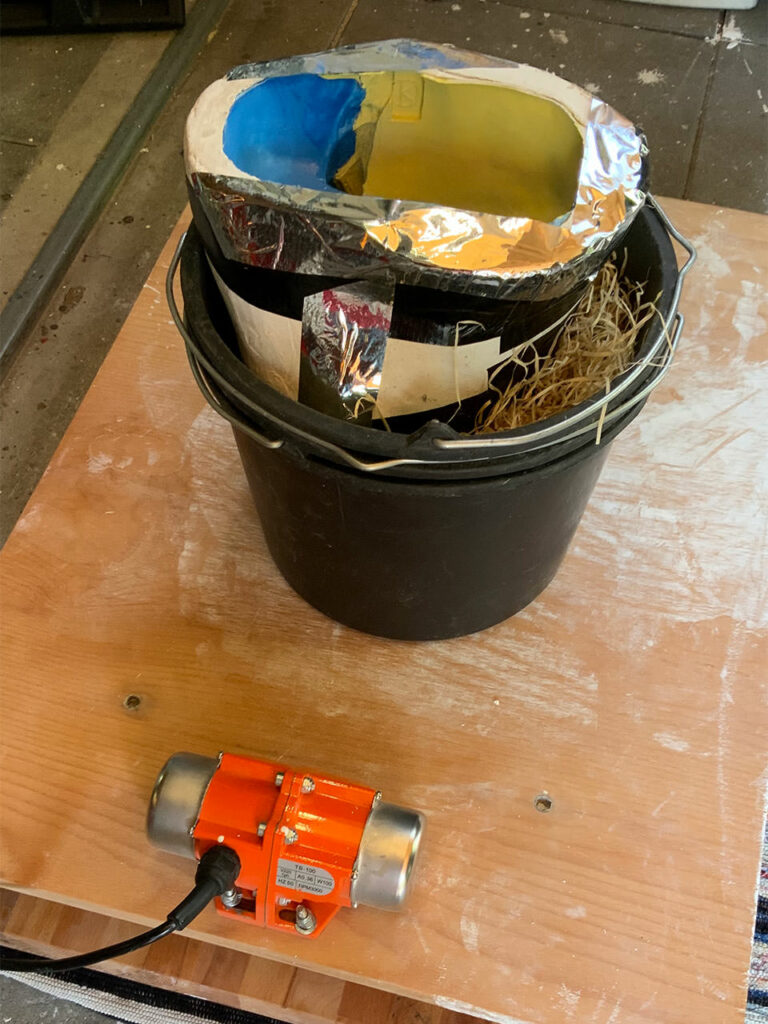
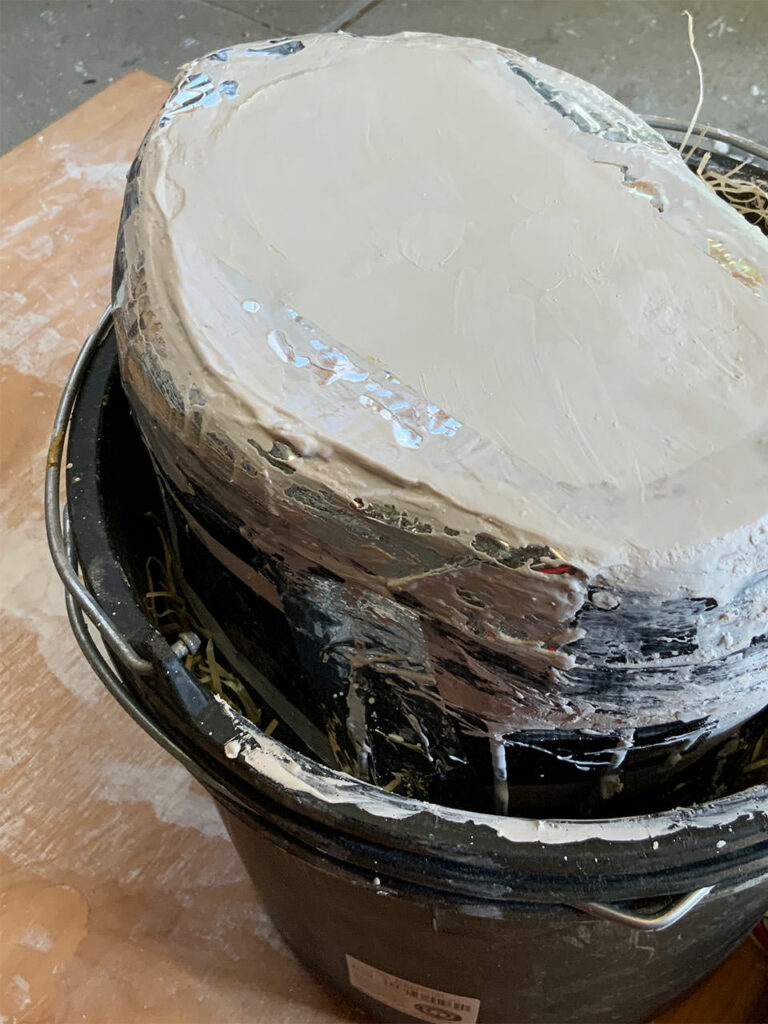
Das nötige Gipsvolumen für den Vollguß hatte ich zuvor nach dem archimedischen Prinzip durch Eintauchen von Gretas Büste in einen prallgefüllten Wassereimer ermittelt: 4,2 Liter.
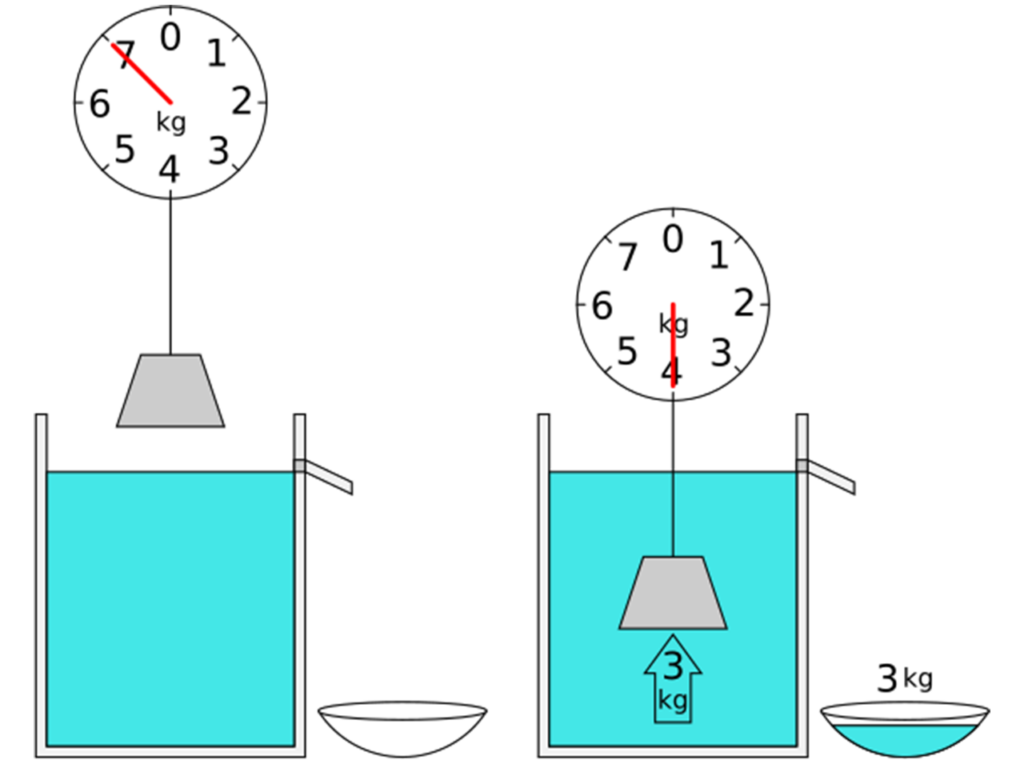
Nach Abwägen der Gipsmenge und der dazu passend kalkulierten Menge an destilliertem Wasser wird dieser per Hand eingestreut und ggf. sicherheitshalber noch ein Abbindeverzögerer beigemengt. Das eigentliche Vorgehen beim Guss habe ich weiter oben erläutert – im letzten Absatz des Kapitels „Gips ist nicht gleich Gips“.
NACH DEM GUSS
Feine Gipsaustritte aus den Silikonformteilen und der äußeren Gipshülle sind normal, ziehen aber eine Reinigung der Formteile zwingend nach sich, denn sonst werden diese nicht mehr exakt aufeinander passen und noch viel mehr Gips ausfließen.
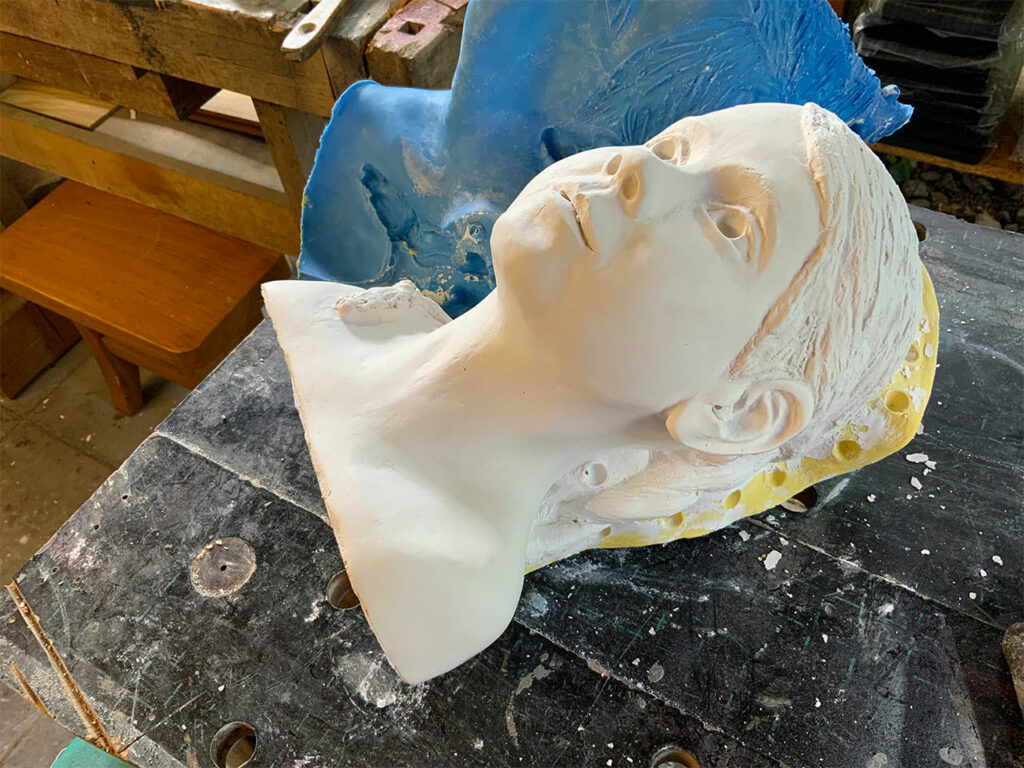
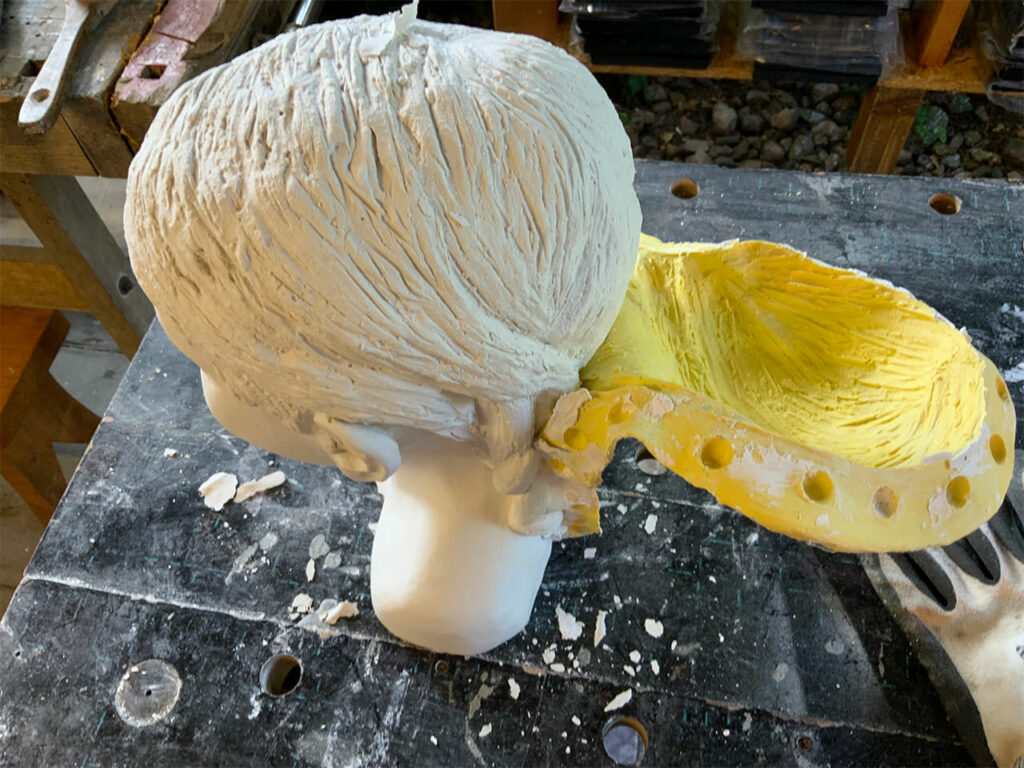
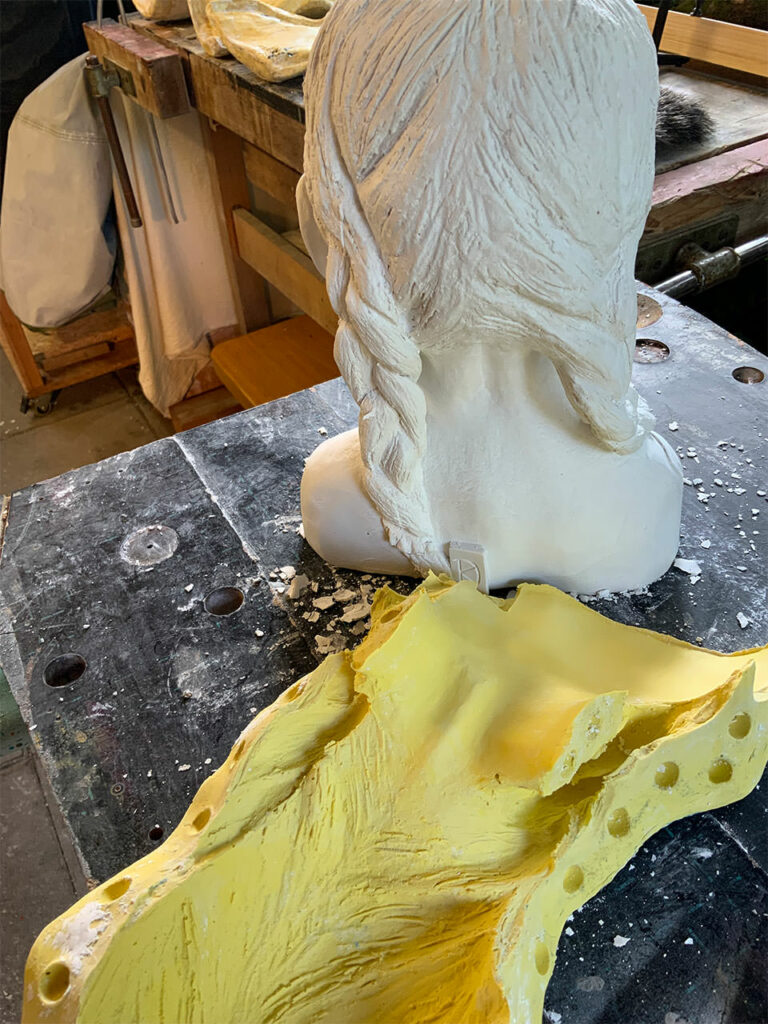
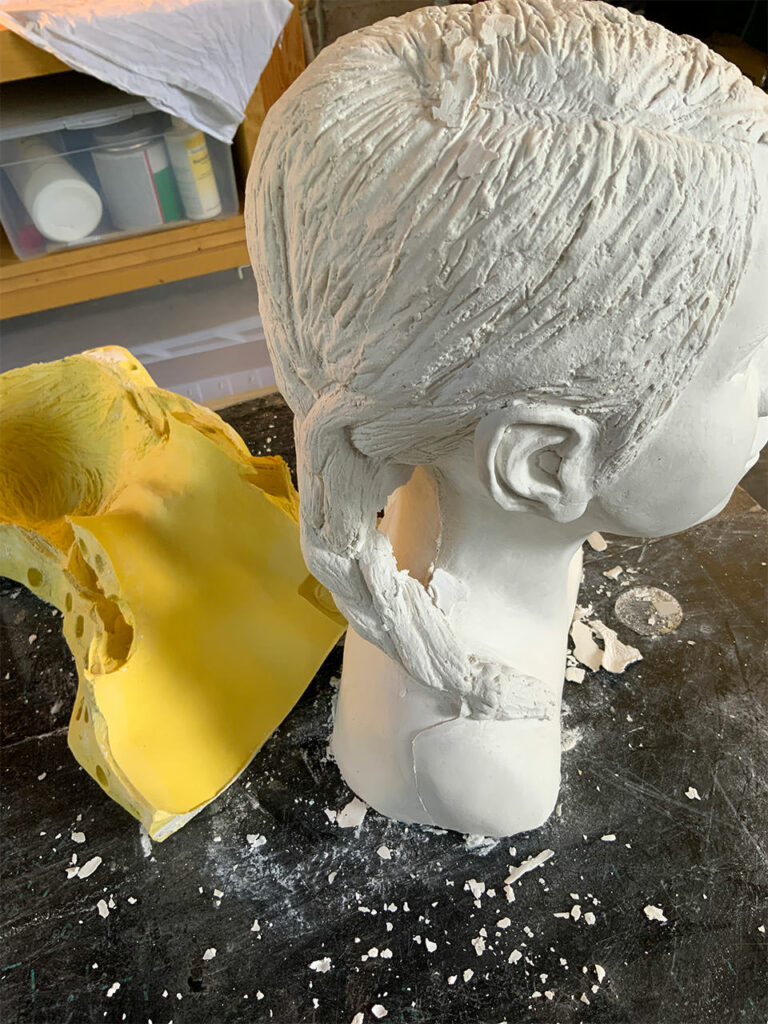
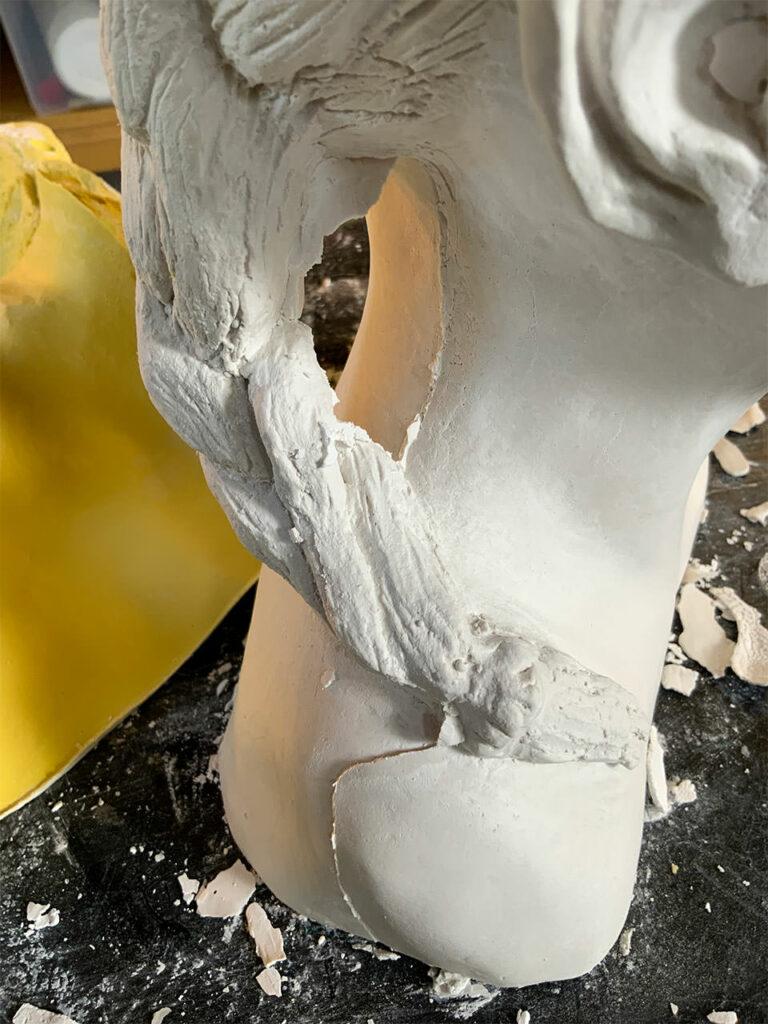
Wenn man diese doch umständliche Abformungsprozedur insgesamt sich vor Augen führt, dann braucht man eigentlich den Ton tatsächlich nur zur ersten Modellierung – es sei denn, man erfreut sich und schätzt als Endergebnis allein das „Irdene“ des Tonmodells.
Ausformungen im schnell abbindenden Gips lassen sich ja kaum machen und selbst wenn die erste Formung in Ton nicht wirklich perfekt gelang, so kann man aber davon eine Silikonabformung fertigen und nach dem Ausgießen mit dem entsprechenden Fließgips ergibt sich immer noch relativ leicht die Möglichkeit feiner Nachbearbeitung, einer Optimierung der Gipsform bzw. des Gipsgusses. Letztendlich gelingt so auch das Abdecken kleinster Farbdifferenzen bei unterschiedlichen Gipsdichten mit einem perfektionierenden Finish aus verdünnter weißer Abtönfarbe (mit hohem Pigmentgehalt).
FEINHEITEN DER NACHBEARBEITUNG
Wenn der gegossene Gips über Nacht in der Silikonform abgebunden hat, so kann man das noch feuchte Material sehr leicht bearbeiten, auch Oberflächen mit einem Baumwolllappen sogar glatt streichen. Dies ist gerade für die Kindergesichter eine tolle Nachbearbeitungsmöglichkeit.
Defekte Stellen durch Blasenbildung lassen sich am besten durch Zufügen des gleichen Gipses im feuchten Zustand des Gipsgusses ausgleichen, Grate aber besser in trockenem und dann mit 400er Schleifpapier. Und natürlich kann man auch die Strategien mischen, indem man die Stellen mit destilliertem Wasser anfeuchtet und schleift.
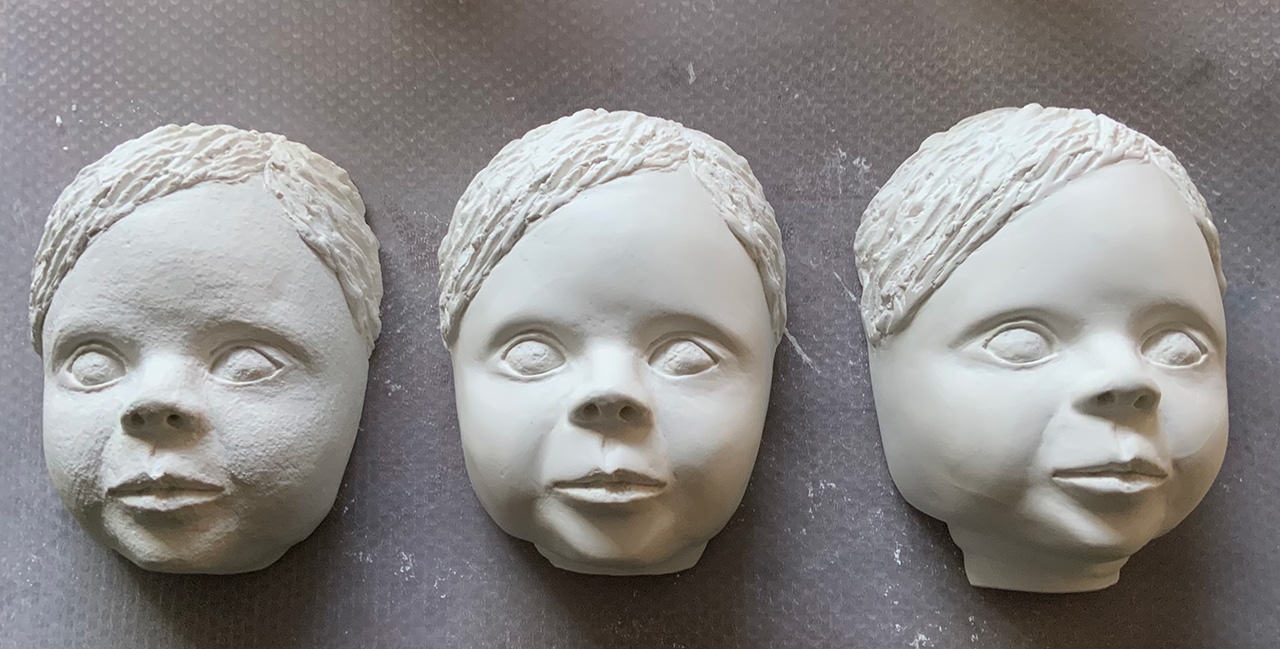
Mit dem Ton bei der Erstgestaltung bekam ich das nie so gut hin wegen der Schamottebeimengung, die aber notwendig ist für die Formstabilität bis zum eigentlichen Brennen und wenn der Ton erst einmal gebrannt ist, also knochenhartes Steingut geworden ist, dann kann man viel Zeit und Geduld für das Glattschleifen opfern – man will ja eine gute Oberfläche haben VOR dem Silikonabdruck.
Nun kann man diese Gipsskulptur in seiner zarten, fast sphärischen Weiße für sich als Endprodukt wertschätzen oder aber dann wiederum auch nur als Zwischenprodukt ansehen, es in Ölsand abformen und auf einen Bronzeguß abzielen als „goldenes Ende“ des Ganzen.
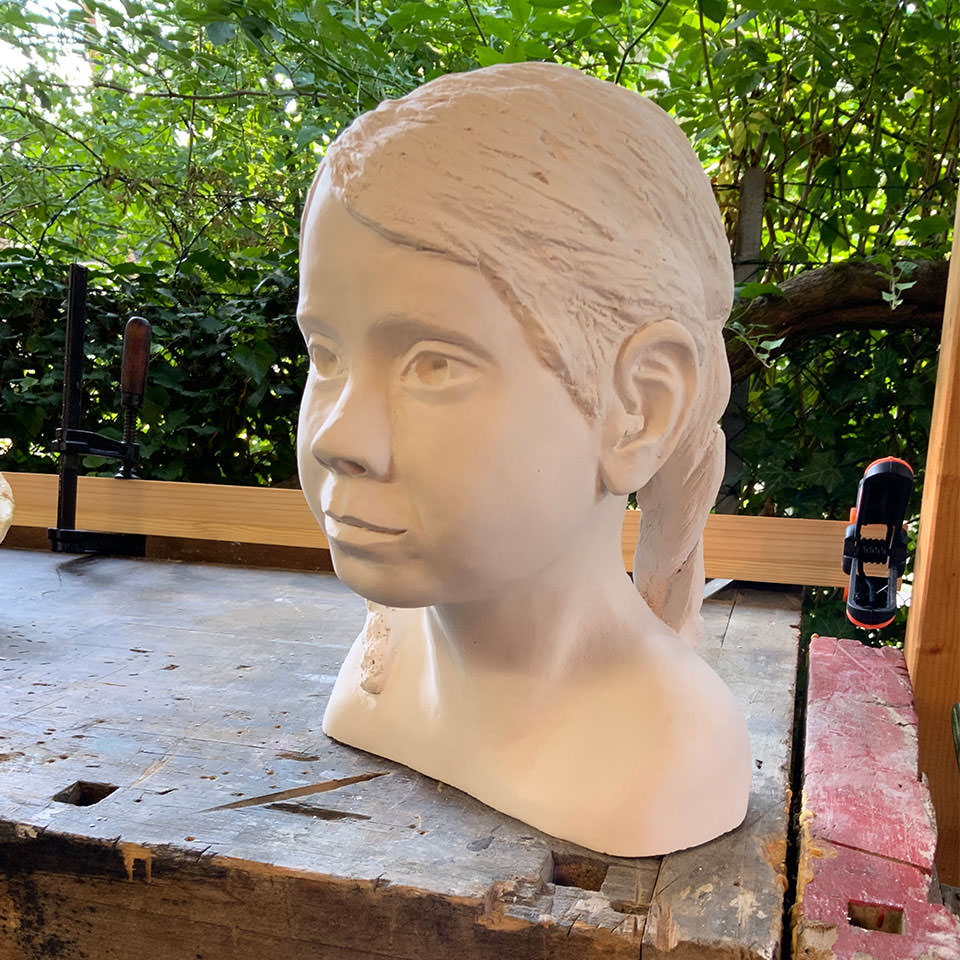